This diary entry is in response to a request by Nando
here:
Over two years ago now I put together a ram pump made from common plumbing parts. This pump has been in continuous operation since, lifting just under 2000l of water a day up to a delivery height of 53m. The water comes from a spring 2.8m higher than the pump approximately 50m away. In its original configuration I used a modified standard brass inline spring check valve for the 'clack' valve. The modification required simply removing the spring and using it in a reverse direction from normal.
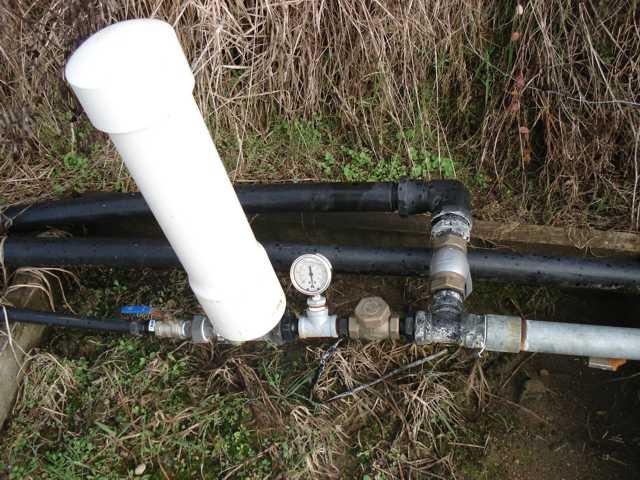
Over two years later (being some 60+ million violent closing events!), upon inspection, I found that there was considerable wear in the moving parts (brass against brass). Part of the problem was the installed angle of the valve. The valve, using gravity to resist the mechanism closing until such time as the water flow over came it, was inclined from vertical as a means of regulating the pulse length/water flow rate. This also meant that the stem attached to the disc put more pressure on its guide on one side.
In my search for a more durable replacement I was refered to a local valve manufacturing company. This company manufactures large industrial valves, but also had a selection of many smaller valves from many different suppliers. After being left to myself in a back room, I rummaged through many different valves before comming across a particular vertical lift check valve.
Vertical lift check valves basically have a disc that is allowed to travel vertically and seals on a seat at the bottom of its travel. Water pressure/flow from the underside of the disc works against gravity and lifts the disc and is allowed to pass. Water flow in the opposite direction works with gravity to press the disc against its seat to seal off the valve.
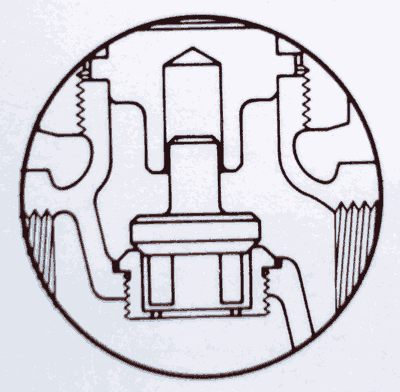
In order to use this type of valve as a clack valve, the valve has to be installed upside down so that the valve 'falls' open. The passage of water in the reverse direction works against gravity and lifts the disc up against the seat, sealing off the flow and creating the necessary water hammer effect.
All of the previous vertical lift valves I had looked at were unsuitable due to the disc sitting mostly flush back in the housing when in the fully open position. Being out of the water flow in this position means that the passage of water is unable to pick it up and close of the valve for the desired water hammer. This particular brass bodied valve is designed for steam use and features all stainless(410) working parts. It is configured in such a way that the disc remains exposed to the water flow when the valve is fully open. 410 is considerably more hard wearing than brass so I considered it a good candidate.
1 1/2" valve
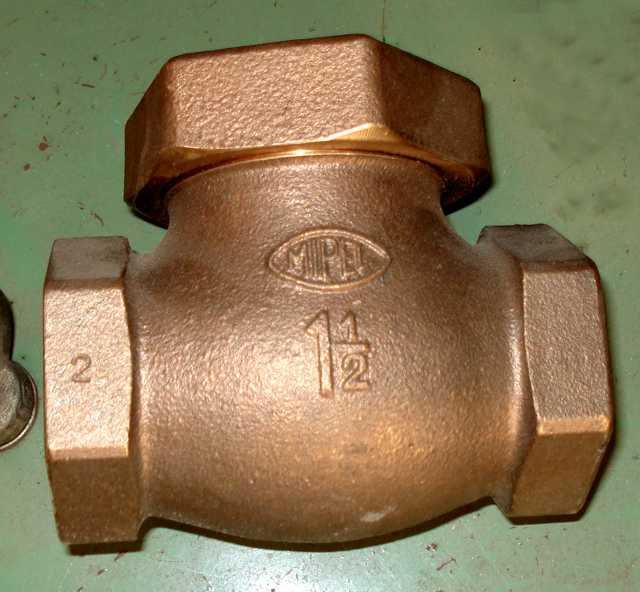
Looking in the inlet (when used as a clack valve). The contrast inside the valve has been altered but is still pretty bad:
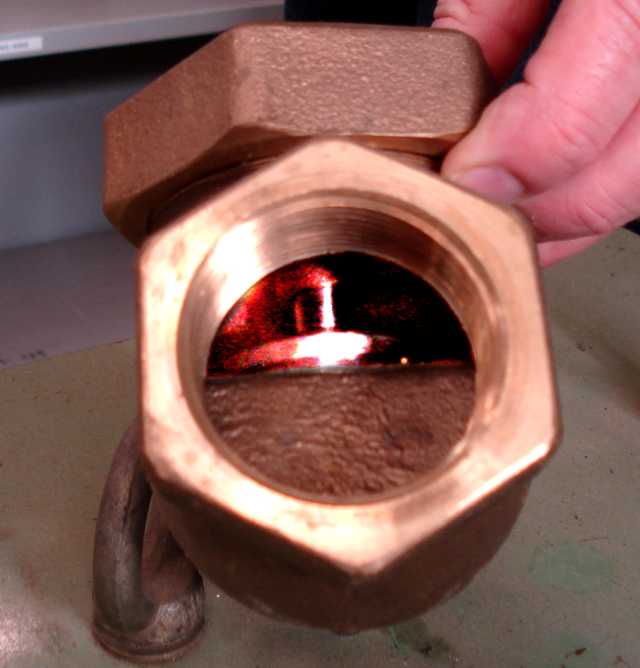
Looking in the outlet:
