Members occasionally complain that they hear lots about people's successes, too little about people's failures. Well, I'll confess to my goof-up. Y'all get to say "I told ya so".
I discovered this weekend that cable doesn't fit!
Here's the diagram that I SHOULD HAVE drawn BEFORE going with this plan:
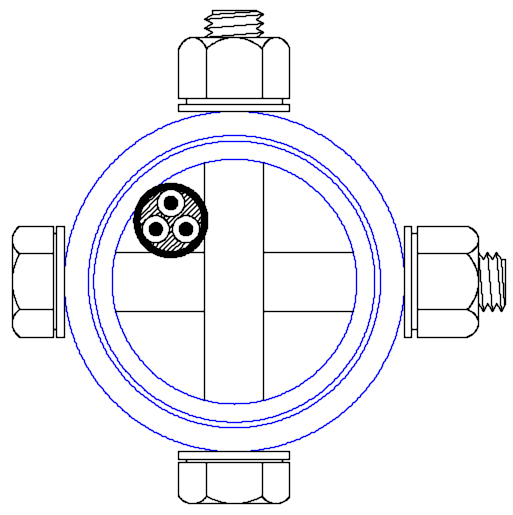
As you can see, the cable won't slide between the criss-crossing bolts. The biggest cable that will go is a #10 gauge, 3-conductor cable. And that's only when I split off the outer jacket, and fed the three wires through. They just barely fit. I doubt #8 wires would have passed through.
I originally wanted to avoid welding structural joints as much as possible - my welding sucks. Since I have a drill press, I was able to drill the holes in the pipe to bolt them together, so it seemed like the simplest way. Right. Now where's the space for the power cable?
I used a stiff "fish-wire" to catch the conductors at the other end and pull them through, just like eletricians do to put wires into existing walls or conduits. But this technique has its limitations, too, and you can't really control where the fish-wire goes as you push it up a blind tube 40 feet long. If absolutely necessary, individual conductors up to #2 Gauge could be fed down, each in its own corner. Pushing the fish-wire down the tube three times and not getting it jammed is pretty unlikely, so that approach is probably fraught with trouble, too.
Well, the wire is in, such as it is. It's going to be very windy for the next couple of days (according to the weather report), so all I can do is wait. I may not be able to raise this thing until next weekend. The prop is assembled in the garage, just kinda hanging from the ceiling, and the generator is sitting on the top of the tower, just kinda waiting idly.
My face is turning blue....
Steven