Well I have spent a long time in the studing mode and then finally took the plunge. Starting of with a 3/4 HP 220/380 3.4/2.0 1440 Rpm Motor.
The first thing i did is set up the magnets in the stator to get the diameter of the rotor that I would have to make.
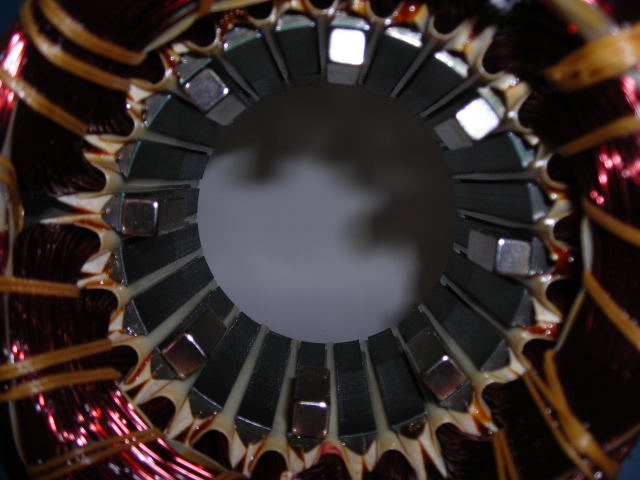
From info posted on this board from the late great Zubbly I then proceded to set up the magnets as they would need to be to cover the 5 of the stator legs (id of the coils) which worked out to be 6 magnets.
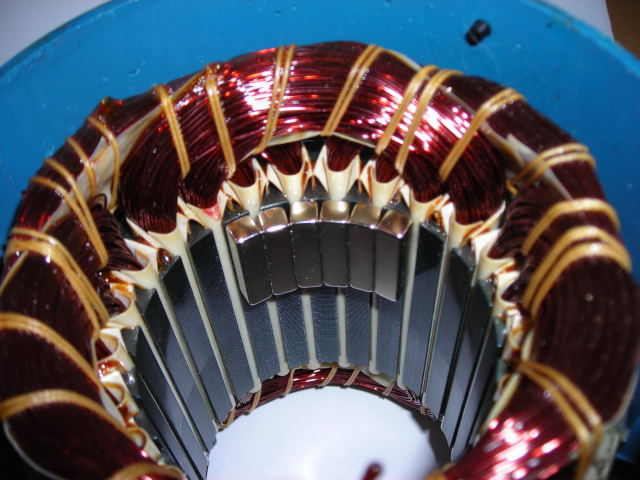
Then the real fun began. Making the rotor and putting the magnets on it.
The rotor is made of grey iron stock machined to allow aluminum end caps to be pressed into it and onto the stock motor shaft. I used loctite 638 for this task.
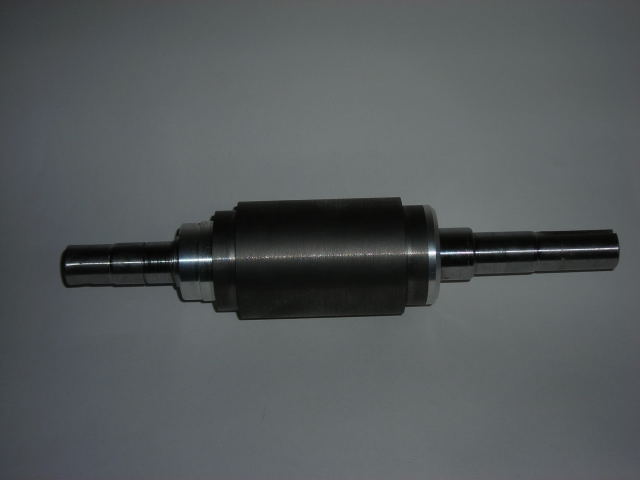
The magnets where placed on the rotor using Loctite 326. This took weeks as I placed each magnet on the rotor and gave curing time between each. In the beginning and end steps I was limited to only placing 1 magnet at a time but inbetween I was able to get 3 set at a time. I made a testing sleave with the proper I.D. to test clearances as I went along. Slowly step by step all 60 magnets found there rightfull place upon the rotor.
