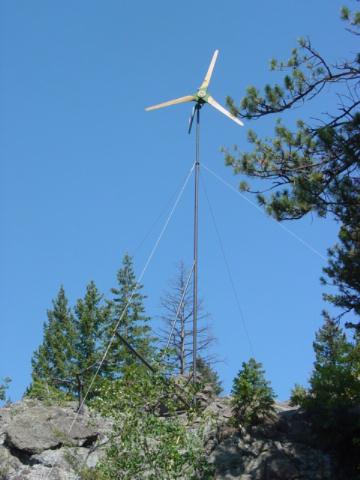
We had a busy weekend helping our freind and neighbor Adam get his 10' diameter, 48 volt wind turbine up. We built this machine last fall, there are details about that HERE and some other discussion about its construction HERE. The tail was to be a white whale... but he wound up painting the flag of wales on there... he was born and raised there, it looks pretty neat.
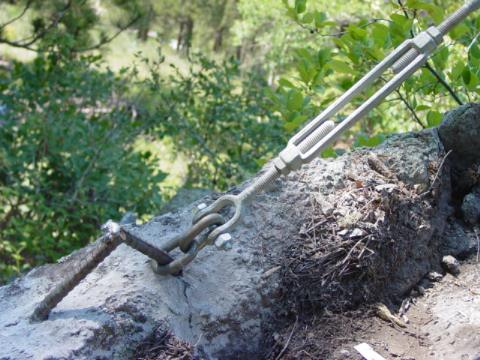
Pictured above is one of the guy wire mounts. It's 2 pieces of 1/2" re-bar epoxied about 6" deep into the rock. This whole tower is on rock - the base is mounted this way, all the guy wire mounts are about the same. It was a tricky site - we had to carry lots of stuff (generator, welder, tools, pipe, wind turbine etc...) about 300' up a steep rocky hill. The line is right at 300' long, the tower is just under 30' tall, up on top of a rock outcropping.
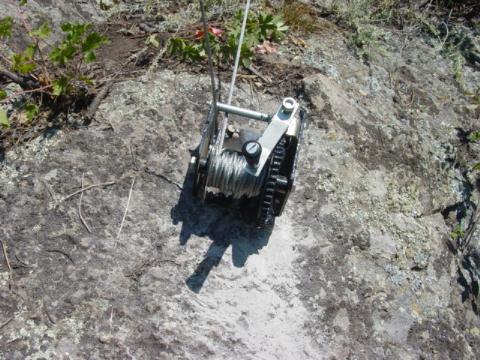
This tower is pulled up with an inexpensive hand cranked winch, which I welded to re-bar which is epoxied into the rock. This little winch cost less than $20, its rated 2000 pounds (although I wouldnt trust that... its a cheap winch!). Its a wormgear winch... no ratchets to mess with. While its very easy to crank - it takes LOTS of cranking to move this tower up and down. It's handy that the shaft for the crank is 1/2" diameter.... we quickly discovered that removing the handle and chucking the shaft in a 1/2" variable speed drill makes things quite fast and easy. This little tower goes up and down very nicely and seems quite safe. The guy wires get just slightly loose on the way down and come up tight when it's raised. It's very user freindly.
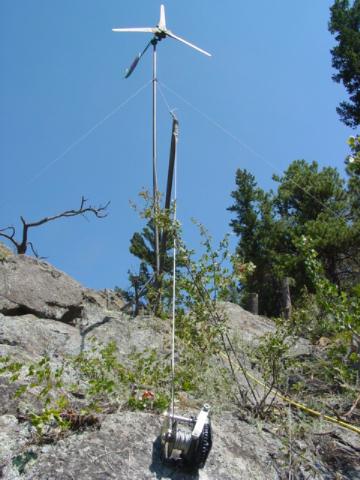
Here is a picture from below showing how the winch is attached to the jin pole. The line through the tower is flexible 10 gage wire, which drops through the pipe and comes out a hole on the bottom. The line from the machine, to the batteries is about 250' long. We bring 3 phase down on 3 strands of 10 gage wire. Again, it's a 48 volt system, so we can get by with 10 gage here.
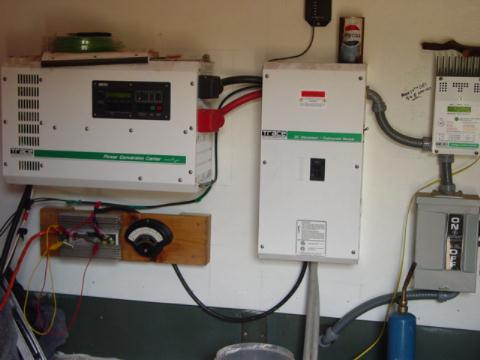
This is the wall in his power room. Hes got a Trace SW inverter. On the lower left you can see the board where we mounted bridge rectifiers and a meter for the windmill. He's got about 400 watts of PV as well. In a week or so, we'll get a dump load and rewire his Trace C40 as a diversion controller so he can use his PV and his wind turbine to help keep his battery room warm when his batteries are full.
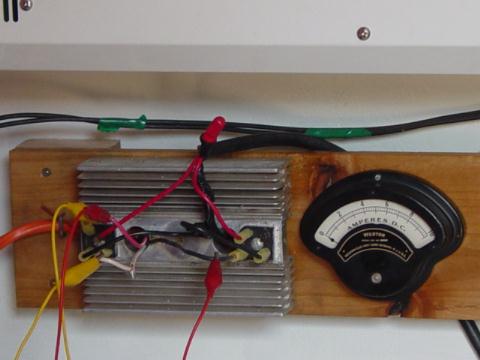
There's a closeup of his rectifiers and his meter. We should have mounted the rectifiers in a vertical positions.. they'd cool better that way, but we decided that heat would probably not be too much of an issue with this machine at 48 volts. I doubt well see much more than 15 amps here. The meter only shows 10, which should be fine most of the time... I suspect there will be days when it'll be pegged. (hope so!) The messy jumper leads are attached there as a temporary shut down switch - so he can short it out easily if he needs to. Soon we'll add a nice switch that does this a little more neatly and easily...
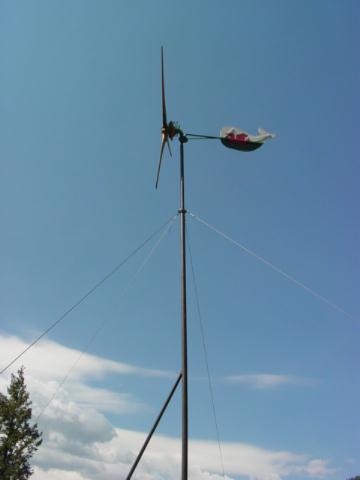
Another fun picture of it. I've not seen any real wind at all on this one yet... it'll be interesting. Odds are the blades will stall... most of the machines like this have had that problem. We'll probalby wind up opening the airgap a touch and adding a bit of resistance to the line to get it right. In the future Im using slightly smaller magnets on 10' machines I think. We did see a bit of wind... about 2 amps on the meter on a very calm day (about 100 watts) - so it is working. It's nice to finally get this one up!