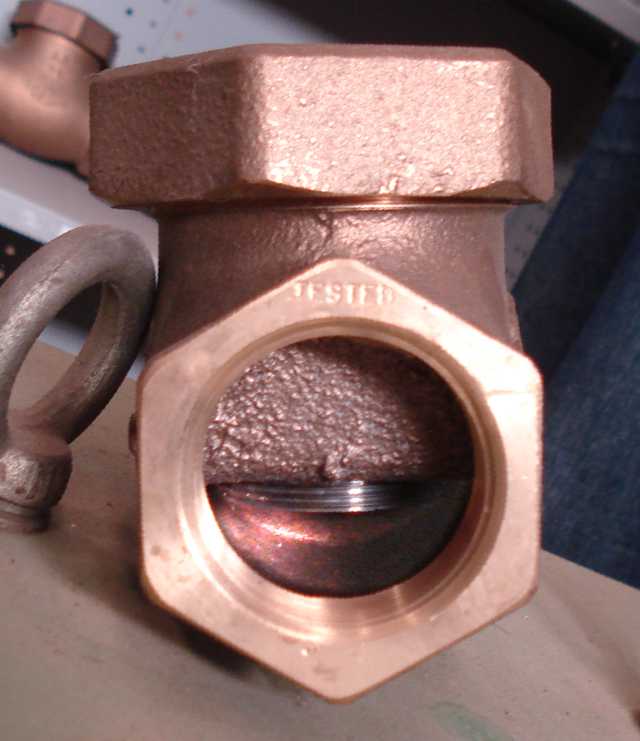
Another bonus was the valves horizontal orientation. I collect the waste water ejected from the valve and this tends to inhibit its operation to a degree when using a vertical valve. A horizontal valve basically throws the waste water out to the side.
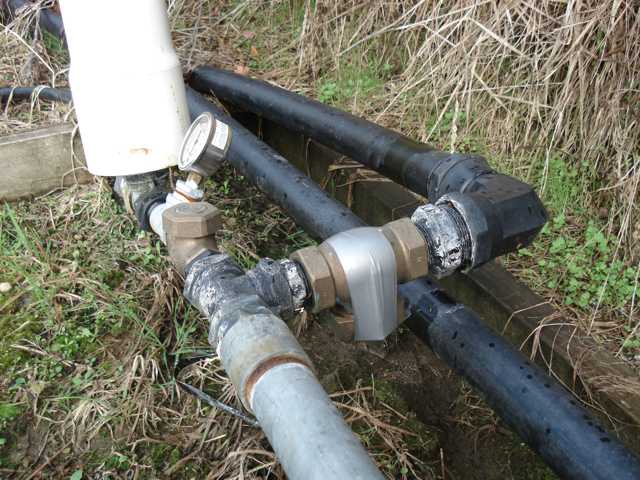
The valve was installed without any trouble. The only problem I encountered was when I went to start the pump. With the old valve it was simply a matter of holding it shut until the water pressure built up in the drive pipe then depressing it fully and letting it go. This has to be repeated a number of times until there is enough back pressure in the delivery pipe to produce a negative pressure 'reflection' to open the valve again. The new valve has a vertical operation in a horizontal body and has very limited access to the mechanism for manual control. Closing the valve was no problem and just required holding my hand over the outlet, letting the pressure increase then letting it go. The passage of water through the valve closed it. Opening the valve once there was pressure behind it was the hard part. After trying to pry the valve open with various implements I was eventually came upon the answer. A short sharp rap with a wooden mallet did the trick.
I tried many different ways of regulating the pulse/flow with the old brass valve to try and optimise the efficiency and never came up with anything reliable. I attached all manner of weights and springs to the mechanism but they always came off or broke. While the new valve was floating around my vehicle before I installed it, I noticed that there was a mild attraction to magnets (also floating around my vehicle
The 410 stainless that the moving part is made from is magnetic. After a bit of playing around I established that I could use a magnet applied externally to the housing of the valve (bronze is not magnetic) and effect the internal mechanism. By placing the magnet at the side of the housing such that gravity is assisted in holding the mechanism open, I can vary the pulse length. Holding the valve open longer lets flow rate reach a higher level/greater momentum before the valve closes. This means more water flows and also that the pressure spike is greater. Varying the distance of the magnet from the housing allows a degree of adjustment to this rate. The magnet is currently held to the valve using duct tape as can be seen in the image above.
The new valve is a PN25 made by Mipel in Brazil and is available in all common sizes from 1/2" up tp 2". I pay $US63, $US83, $US140 for the 1", 1 1/4" and 1 1/2" respectively. A cheaper version of the valve is also available with a bronze seat and ptfe disc but this one is not suitable for the reasons mentioned above (also is not magnetic). The valve has a LG2 bronze body, cap and union nut and grade 410SS disc and seat. Specs are here
A short low quality video (~95kB) of the ram in operation is here. The valve has been in operation for about 4 months now with no sign of wear.