Hi Guys
I am just starting to a new wind turbine project but with a slight change to the normal. This machine will be radial flux with an iron core stator and the magnet drum on the outside, very similar to the A.W.P. turbine but with neos. I have most of the components gathered together and ready to roll.
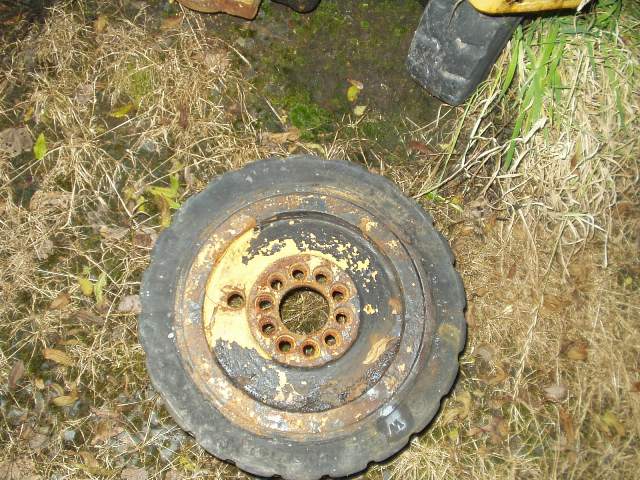
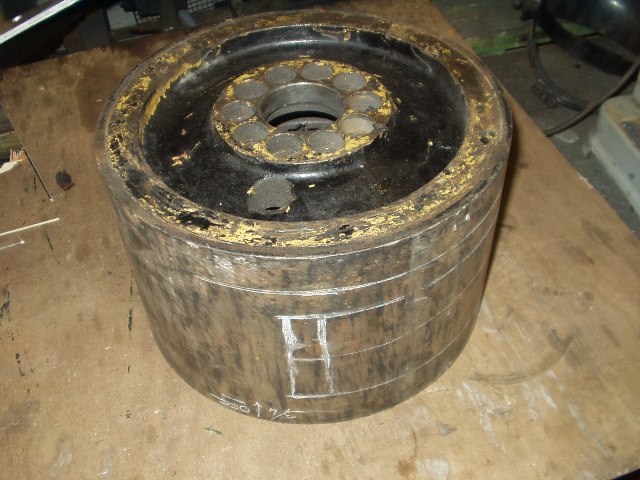
This shows the tyre removed, I used a mortiser with a 1" chisel to cut off the tyre.
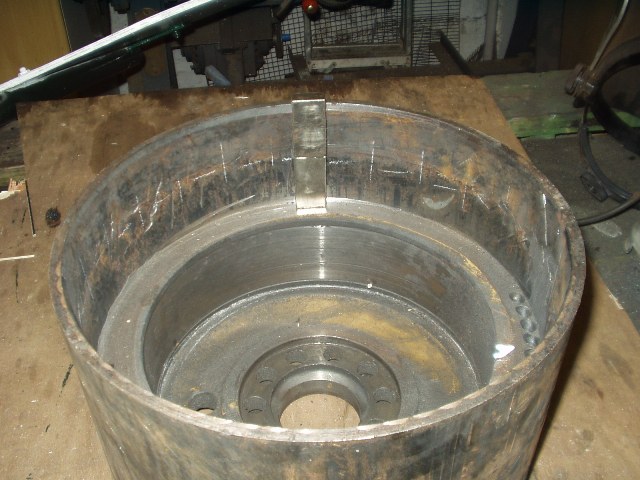
The magnet drum is the front drive wheel from a forklift truck and will need a little bit of machining to fit the magnets.
