My drill press was very useful for testing this alternator. The hub's cylindrical dust cap (they're usually domed) allows a belt to be placed around the end of the hub and the chuck of the drill press is able to turn it. No pulleys required. The mount was cobbled together a bit to mount in the vise, hold the hub, and hold the stator in position. You can see the bicycle spedometer in the lower center which gives me a RPM reading.

The ½ HP motor of the drill press turned the alternator well in most tests. In some tests, the power of the press was not enough to maintain speed. Despite the press' inability to turn the alternator faster than this, the charging current curve up to this point was straight enough to expect it to be constant up to the stator wiring's rated current (about 20A).
With airflow on the stator, its encapsulation in an epoxy board, and the thinness of the stator, it's hard to tell in advance whether the stator will be able to deliver more or less current than that, without burning out. Only experience will tell.
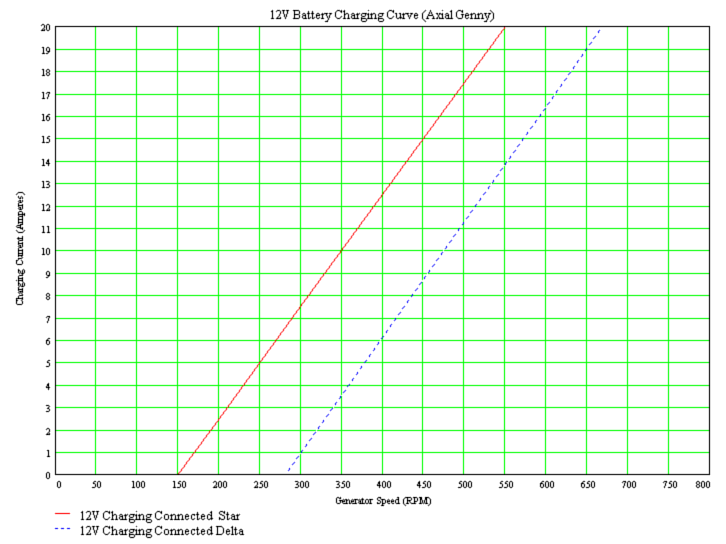
Resting with the 20A maximum current assumption, then the alternator can deliver up to 250 Watts charging a 12V battery.
Star Cut-in is at 150 RPM and rated speed is about 550 RPM.
Delta Cut-in is at 280 RPM and rated speed is about 680 RPM.
I haven't computed efficiency yet, but it was immediately obvious that the Delta connection required much less torque to turn than Star, as evidenced by the drill press pooping out at 240 RPM when turning the genny in star, while in Delta I got it up to 400).
(No, belting up the ratios faster doesn't help. When you're at 100% power, increasing RPM just lowers the torque - the belts either slip or slow down).
Oh, yeah, stats:
Coils = 12
Phases = 3
Wire gauge = 18
# turns per coil = 56
Stator thickness = 3/8"
Magnet size = 1" round 1/4" thick
Magnets per rotor = 16
Air gap = 1/2"
Magnet circle = 7.5" diameter
Coil size = 1.75" OD x 0.75" ID
Encapsulation: waterproof Epoxy compound, with fiberglass laminations
Warning: do not mix the epoxy aggressively - I accidentally introduced too many air bubbles into my mix. If I had known that there was enough unmixed epoxy left over to start again, I would have.
In the real world, I will need to space out the rotors because there is no way an actual windmill can tolerate 1/16" spacing between rotors and stator as it yaws this way and that.
Thanks again, everyone for the inspiration, feedback, and for sharing your own successes & failures.