Some time ago I was asked about carving blades/airfoils by hand and how one could get the proper 'twist' from '2 by' material. It is difficult to describe things with words at times so I suggested I post in a diary and all might benefit.
A simple CAD drawing shows one can get over 40 degrees twist if one just properly positions the twist in the blank. The 'face' won't be a place to register the airfoil. One can imagine the complaining at this time. Get over it. Make wedges to create the proper attack angle or make the blade adapter with an angle.
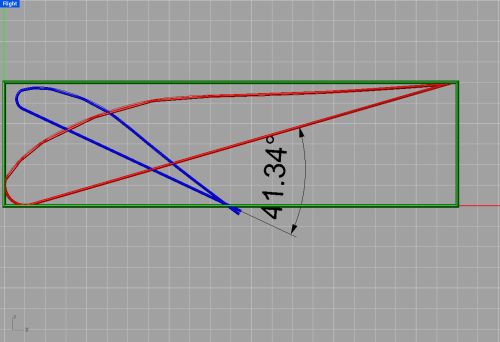
The strongest and most stable woods are 'Vertical Grain'. Ideally the airfoil should be 'VG' at all points for strength and stability. With '40 degrees of twist' it would be difficult, if not impossible, to get a chunk of wood to conform to vertical grain at all points on the airfoil. It is doubtful a piece of wood with 40 degrees twist in a few feet would be stable. The best blanks will be clear vertical grain material. It is hard to find. The first question asked is usually 'Can I laminate up a blank.' . The proper answer is, 'I have no idea'. Many can. Many have no idea of selection of the wood to make a carving blank or that the annular rings should alternate with each added piece. Get good clear wood, avoid the 'heart', orient the grain properly, make good tight joints, use the proper adhesives, cure them at the proper temperatures and it should be fine.
Wood species: Use what is available. Preferably one can find a light, rot resistant wood that is basically clear or small tight knots. One can dream of Sitka Spruce, 50 growth rings per inch and no knots on a 40 foot long, 24" square timber. Well, dream on, it is no longer common. Many species were once 'certified for aircraft spars'. 'Atlantic white Cedar', Douglas Fir, Eastern white pine and many other species were used and certified for aircraft work. Early Gibson and Martin guitars were built with 'Spruce' from local lumberyards. Basswood, walnut, butternut, cherry, ash, yellow pine and even oak would make a decent prop although oak will be a bit heavy and others are more valuable as a furniture wood than as a turbine blade.
Ron