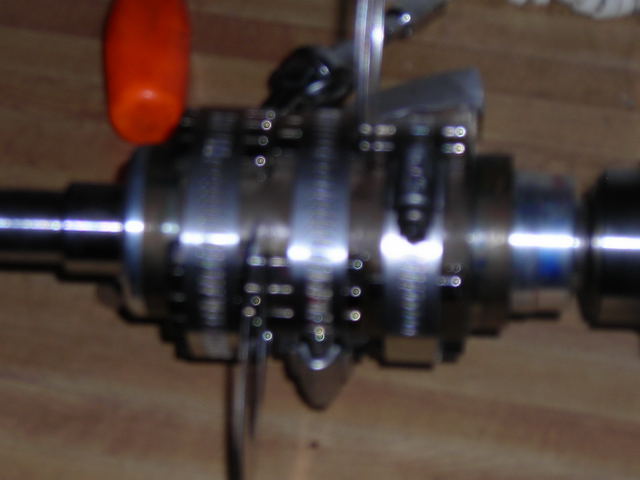
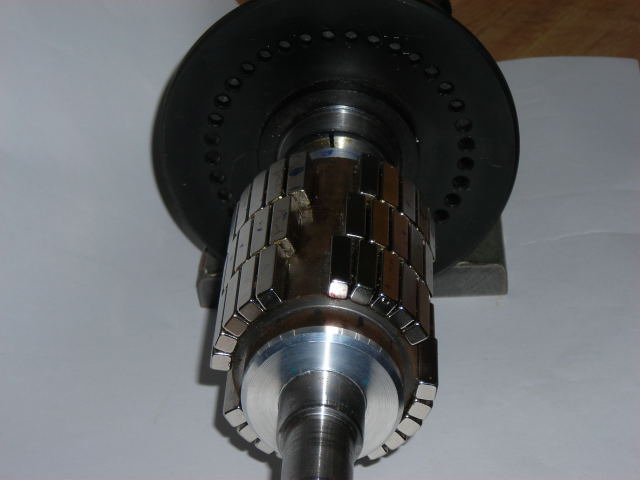
After all magnets where in place I laid up some Kevlar tape on the rotor and cast the unit with slow cure Epoxy resin. After casting I then cut down the O.D. to fit within the stator. In the end the magnet to stator gap is .047 of an inch and Rotor O.D. to stator is .012 of an inch.
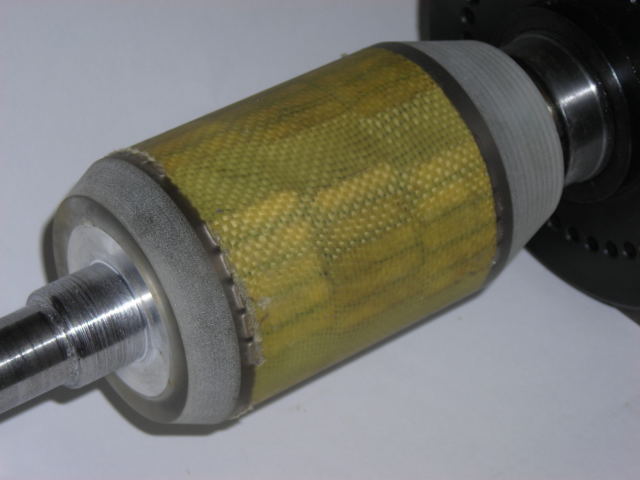
Many thanks to Flux for pointing me in the right direction to test input watts properly. I already has spinning the motor in my little lathe between the chuck and the tailstock. I just added a arm to the base mounting point that has a point setting on a gram scale exactly 1 foot from the shaft center line. By getting the torque foot pound reading and rpm's from a laser tach I was able to calculate input wattage. Ft. Lbs x Rpm's/5252 x 746 = Watts
With the Amp meter and volt meters attached to the batteries I calculated output wattage.
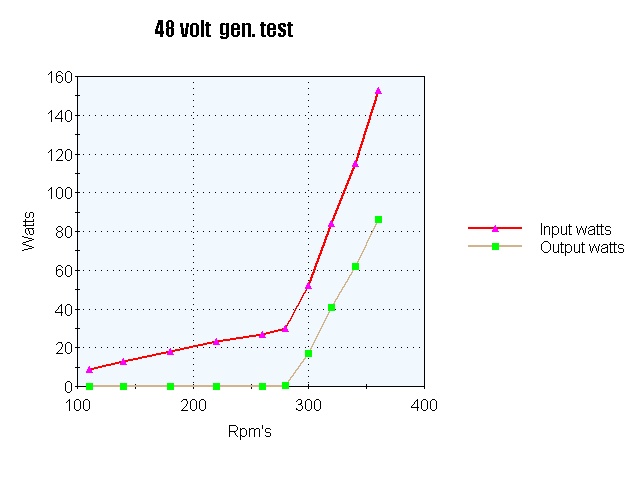
Even thought I don't have the power needed to pull this generator to max output on my lathe. I can now see that the output power of a stock wound motor is the
Claimed motor max amperage x battery clamping voltage x phases = max output wattage.
This goes along with what I have read on this board by others.
This means that my 3/4 conversion should make around 559.5 Watts.
Motor amps Delta 3.4 x 56v x 3 = 571.2
The max. wattage changes with battey charging state as far as i can see.
Watts per Hp 746 x .75 = 559.5
Zubbly rule of 150 watts per cubic inch of magnets.
Using 60 .25 x.25 x 1 inch magnets = 3.75 cu. in. x 150 = 562.5 watts. Means that I should be able to pull this to near max output.
The bad part is that my figures show this to be only 55% efficient which means that the prop will have to push out just over 1000 watts to drive the gen. to max output.
Some may ask about cogging. Yes there is some. It takes 10 ounces of force on the scale to overcome it. I have looked all over this board and have not found out if that is concidered allot or alittle.
I have ordered a set of blades of from ebay 6.8 ft TSR 8. By the Altons blade calculator my gen. should start at Tsr 9+ at 7.8 Mph and drop to 7+ at 24 Mph before needing to furl
Now onto the next steps furling system and tower.