Well, I use the kids digital camera and can't find it today, so the pics I upload are what I could splice together on the scanner

Has anyone else tried the barrel blades like we talked about in other blade posts before? I built a quicky set in about an hour or so last night. So far my best working blade set! And I have less wind now too.
First I'll say this was a quick shot at making these, fast and dirty, nothing fancy, and they are the best working blades I have had so far. They are badly off balance and mounted poorly to the gennie, they still startup pretty easy and are the only ones that have ran in the high 12V range in such low winds, and also hitting over 15V in medium decent wind. My PCV 2 and 4 bladers would be sitting dead in even heavier winds. As a mater of fact My 4 blader I took off (made from 4" green sewer pipe) to mount these last night was sitting dead all night, these tried to start up even as I was mounting them.
Today I will take them down and balance them, or just make a second set first while these are still up since there are working now.
What I did was to first cut 4 blanks, over 6" wide and more than 25" long. I squared up the blanks so they hung over the edge on all for sides and mounted them to 2 boards. The boards are 25" long X 6" X 1/2 each. Actually 5 1/2" wide, you know milled lumber is always small. I held the blanks together and drilled through them for screw holes with the cheapy drill press.
Once I had the 4 blanks screwed down as tight as I could get them to the boards I ran them though a 10" cheapy table saw. That gave me pretty much 4 blanks almost exactly the same, 5 1/2" wide X 25" long with straight and squared ends and sides.
Then I took the Large Bulky Sawzall and cut the shape I wanted through all 4 blanks and the 2 boards at once. Make sure none of the screws are in the way, if they are drill a new holes then move the screw.
I broke my blade for the jigsaw (cutting a woodburner) and could not find the spares or I would have used it and got better cuts.
Below is what the shape of the blades are basically. This is the wood template I will use for the next set once I clean up the rough cuts and do some sanding.
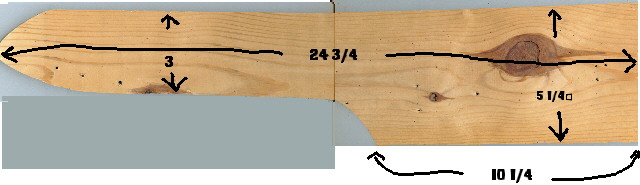
I will most likely try using my router (if it still works) and screw down a little over sized blank to this. I should be able to router out 4 blades at once and everyone be nearly the same.
For mounting these fast last night I already had about a 5"X5" square block I been using as a mount. I took of the blades from that, they did not work well. To this flat wood hub I screwed down the trailing edge of the blade tight with 1 screw. This held the blade cntered as I wanted on the square block. I then swung it out of they way and screwed down the next blad with 1 screw also. I did all 4 blades that way. Then I pushed 2 blades in a row back in place. The leadin edge of one blade lapped over the trailing edge of the next. I drilled a hole through those and ran in a screw loose. I had a small wedge I had cut that was about 23-25 degree angle, I simply slid that under the top leading edge and added some more screws to hold that angle, not tight! The trailing edge IS tight, the leading edge simply pokes out forward. I did that with all 4 blades. This gave me somewhere close to 25 degree angle at the hub.
I have about a 50" rotor now.
To mount this to the gennie, the gennie has a round 3/4" plywood hub hammered onto it. Center hole drilled small then hammered on force fit. It works well for the test rig, but I would not used it for a real mill. Anyway I just took 4 long wood screws and screwed the new rotor onto that round hub centered the best I could in the dark fumbling around.
I knew the blades were out of balance but I didn't have much time for anything last night and I wanted to do SOMETHING anyway just to be doing it, so this was it! I am really surpised this set is working so well! The balance is off enough that swinging the heavy blade half way up the left side and letting go it swings almost half way up the other side, not just a simple drift to the bottom! It swings back and forth too a couple times. It catches the wind good enough to over come the off centered weight and the cogging from the gennie too!
Below is the piice that was cut out of the blade. I think this can be used as is for a mini mill still. It is about 14 3/4" long so with hub added it should still be about 30" rotor itself.
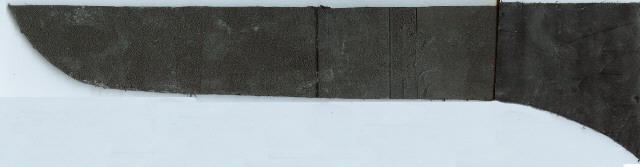
The barrel I used has been sitting in the yard for many years! It shows NO sign of ageing or drying out like PVC sewer pipes will do in just a couple years. The barrel sides are stiff enough to hold up to the wind yet a little flexable, might survive a bird impact? With a little more work I think these barrels would make super great blades for the smaller mills (about 50" rotor maybe more) and should be able to get at least 8 blades from one barrel full sized plus all those shorter peices I showed for mini mills of around 30" rotors. I pay $6 for these plastic barrels (last time I bought some)so I am looking at about $0.40 per blade if you count the 30"rotors, or $0.75 if you just count the 50" rotors.
I am geusing 8 blades here since I cut mine from about half a barrel last night with some left over. I think if laying out the cuts better and wasteing less materail it might be possible to get 10-12 blanks for the blades.
Something I will do but didn't yet is round the leading edge also and bring the trailing edge to a point. Right now they are just however they came out when cut flat
then left to bend back to the curved shape again. And I really need to balance this set!!
As for mounting these much better than I did, I think the fan hubs from many central heat and air units would work well. Most are pretty strong and solid, BUT most I have are counter clockwise rotation so I would have to cut the blades backwards. Also I have an off sized shaft on my test genie and nothing fits it. Japanese motor, and I don't want to pay $20 for a drill bit I might use 3 times!
Better wood hubs could be used also. That's what I will use for the next set or to re-do this set. 23-25degree angle seems good. If I'd have had more time last night I would have made a 3 blader instead, but I didn't have the time to make a new hub mount and stuff, so I just used the 4 blade mount I already had. Making 4 of these blades at once is as fast as making 1 blade once you screw them all down to the wood support.