Finally managed to make some progress! This alternator started out as a 24V, 140A unit fitter to a Kawasaki 80 Wheel Loader. It has a 12 pole rotor just under 6" in diameter and is 8" diameter overall. There are 18 overlapped coils made up of 6 x 3 phases in the stator. Each phase is made up of two conductors approx AWG 16 wound in parallel. In an attempt to make it more suitable for use in a wind genny I have made some modifications. I have fitted 24 neos to the rotor, tapped the windings, removed the internal rectifier and re-assembled. I have retained the brushes and field windings.
Rotor with mags fitted:
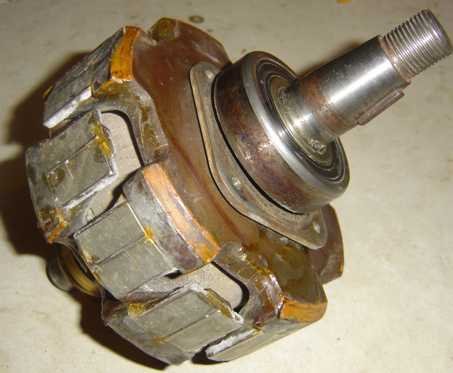
Assembled Alt showing tapped windings connected in series 'Y'. Note the 12V, 60A alt for comparison
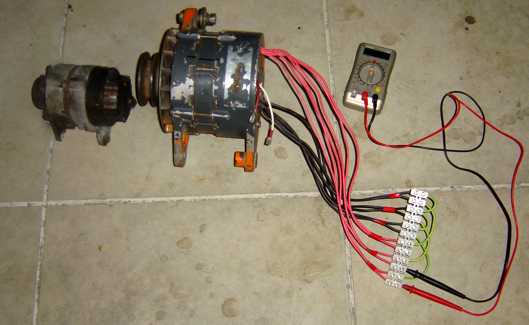
Preliminary testing is showing some promising results. As expected, adding the mags has produced a cogging effect, however this is less than I get from one of my standard F&P smartdrive motors (probably closer to the 'de-cogged' version). With the windings connected in a series 'Y' and not using the field coil, I can get about 10Vac between two phases by giving the pulley a hard turn. If I maintain a constant 1rev/sec (very approx by hand!) I get about 2Vac. This indicates a 24Vdc cut-in speed of around 500rpm.
I was initially unsure as to what effect the use of the field windings might have in conjunction with the permanent mags. I was hoping that I would be able to boost and/or retard the flux that the coils see so as to boost output and/or reduce cogging on startup. I connected the field coil up to my bench supply and supplied it with 24V (~1A). This noticably increased the 'cogging' effect. Giving the pulley a hard turn now produces aprox 15Vac, a 50% increase! It is not possible to maintain 1rev/sec because of the increased cogging, but 2rev/sec gives 5-6Vac, once again approx 50% improvement and closer to a 300rpm cuttin. Reversing the field current drastically reduced the cogging effect - it is still there but barely noticable! With the field reversed the most I can get by giving the pulley a hard pull is 2Vac.
Ultimately I am looking for 2+kW at 1000 alternator rpm and intend to use 1:3 gearing for my turbine. I realise that this 'testing' is very approximate but theyes give me some hope - enough at least to make sure I get a proper test rig set up this weekend so I can load this unit up and get some accurate results.