I am in the process of doing a couple of induction motor conversions - and I sure would like a good way to test the output.
It's important to know since you can't really make a set of blades unless you have some idea about the output (and input) the alternator will need.
So I decided to put together a power unit that could drive a variety of alternators. I don't know what it is about Briggs & Stratton motors, old ones seem to follow me home like lost puppies. I had 2 - one with a good bore, but over and eigth inch of end float on the crank, and the other with a trashed bore but good end float.
So I took the sump off the one and put it on the engine with the good bore, even got very lucky with the gasket (reused it!) After a little fiddling around with carbs and diaphragms etc. I've got a great running unit that starts easy on the first pull.
One oddity is because the good sump was off an older engine it had a low style oil fill. The motor it went on had a high style oil fill. So now there's two oil fills!
The bad sump:
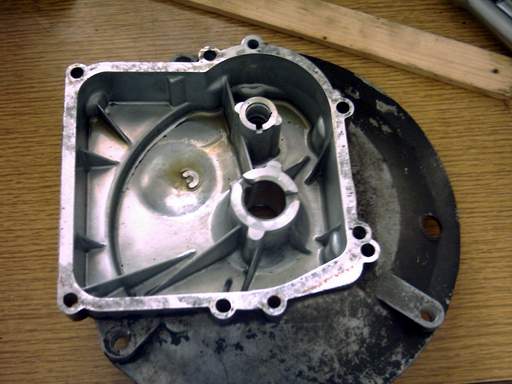
The thrust suface around the crank bearing is trashed.
So next I went to Home Depot and bought a bunch of eighth inch by 1.25 inch angle. About $40 worth. This was the most expensive part of this project. It would have been better to get the steel at the scrapyard.
I marked it up and cut the pieces with an abrasive wheel in the circular saw, which works pretty well. There's a top and bottom frame 12 x 24 inch, 4 uprights, and 3 motor mount tabs.
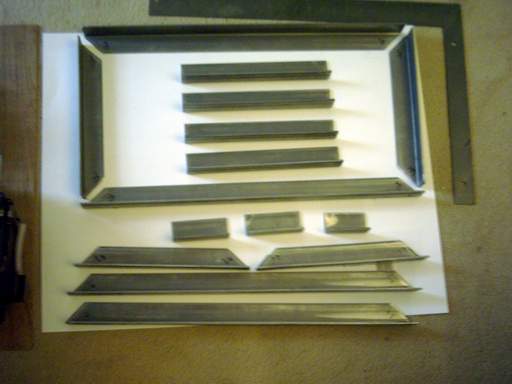
I read a tip from TomW a while ago about collecting metal shavings. Use a bag with a magnet in it, then just turn the bag inside out, take the magnet off, and throw it out. Thanks Tom that saved a lot of cleanup time.
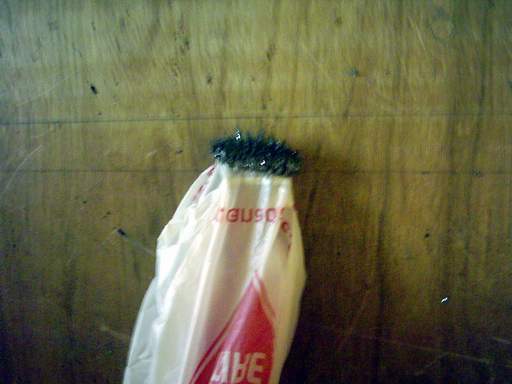
A friend of mine is a lot better with an arc welder than me and kindly agreed to a bit of welding:
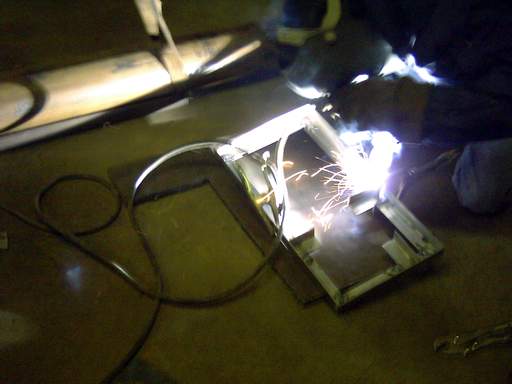
Next a trial fit of the motor to locate some holes for the motor mount bolts:
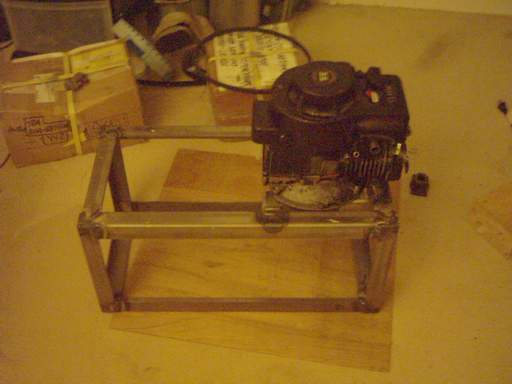
A bit of paint and some wheels from an old lawn mower:
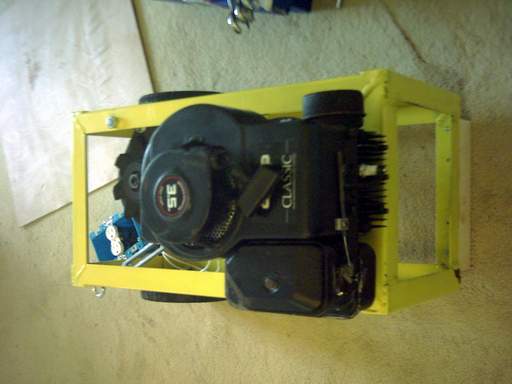
Just for fun I hooked up an AC Delco alternator to it. I rewired the stator star and full fielded the rotor. It gives about 95 volts AC but the motor is really working into that load.
The shape of the frame means it's easy to attach different things to it.
For the induction motors I'll be making a jackshaft with some stepped pulleys to give different speed outputs for testing. It should be possible to get from 100 to 400 rpm and with that reduction there will be enough torque out of this little motor to test the alternators I'm doing right now.
Bigger alternators will need a bigger motor - but this will probably do for now!
Project cost - about $50 including the paint.
Fun!
Ted.