Pepa,
I'm glad to see that you are interested in and paying attention to airfoils, the heart of a blade.
The real issue here concerning rotor efficiency is airfoil Lift to Drag ratio (L/D).
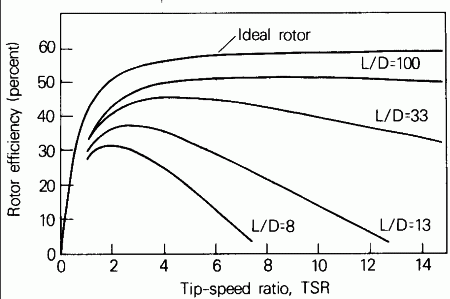
As you can see, almost anything works to a degree if you want to operate at a TSR of 2 or 3. However, if your alternator design requires a TSR of 7, you better have a high L/D if you want reasonable efficiency. Windstuff Ed once pointed out that even flat boards as blades can be 25% efficient. Rightly so, if you're willing to accept a low TSR.
Unfortunately, blade L/D is not easy to measure or predict. It takes a wind tunnel and special equipment. A generalized airfoil shape will have an unknown L/D as do probably most of the blades produced here.
I think we can say that using a section of a circular pipe as a blade will not have a very high L/D. Your example shows that the root area has something more approaching a generalized airfoil shape compared to the tip. Unfortunately, the outer 25% of the blade radius is where most of the work is being done. THIS is where it's more important to have a higher L/D.
Jondecker says that he is willing to give up 10% in rotor efficiency to have simpler construction. You may be giving up more than you think. An example:
Say you have wind conditions that produce 100 watts in the wind. With a well designed rotor of 45% efficiency, you extract 45 watts from that wind. A rotor of 35% efficiency obviously will extract 35 watts. This is 22% less power than than the better rotor. Efficiency counts!
What's the answer? Start your rotor design with a published airfoil with known parameters. It'll pay off.