This is a copy of another thread I did on a site that France has made difficult for folks to see... and some wanted to see it..... I don't understand it... but..
It has been slightly modified to reflect the 5 picture count that this site has, so is broken up a bit.
================================================================================================================================
It's time to put some practice down in a how to style rather than a Q and A thread.
To make a nice 6kw unit that will truly do the 6kw rather than the not so real figures bandied about by PJ, we need first and foremost a better transformer.
This is easily done in Australia by procuring "inspire" grid tie inverters off ebay for 50-80 dollars, and extracting the huge torroids from them. In this article we will assume you have procured two of them, and we will make a much better transformer than both of them put together, by making then a single core and then rewinding them. Torroids can be found in a range of other galvanically isolated grid ties as well... so we are looking for dead grid ties that are heavy ( 30kg plus)
This is a simple procedure, but one that requires patience and methodical action.... it is a true pain in the butt to do, but is simple, and a perfect foundation for your inverter.
The transformer you will create would cost around the $1800 region, if it was purchased in this country... this one I am winding will cost $120, and i will have two stainless steel boxes with ip55 rating as well left over, plus a range of very nice filters to quieten down the hash from the inverter if you want to. These grid ties have a few nice bits in them.
Here are the two transformers after pulling them from the box, and knocking the center out of them... I use a small mash hammer and a big drift to simply knock it straight through the center hole...yes it will go through....... you can drill it out if you wish like I did the first time... but it is both dangerous to the wiring and to you unless you have a good way of holding it very securely.... best just to knock it through... takes seconds, and no mess.

Once that is achieved, it is time to look at what we have got. A huge torroid the like I have never seen before. The figures on the side say 130v:240v 50hz on this one.

The 240v winding is on the outside, and the 130v winding is on the inside.... there are several ways we can tackle this.
We can simply tape the two together, join the 240v windings in parallel, ignore the 130v windings, and wind a secondary around the two transformers, and were done.
This will work, but you will struggle to get decent wire through the center for your new primary... so not worthwhile.
Next option.... we can strip the two 240v windings off the outsides, and be left with the 130v windings on each. This is not so silly, as the 130v winding is 2 in hand, so if we stack them together, tape them up, we can series these windings and get a 2 in hand 260v winding, and a much bigger hole in the center. This is an ok arrangement, and will work well... and very easy to do.
This gives us a 260v secondary.... this is a good thing, as the reason we are doing this anyway, is to get the magnetizing currents down... otherwise we need only buy the Powerstar W7, and we get the same kind of honest power, but 5.5kwh/day losses because of the E I transformers they use... very lossy. It's that simple, if they used big decent torroids, we would not need to change anything.
So if we can "overwind" a bit, we decrease the strength of the magnetizing current needed to run the thing, so we can get the idle currents down even further... ie for a given field, it is amp turns... so more turns, less amps..... and the magnetic field in the steel can be decreased as well, and this will mean the magnetising currents will be less.
It is likely that the original configuration will be close to saturation, and a look at the graphs for this will show a non-linear relationship with current and field strength as we get progressively closer to saturation.
So if we can back off from that point even a little bit, we will get a more than linear decrease in magnetising current.. so all good.
One draw back with this approach is that you have to live with the transformer noise. This may not be an issue if you locate it well away from your living environment, but can be a nuisance if you work next to it all day.
The second draw back, is that you can get rid of a pound or two of copper, if you rewind it as a single transformer from the start........ ie those wires that are pressed together between the cores where they meet, can be gotten rid of entirely. Each transformer can then loose 1/4 of it's resistance from copper loss, and that pushes your power handling up.
Saturation: When you have designed the transformer, and it runs fine, you cannot saturate if from overload if you have a sine wave source... contrary to popular opinion.
A lot of folks think that overloading the transformer brings it into saturation, but this is not so...
If you look at the equations, you need a frequency change or a voltage change to saturate the core... load current makes no difference.. nix....
So providing your inverter does not clip, you should not saturate the core, no matter how hard you press it. All this extra current put into the system will be working against the wire fields as MMF and back MMF, the magnetising current remains the same... so I think the load losses are in the copper... so if we can get copper R down, we are well on the way to more power for longer. ( eddy currents and hysteresis will also play a part, but not much in a torroid comparatively.)
ie any transformer ( because we know the core does not saturate from over loads) can take large currents...so the output current is only limited by the heating and regulation ie can be massively overloaded for short periods. The voltage will sag in proportion to the copper losses, but provided it is released before it burns up, it will survive... but it won't saturate.... so.... a 100w tranny will stand say 10kw..... but only for maybe milliseconds before the copper fuses.. this is extreme, but you can see what we are driving at. Basically the difference between a 1kw and a 10kw transformer is how fast we can keep temp from rising beyond safe. ( alright, the voltage regulation will be total crap too )
So a 2kw transformer may handle 10kw fine if it is...... say .....oil cooled, and so becomes rated at 10kw. The grid tie ones are inside a sealed box, so are "under rated" so to speak because they have little chance to get rid of the heat, but must run all day at full power or for a fair bit of it, so although they are rated at 1.5kw inside the box at 100% duty cycle, once outside, and with most of the windings gone, they are very much increased in power handling ability.
Edit: I edited the above, but it is still yuk, the idea is there, the expression is not....... but you get the idea.
Thats why the PJ can do the 8kw for a short period of time, sadly, the transformer gets hot fairly quickly... but the cores will do it fine... the copper won't. PowerJack has taken this to extremes, and sometimes uses a single transformer with a fan instead of two transformers... obviously hoping for a very low duty cycle.
So after all that, the next possibility is to unwind it totally... and start from scratch.. with three cores used, we could loose a complete transformer worth of copper, with 2 cores we get rid of 2 sides of wire..... so our copper losses get less, and if we want we have the option of more copper as well, as the hole size remains the same, but the turns is decreased by half or 2/3rds ( depending on core count)
I have done all three styles. A complete rewind is best for noise and performance.. so the suffering is worthwhile.
Moving right along....
Here we are with some of the tape coming off. We use a small former of some type to roll the plastic on. This is to be reused, and is an easy way to unwind, and rewind... and is boring as hell....
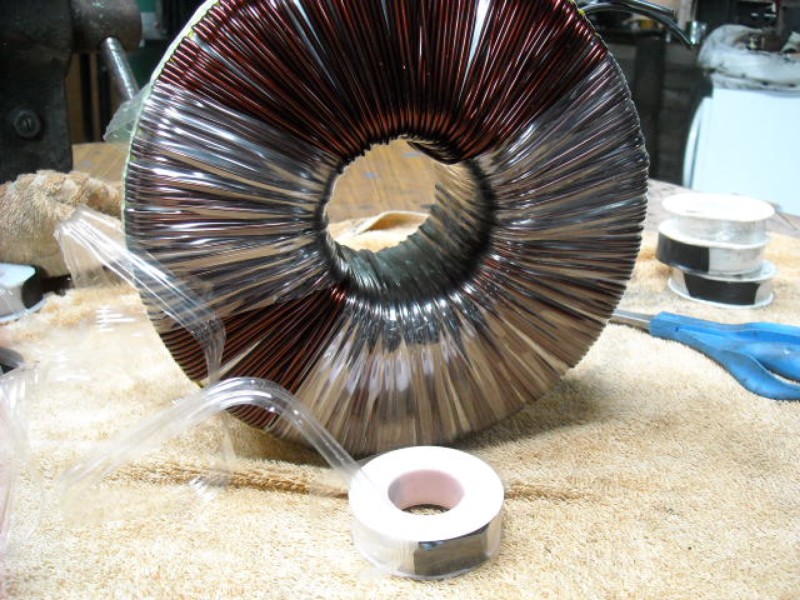
And here we are with the plastic off the outer layer:

