I'm not good at metal fabrication so I looked into making the yaw bearings, etc out of pipe fittings.
I found Windstuff Ed's page of formulas for furling, entered them into a spread sheet and saw solutions with 45 degree tail angles so I went ahead and put one together.
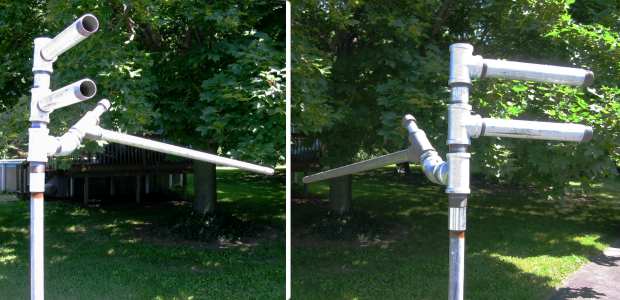
The first thing I noticed was that my tail drooped a little, about 6 degrees, but if reality matches the math then that should work okay too.
The tail would have been a little more compact if the supply house had a 1-1/4" wye. I got a 1" wye to use on the tail boom but had to use nipples and an elbow to get the 45 degrees off of the yaw bearing.
When everything is ready I'll get the parts welded up so they don't move.
Truth is I think the fittings look clunky and there's about $35 in pieces there. I imagine that's a lot more than if I'd made the parts myself but probably less than paying someone else do it...
More:
I got a used Saturn rear wheel hub off of ebay for $10, double checked the hole measurements, and emailed a DXF file to my laser cutter to get a hub mounting plate and two rotors; am waiting for those.
... the back cover on the hub popped off while I was hammering out the studs and I got a nice look at the ABS sensor. I got a notion that that'd be a good way to measure RPMs but there I read somewhere on the board about using a frequency counter on one of the alternator lines and that sounds simpler and better so I chucked that idea...
Reminds me of this anecdote: If two people come together and give each other a dollar then they both leave with one dollar. If two people come together and give other an idea then they both leave with two ideas.
I really appreciate that so many people share their ideas.
Thank you,
- Ed.