Continuing from my last posting.
http://www.fieldlines.com/story/2009/2/9/15032/62195
The addition of a second rotor as suggested by DanB and Flux has improved performance significantly.
The rotors are 6" square, and using a bicycle hub for the main bearing.
Still only using a single test coil, with more turns of thinner wire, 24 swg (0.56 mm) this time, 340 (Then I ran out of wire..)
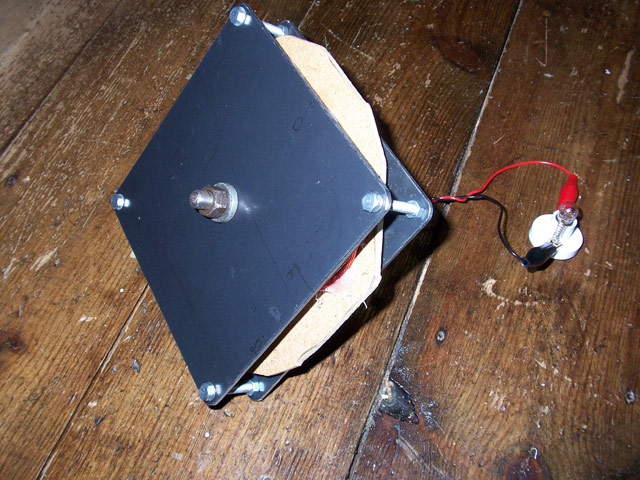
Whilst the MDF wooden stator mount is adding to the air gap considerably, it gave me some idea of what can be achieved, there was still a strong attraction of the rotors.
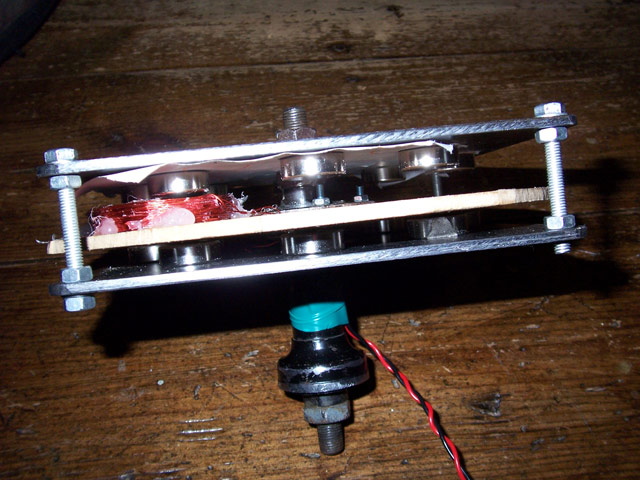
The single 3 ohm coil produced 7 volts @ 700 rpm, and was enough to illuminate a 2 watt bulb with a hand spin.
As this is a 6 coil, 3 phase set up, I may be in VAWT territory?, not really bothered at this stage, as it is fun experimenting.
I have found a good method of winding coils also.
Using the actual chosen magnet as the former sandwiched between 2 steel plates, circular probably best, the coils can be wound, and then (to prevent them expanding when released from a jig) the plates can be carefully slid apart to expose the coil and adhevise can be applied to hold the windings in place, leave to set and repeat on the opposite side - It worked well for me with thin wire.
Ben.