Assembling the alternator was a bit of an adventure and the anticipation of seeing some voltage output was killing me!
Ok now lets see what a few magnets and some coils of wire can do....
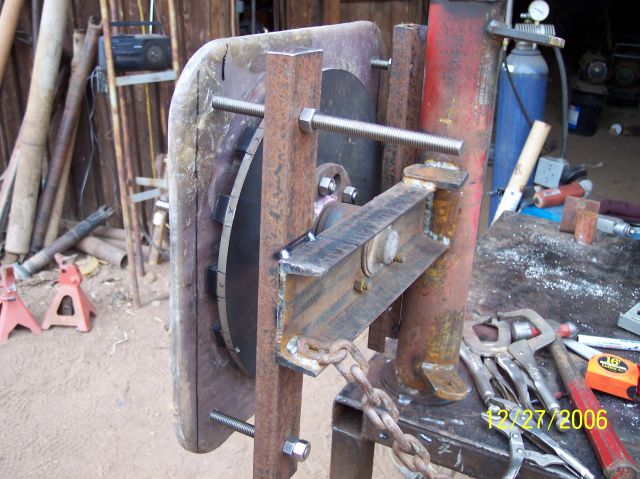
First I needed to build a stator mount. The mount in Hugh's plans seemed a little complicated. I wanted something a little easier and needed to stick to the philosophy of the master plan - K.I.S.S. (Keep It Simple Stupid)
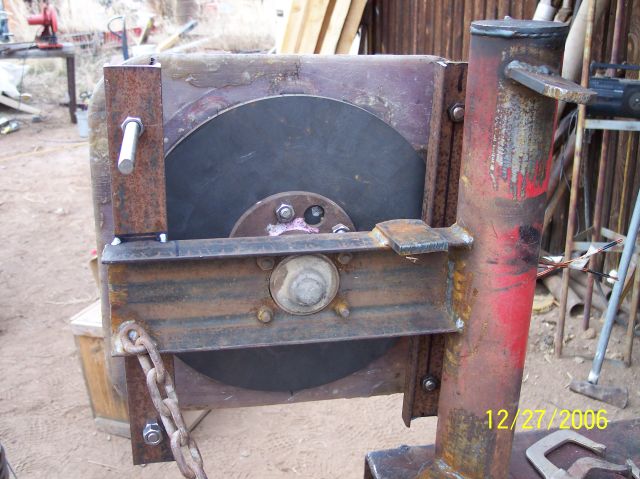
The stator mount is just tacked into place at this point. I didn't want to weld'er solid until I was certain it was in the right place.
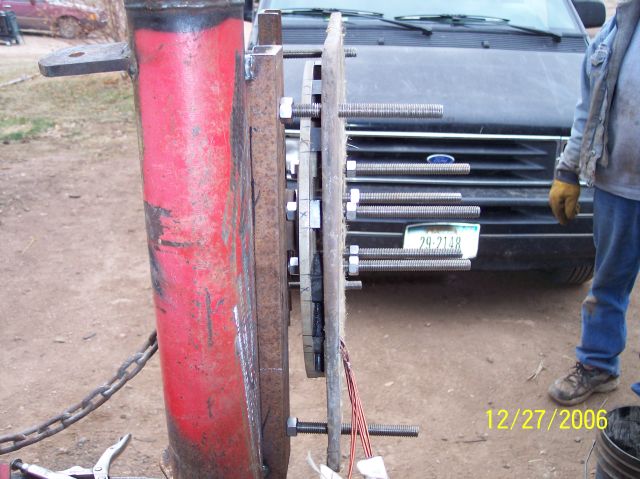
Here is a side shot of the mount. You can also see a portion of my father who has been indispensable throughout the whole process. After all he is the one who taught me the basics of welding, mechanic'in and running a lathe.
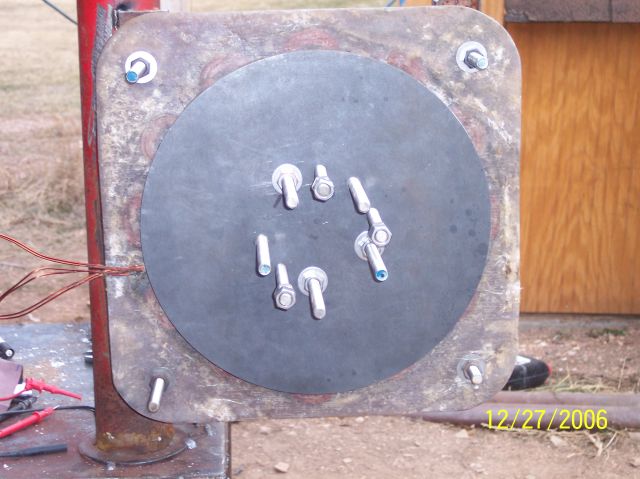
Ok - Couldn't wait any longer I had fasten the stator down and install the front magnet plate. (What will it do for voltage - keeps ringing thru my mind!)
