part grams Oz radius radius cm oz/in g/cm
Timkin 471750 123.00 4.34 1.24 3.14 3.51 39.21
w/o spring 94.00 3.32 1.24 3.14 2.68 29.97
Timkin 32x50x82 186.00 6.56 1.24 3.14 5.31 59.29
w/o spring 155.00 5.47 1.24 3.14 4.43 49.41
Dexter stock 124.00 4.37 1.24 3.14 3.54 39.53
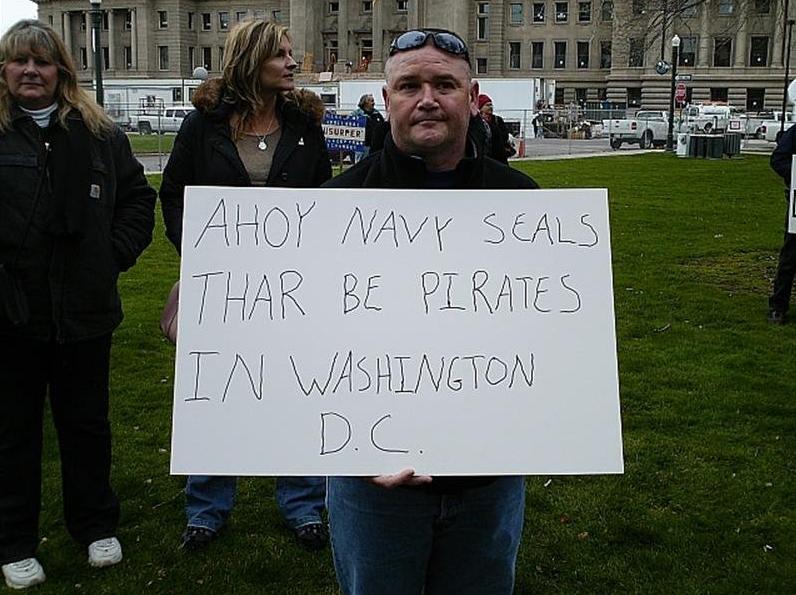
Testing rig
Procedure - spindle shaft where seal was to ride was polished. Bearing was nylon on steel and oiled. Seal was installed in holder, seal contact area was lubed with 5-30W oil between each test. Water was added to bucket until it started to move, bucket and water was weighed. For each condition this was repeated at least three times. The weights were recorded. There was little deviation in the weights.
Conclusion - "It ain't worth it." If oil can be used as a lubricant, the seal drag is in ounce inches. The spring adds some. After 'running the numbers' it is apparent the standard seal which does not have a spring is about as good as it gets. Foot pounds are .021 to .042. A horsepower is 550 foot pounds a second. At 600 RPM the seal drag is still less than .01% of a horsepower.
Research is a good thing. Until I actually ran the numbers "seal drag" was an unknown in my knowledge.
Ron