I'll bet not too many people have had this problem...
Well, I said I share experience on this project, both good and bad - this weekend a bit of a setback I'd say. Nothing fell down or got smoked, and no one was injured, so I guess I should keep it in perspective. I checked out the turbine this weekend, on what's been one of the few really nice days since getting through our sugar (maple) season. We'd had a steady, but predictable wind Saturday. I'd stopped it a couple of times by shorting phases via the controller. All seemed normal, so I thought I'd have a look-see and grease the tail hinge and yaw-head.
Everything looked pretty good except, as you can see, the coil sectors have shifted. I picked out the worst one that I could see for these photos:
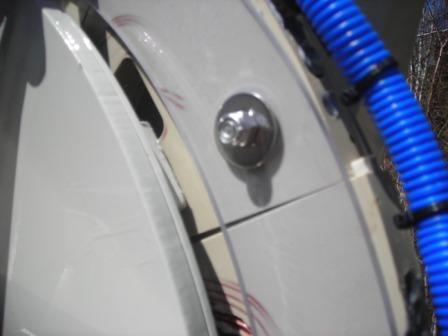
Torque on the stator, perhaps braking, perhaps just normal load & vibration is causing the sectors to rotate and slide along the T &G joint

I loosened the mounts and was able to tap things back into position. Retightened and we're operating for now. The winds are starting to drop off seasonally a bit now anyway.
Thinking about it two possible solutions; I welcome others:
1) I could drill and add a second through bolt in each coil. The original design had two; in hind-site I probably should have left it. Similar to this:
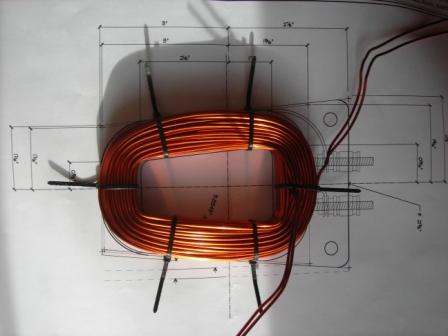
2) I wonder about the possibility of
flipping the stator. The sections are rotating about the stator bracket mounting bolts. And, compression at the inner part of the sector seems to be causing the neighboring sector to shift outward on the unrestrained side. I wonder , if it were reverse, if the same compression would end to tighten or bind against the next sector(s), while the arm of the bracket would be in tension. Here's a flip photo for a visual:

Glad it made it through the winter, but got to work this out. I welcome suggestions. ~ks