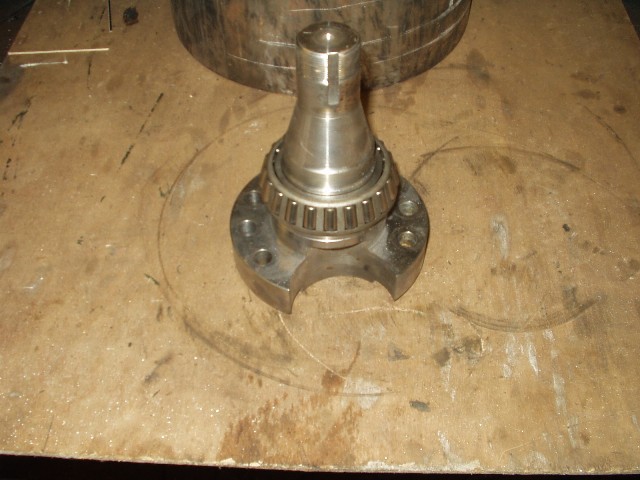
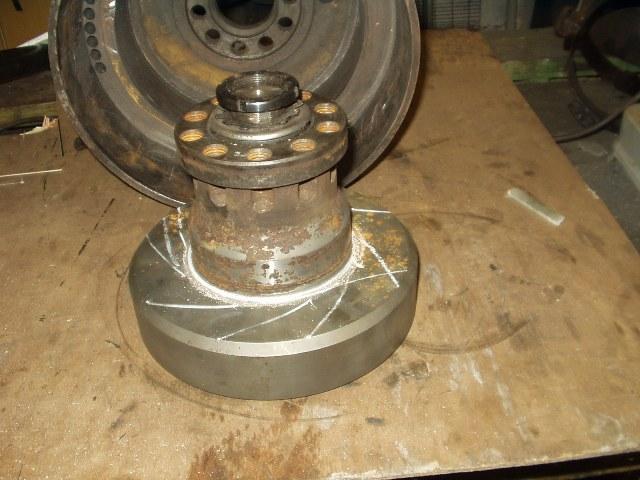
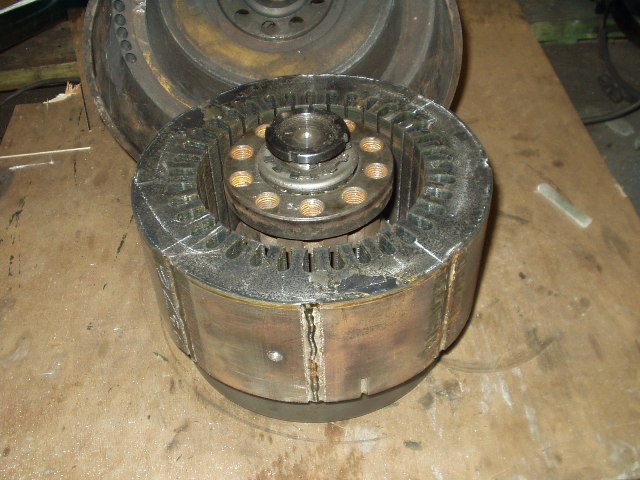
The original bearings and hub will also be used.
The stator lams are from an 11kw motor and I intend to machine new slots on the outside.
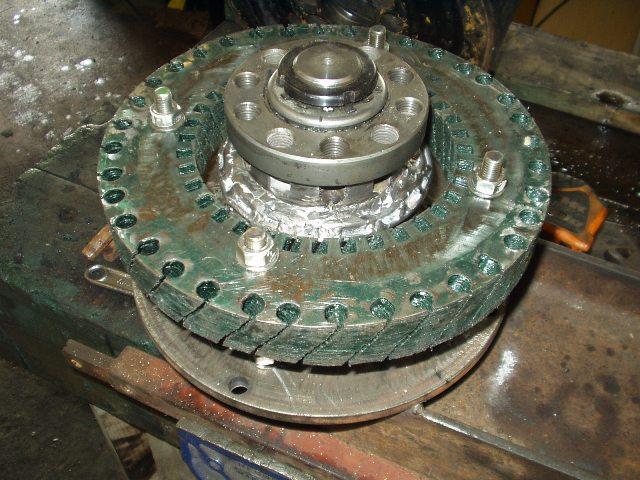
I have had a practise run on another old stator and it seems to work but I have a couple of questions to ask before I start to make the jigs etc.
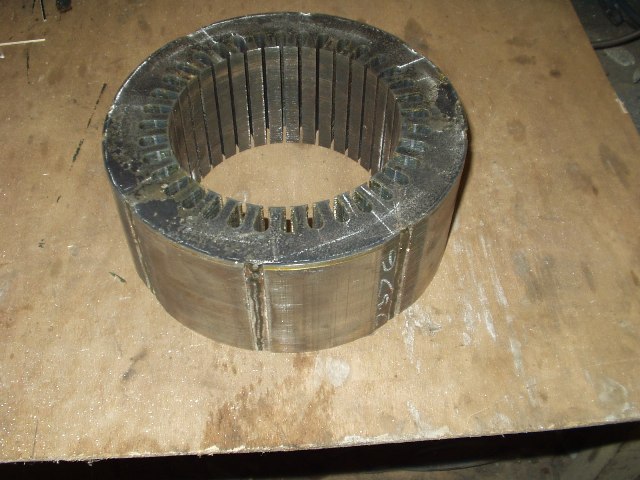
This is the stator I intend to use.
My plan is to drill 36 slots with a vertical drill with a jig to maintain accuracy.
The lams are welded on the outside but after drilling they will be turned down on the lathe, the lams will then be split and de-burred, skewed, varnished and pressed.
The magnet drum will have 24 poles around its circumference each being made up of two 2x1x.5 magnets in repulsion, 48 magnets in total.
So that's the plan so far, I have no idea of blade size or expected output yet, the only part I am sure of is that it is going to be very heavy and will need a purpose built tower. That will please the wife!
So here is where I need some advice please!
Q1. is the shape of the stator slot critical? Most that I have seen are oval
Q2. Is it possible to use a round hole for the slot about 12 - 14mm dia
Q3. If two magnets 2x1x.5 are placed end to end in repulsion N-N or S-S will they act as one pole 4x1x.5?
Many thanks in advance
Russell