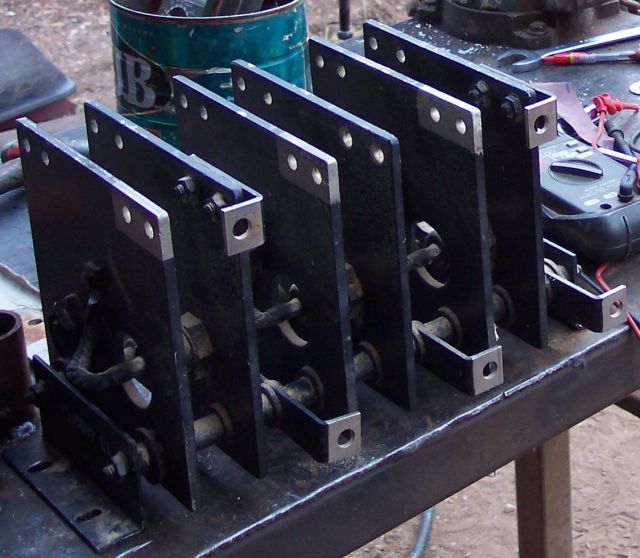
This is the stud diode rectifire that I scrounged from an old piece of mining equipment. I'm not sure what the ratings are on these diodes but I'm sure it's more than I will need.
I decided to install the rectifier after I seen that the alternator was showing some voltage from leg to leg. At this point the amount of voltage was not important, but rather the fact that it is producing a voltage.
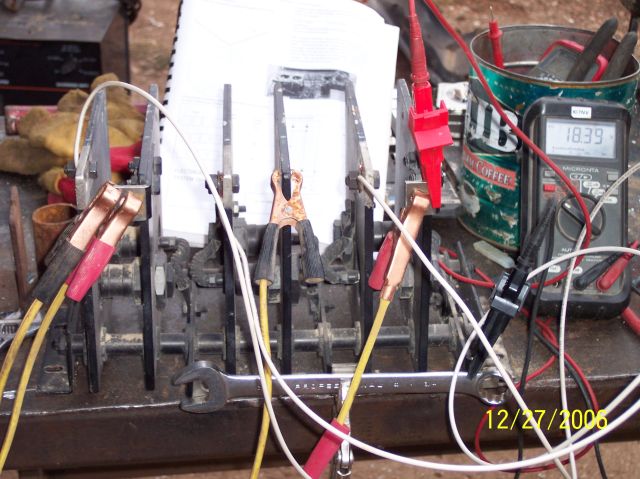
Ok - I know this is messey...but you have to realize the need that I was experiencing to see this thing work.
All we had were some jumpers and....Well a 3/4" wrench to make some connections. 
HA - 18 VDC! She works...
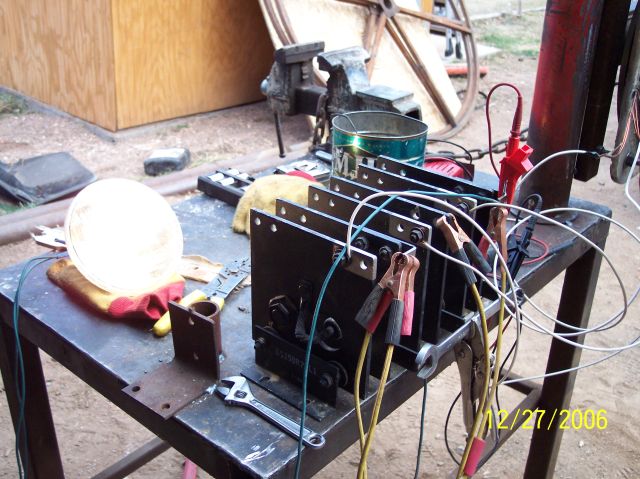
Ok, ok... yeah but it's not doing anything right. What can we use for a load. Well we scrounged an old head lamp and pig tail from an old Chevy Nova and made'er light-up.
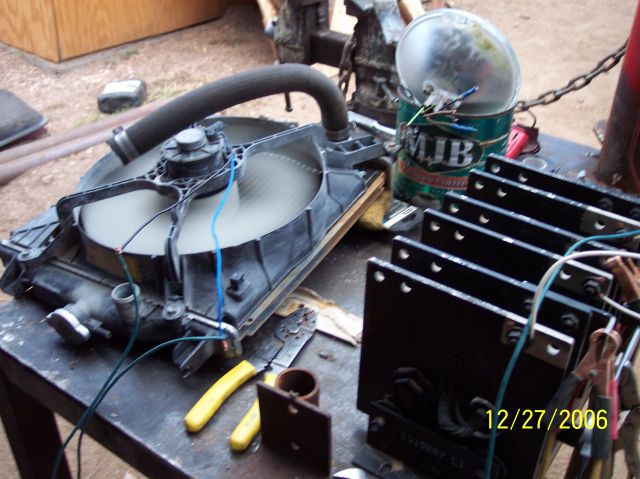
The next "load" we found was a coolant fan scavanged from a Subaru. We knew that sooner or later these old car parts were going to come-in handy!
I'm not sure how the fan motor is constructed but it didn't take much to make her spin. In fact a quarter of a turn on the alternator would make the fan start to spin! That was neet..
Incidentally, the head lamp that is now setting in the old coffee can has an element that is burnt-out. We thought it would be fun to see if we could fry it...we did.
It's amazing how, when loaded, you can feel the torque on the alternator. Also, when you short all three of the legs together before the rectifier, the torque is tremendous.
After the new excitement died down, I took another look at the air gap between the magnets and seen that it was not very uniform. At one extreme there was about an 1/8" between the stator and magnet plate and on the other end there was about 1/4" gap.
Well, that was it for day one of the alternator's assembly. The next day was going to be a time for making sure the air gap between the magnets was more uniform, make better connections on the rectifier and to take some meaningful voltage and speed (rpm) measuements.
Wil