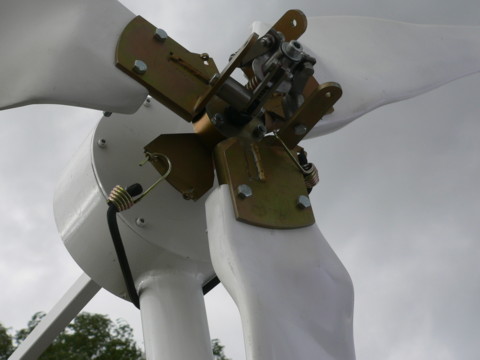
This weekend we went down to Fort Collins to give a 2 day work shop at the 7th annual sustainable living fair. They do this in a nice field with big trees along the Poudre river, right next store to New Beligum Brewing. I never got around to see much of the fair (we were too busy) but one of the neater things I saw were the little 'Kestrel' wind turbines that Matt Tritt brought up to display for DC Power Systems out of California. I believe this was a 7 or 8' diameter machine - very neat, with an axial flux alternator and variable pitch blades. One of the neatest small wind turbines I've seen.
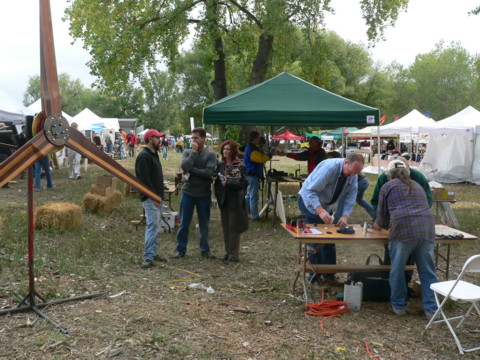
We had the same spot that we did last year, a nice big area under large cotton wood trees. We had a tent and 5 tables. It looked to be a nice day on Saturday till right when the fair was supposed to start (10AM) when it started to get windy and it poured rain. The rain stopped after about half an hour and then we just had to contend with fairly high winds all day. We had between 4 and 6 folks working all weekend on the wind turbine. George and Rich were there to help although we never did any work on it (other than the welding/paint work we did before the fair). At the fair the attendees carved blades, built the alternator, and assembled the machine. They did everything except for the metal work which we can't really do there (plus we don't really have the time).
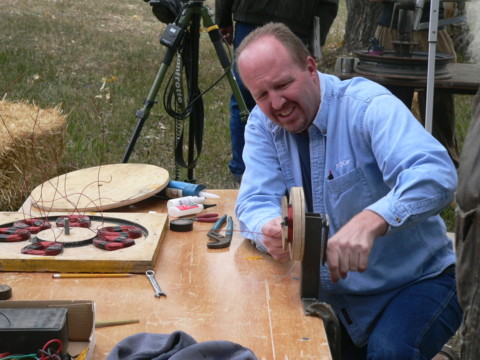
We actually wound coils and wired up stators for two machines. Lately for the 10' machines we've been winding the coils with 140 turns of #16 gage wire.
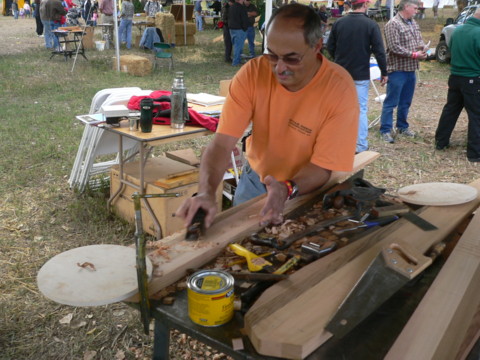
The only power tool we bring is a palm sander to finish the blades. Doing it all with hand tools takes a little longer but it keeps things nice and quiet for the fair. Our neighbors Scott and Bonnie (who own the Canyon Spirit Gallery donated the laminated Western Red Cedar blade blanks that we used. We brought 4 blanks just in case someone made a bad mistake, but we never needed it. To carve the blades we bring a really heavy steel work bench (it's 4' x 4' and the top is solid 1/2" thick steel) and try to keep two people on the task all weekend. That's about what it takes to get done in time.
