Hi All
Firstly, excuse the intro, i had a Roger Waters song in my head when i wrote that.
So my basic design is a 9 coil, 12 pole design. From what ive gathered, the sane thing to do is to have the hole in the coil the same size as your magnet. The magnets i plan on using are 40 x 40 x 10 mm, so about 1.5 x 1.5 x.0.5 inches N35 Neos. The inside of the coil will be a 40 x 40 square, and the windings will bring it to about 80 x 80 mm once done. Thickness im aiming for is about 10mm, same as magnet thickness.
If the north pole of one magnet moves out of the centre of the coil in a clockwise direction, the south pole of the following magnet should just start moving over the same coil. A north pole moving over 1 side of the coil, and a south pole moving over the other side of the same coil will cause the flow of electricity in the same direction in the coil.
The coils i want to wind with 0.5mm wire, 2 strands in hand.The reason for 2 strands is to get the total length of copper with half the resistance, as the electrons dont have to move the total length of the wire. I have worked out that i will get about 800 turns of wire in the coil, adding up to about 208 m of copper if my calculations are correct.
The whole stator will fit inside a 360mm diameter circle, and the rotors will be about 300 mm OD.
I have a good idea on how i want to mount and balance the setup, which requires a few machined parts. So hopefully it will all go OK.
Here is a pic of my coil and magnet layouts. Blue is north pole and red the south. The coils are copper in colour should it not make any sense.
Please tell me what you guys think. Will i get something decent out of it?
Thanks for your input
Roly SA
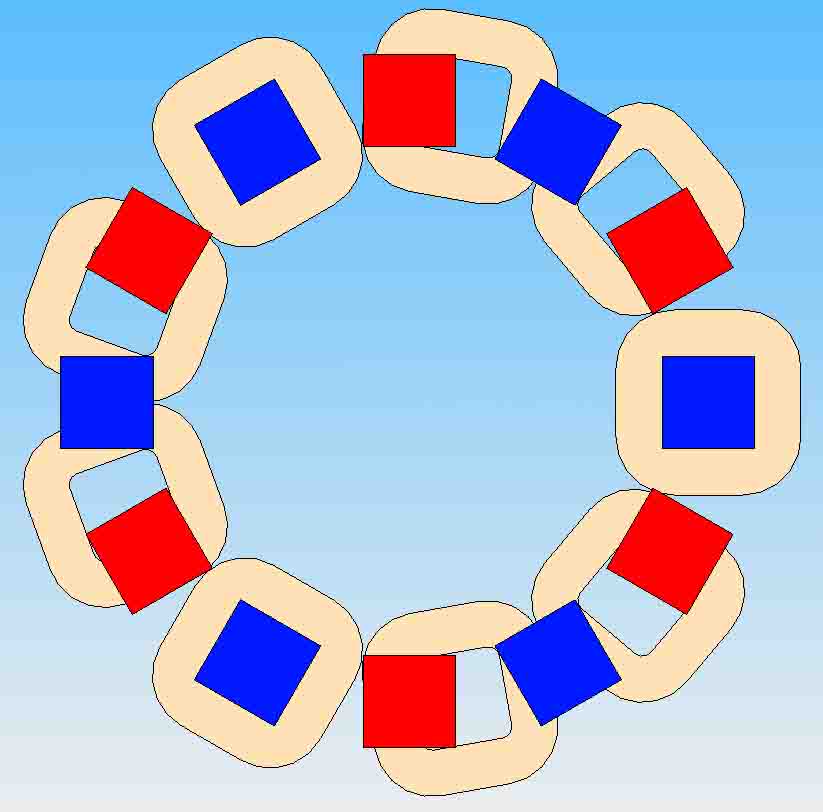