Here we can see the unwinding stick. It is about 800mm of 6mm x 38mm steel, with notches in the end to take the wire. It must be fully insulated with a few layers of tape so that the steel cannot touch the enamel as you weave the thing back and forward through the core.
There is a right and a wrong way to use this, and if you look at the wire as the stick is passing from right to left, you can see that the wire being unwound is on top of the stick, this will stop horrible kinking, and make it very easy...... you'll be surprised how unfit you are until you try this for a few hours.
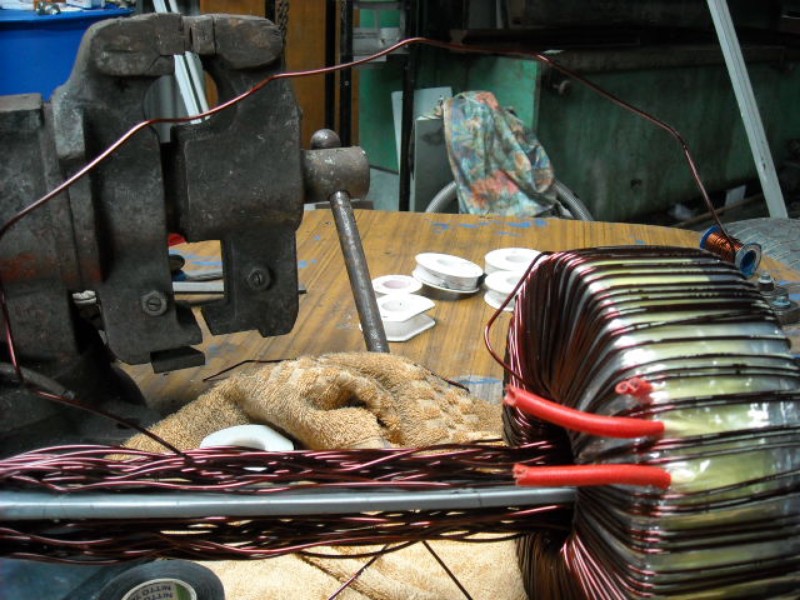
Notice how kinked the wire is on the stick... once we get a layer off, we need to straighten it out.... first step is to hook it onto something solid....and give it s stretch..... thusly. The kinks get worse as we get closer to the core.
5 pics is it for this site, so we will have to go again.
.......oztules