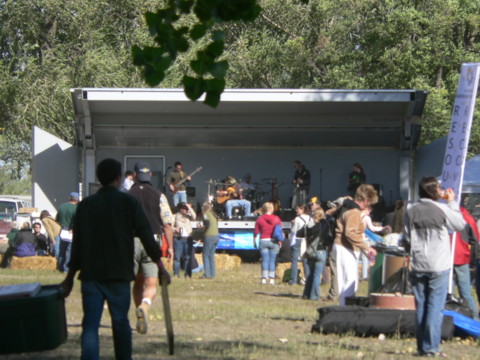
There was good live music all weekend.
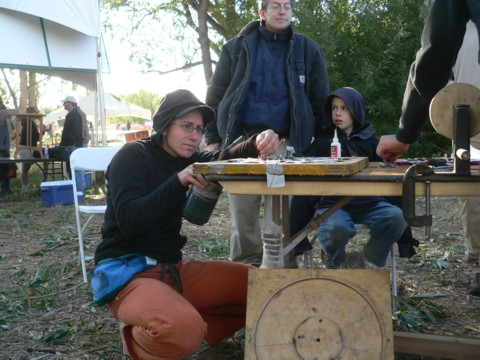
Madeline stripped the insulation off the ends of the coils and wired the stator up near the end of Saturday. The casting process is messy and smells bad so we try to be ready for that at the end of the day on Saturday when things are winding down.
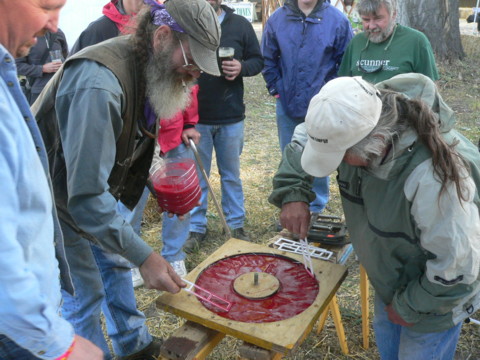
We used vinyl ester this time for all the castings. We did this at about 5:30PM (were supposed to be done at 5:00) on Saturday. It was not a terribly warm day and they were calling for a cold night so I was a bit worried about it setting up in time.
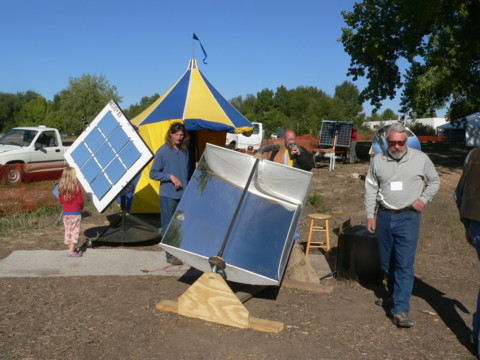
Sunday morning I got there early and had a bit of time to wander around. Justin from heliotrack.com was there showing of some of his neat solar trackers. Very impressive how quickly he was heating water with mirrors - fun stuff. He lives nearby in a neighboring canyon - It would be fun to work on some projects with him one of these Mondays perhaps.
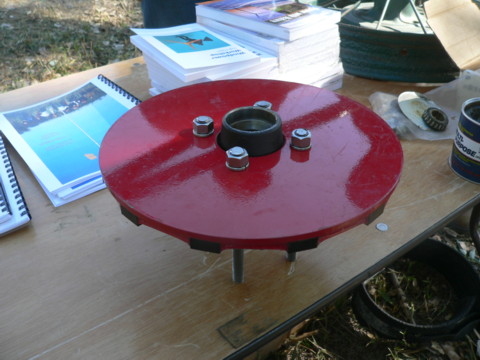
They got all the studs cut to assemble the alternator and fit the hub to the back rotor.
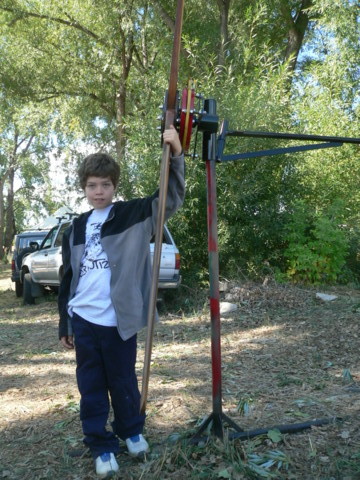
Liam was our youngest attendee. He spent most of Sunday helping to carve blades - drill out the blade hubs etc. He had lots of intelligent questions - he was one of few who came by who actually had a pretty good idea how, and why this stuff actually works. I think he's planning a smaller version as a school project here soon.
