Too easy!
Big fun!
The ones about like that I did have 2 sets of windings, start and run.
The wires are too small to seperate... for me.
I only seperated the starts from the runs.
Test the lead to lead ohms, say 50, 100, and 150 ohms.
The 150 ohm reading is from a single end of both sets (red to blue?)
The other (black probably?) goes to both windings, 50 ohms to one wire, 100 ohms to the other. About like a center tap.
Carefully snip string and paper to find the end of the end where it is connected to 2 wires. Cut only one. Add an output wire to the coil wire just cut loose.
Now there are 4 output wires, 2 seperate phases, to be rectified seperately.
Turn or machine the armature for 6 magnets, N-S-N-S-N-S.
Do somekind of decogging measure, because it'll cog!
Don't glue the magnets down until the cogging is fixed.
A 2 liter bottle cut flat and twisted like a funnel helps get the rotor in without damage.
Expect some extreme voltage (over 100VAC) at low RPMs, but a very low amps.
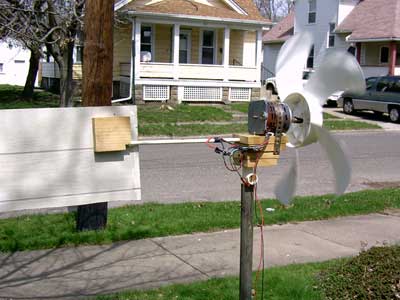
G-