My latest blade set, started on new years day. Made from #2 lumber yard SPF 2x6x10ft. $15 each. The blades are sandwiched in a hub of two 3/4" thick disks 36" dia. Each blade is attached to the disks with 6, 1/4 bolts . By the third blade I had it down to 4 hrs.
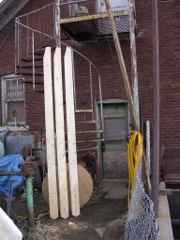
I used theese tools
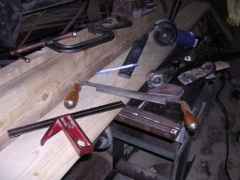
My favorite is a HF grinder, With a 4 1/2' 40 tooth carbide blade brazed on a 5/8"nut. It warped like a potato chip, but did not seem to have a bad effect. It carves like the wood is hot butter. HF sells 2 chain saw type cicular saw blades for about $28 and $32. The 40 tooth carbide blade was $3.99, much better.
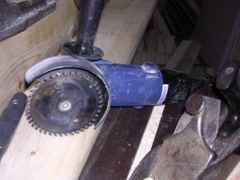
I start by marking the blade tip for thickness, 5/8" and pitch 3 degrees. I anchor the blade root horizonal and then use a protractor level on the blade tip in case the board is warped.
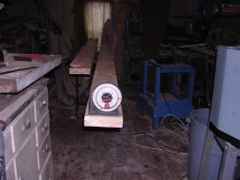
The first blade is planed and rough disk sanded. That is as good as I will make it. Each board started at 15 lbs and ended at 8 lbs. The disk were 15 lbs. each.
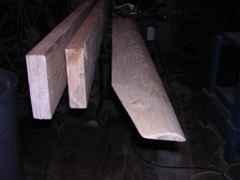
5/16 holes are laid out and hand drilled through the stack of hub disks with the blades c clamped on top. Amazingly all the bolts pushed in. I had held the drill square.
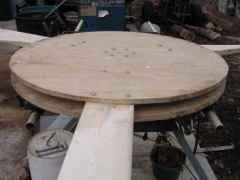
I then put on some old cotton work gloves and dipped them in dark used motor oil and hand rubbed about a quart of it on to the blades and the two plywood disks. I think they look better and it shows the grain.
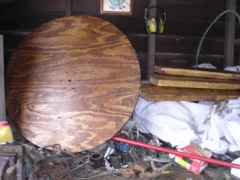
This will be in a urban area below roof top level with poor wind. Theese blades will replace the 13 ft dia. blades on this mill. The 13 ft ones would stall when the 125 amp GM alt would entergize.
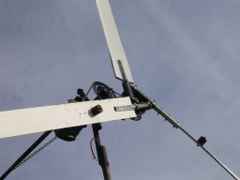
Next blade experiment might be with 2 x 12 x 14 ft lumber.