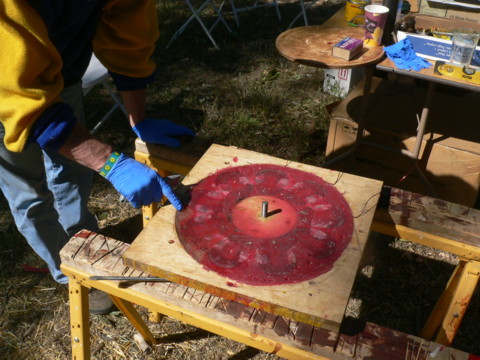
The resin setup nicely, but the stator had a huge air bubble in it right where we needed to drill it out for a mounting stud. One of the folks ran quickly to a hardware store to pick up some 5 min epoxy so we could patch this spot. They drilled a few small holes into the stator to give more surface area for the epoxy to grip onto. It seemed like a good fast fix - it came out fine.
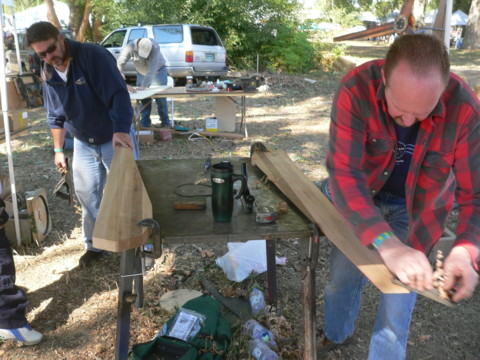
Nearing lunch time on Sunday the blades were just about finished.
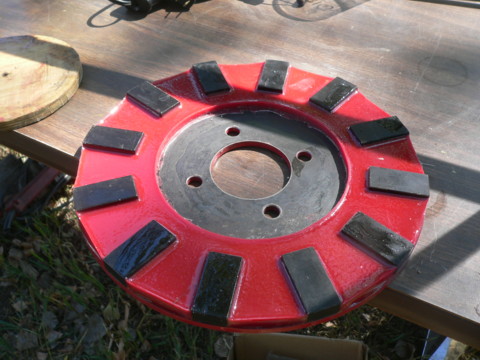
There's our front magnet rotor. Woops... no threaded holes for jacking bolts! I meant to have this done at home before the fair - it makes a real mess of the magnets when you have to drill/tap after the fact. So - another trip to the hardware store for a 1/2-13 tap. They drilled/tapped those holes, it took about an hour to clean up the magnets again and we were back on track.
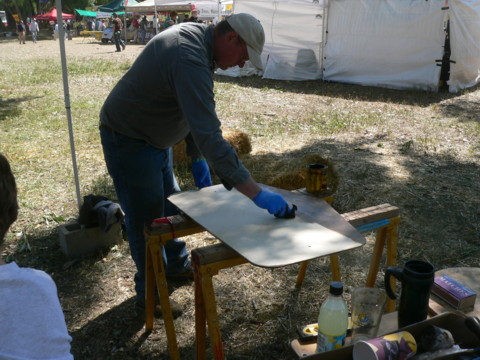
About 3:00PM on sunday they got the tail cutout and stained.
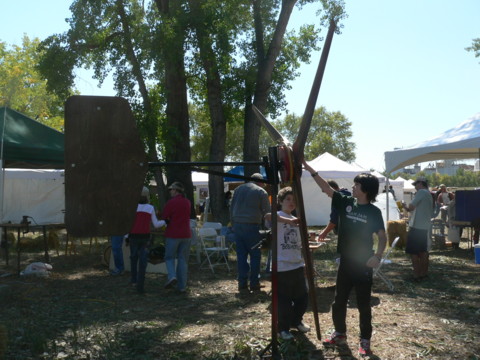
Liam explains to another young fellow whats going on here.
