Below is some illustrations of induced losses. The images are computational fluid dynamics models done by Risoe. This is an extension of what I had to say in the last paragraph of Ed's recent blade calculation post.
http://www.fieldlines.com/story/2005/5/30/15179/7889
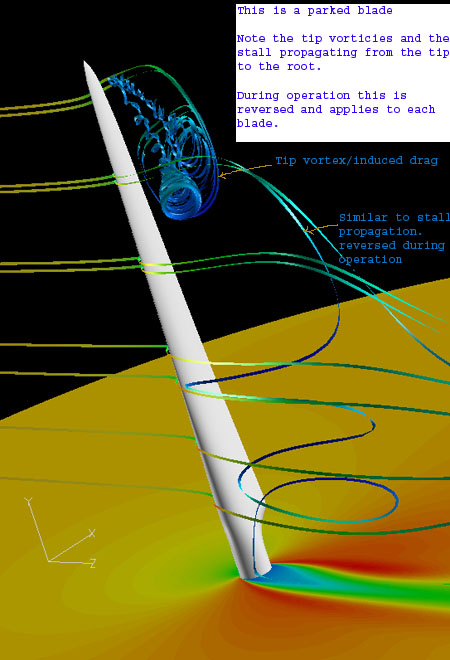
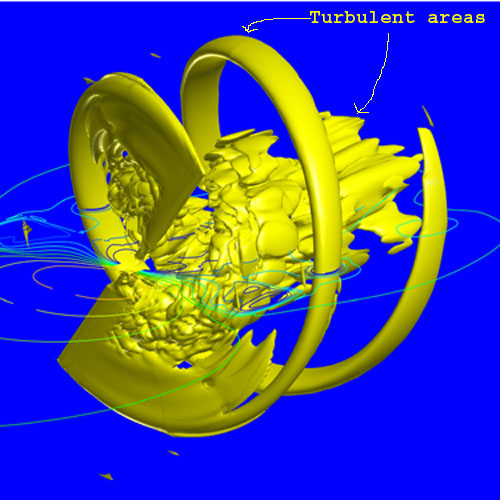
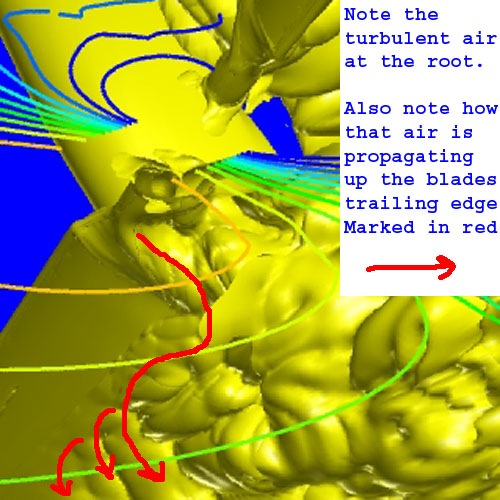
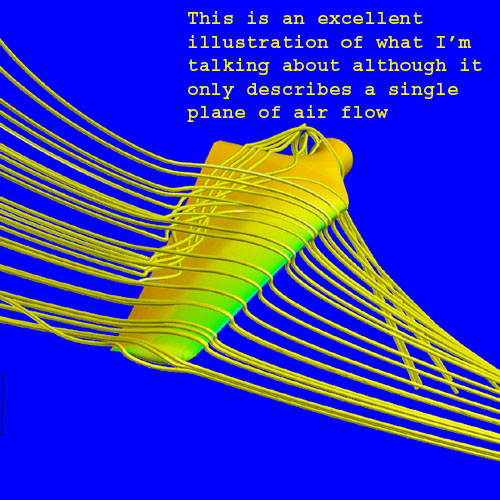
The newest enercon blade design reflects a recognition by them of the fact that treating theses areas will yield appreciable results. Note enercons use of winglets and a deep swept back root at a high angle.
http://www.enercon.de/www/en/rotorblattkonzept.nsf/mainView/1?OpenDocument
I, as usual these days, was advocating the use of fewer blades if possible and thought I would throw out some info to support my logic, which is, everytime you add another blade you add another "set" of these induced loss areas which may be greater than the losses incured by increasing the cord width of fewer blades which results in increased drag across the lifting portions of those blades.
Any takers? This isn't intended to be a classic 3 blades Vs. issue.
Mike