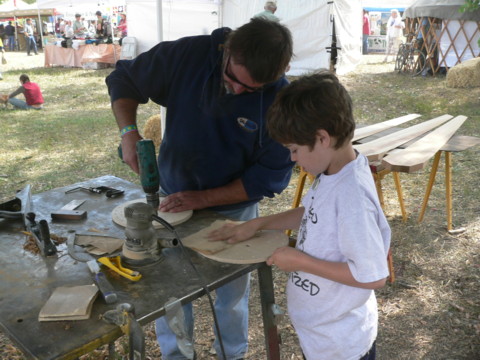
Liam and his father finish up the blade hubs.
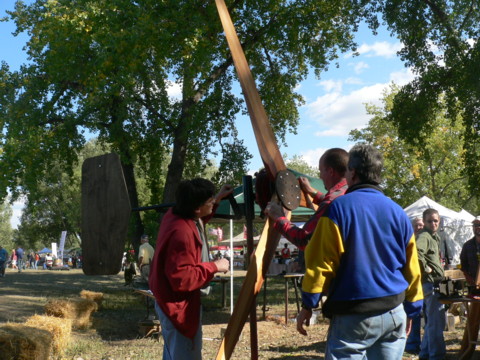
Fitting the blades to the machine right at 4:00PM on Sunday. The workshop closes at 5:00 - and we always donate the 'finished product' (finished or not at 5:00PM) to the silent auction which also closes at 5:00. So it's nice to have a finished (or nearly finished) machine.
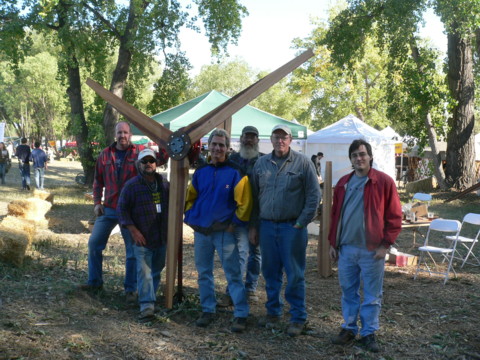
There's everyone that managed to stay till the end! It came out nice - better than expected actually. One of the attendees won the machine at silent auction for $650 - a good deal, a good home for the machine, and the money goes to a good cause. 'Whiskers' (the fellow who got the machine) was also with us last year for the final day and came back this year to find out what he missed. He's off grid somewhere in Southern CO with a 48V system - he understands fully how to build one now, how to fix/adjust this one as needed so I expect he'll get good use from it.
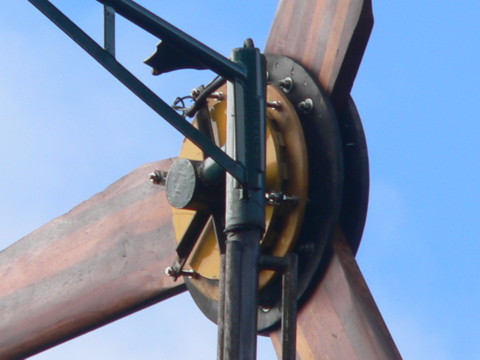
Hmmm... this is what I came home to. It's a zoom picture when its still on the tower - the machine still turned but very slowly as though it was shorted. You can see at least one of the coils looks rather dark, another burnout I'm afraid. I knew it would be windy so I shut down my 20' wind turbine before I left. But it was very windy on Saturday, Sat night, and sunday. A few trees were down - branches littered the strees in Ft Collins. One of our neighbors woke up to find an 18" diameter tree blown down over his truck (that's the only actual recorded windspeed data I've got). I know my 17' wind turbine survived till at least 6:00 PM on saturday (because DanF saw it running) but some time after that the stator burned out again. So... I'm not quite sure where I'll go with this one now. I'll either build a new stator (like the old one) but use vinyl ester and maybe some of that aluminum trihydrate that another fellow here on the board has used, it's said to improve thermal conductivity. Also - the tail boom on this machine is from sched 80 pipe, so I could lighten it a good bit. My other alternative is to cut down the blades and open the airgap a bit but I hate the thought of that.
Other than though, it was a good weekend and a fine monday. We spent monday unloading the truck (we bring what seems like the whole shop down to the fair), dropping my wind turbine celebrating multiple things and arguing about intellectual property rights and youtube.com lawsuits if I recall. It was a bit too much fun I'm afraid.