Hello all,
In 2006 I posted asking if this was a suitable motor: 600v, 3 phase, 1 hp and 8 poles. Zubbly responded that this was an excellent candidate. He recommended cutting down the rotor to accept 1" x 1/4" neo discs, picking the star connection apart and bringing the leads out of the case and reporting back to him for testing procedures. Deep sympatahy to his family:(
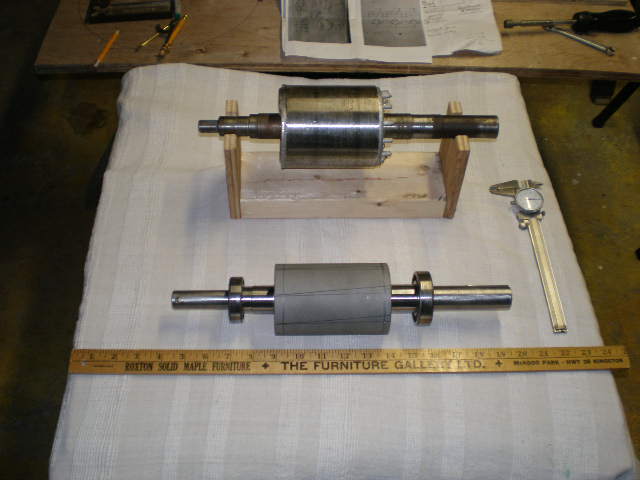
Here is the original rotor and the new one my son machined for me with the face sandblasted for adhesion of glue and magnets.
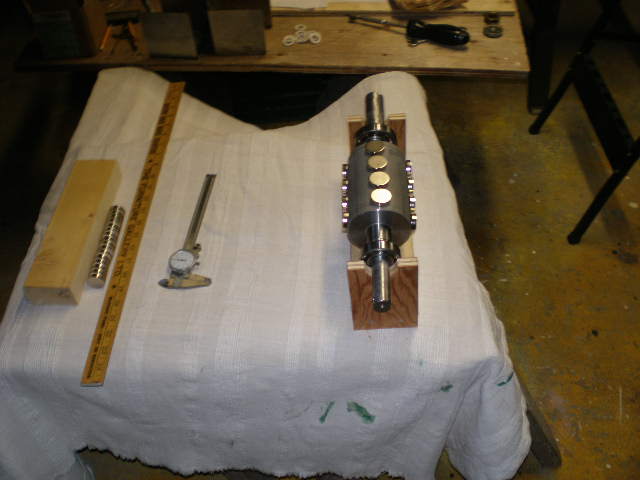
Here are all my north poles glued in. This isn't easy because although they stick just fine dry, as soon as you apply glue they will repel each other. Skate about.
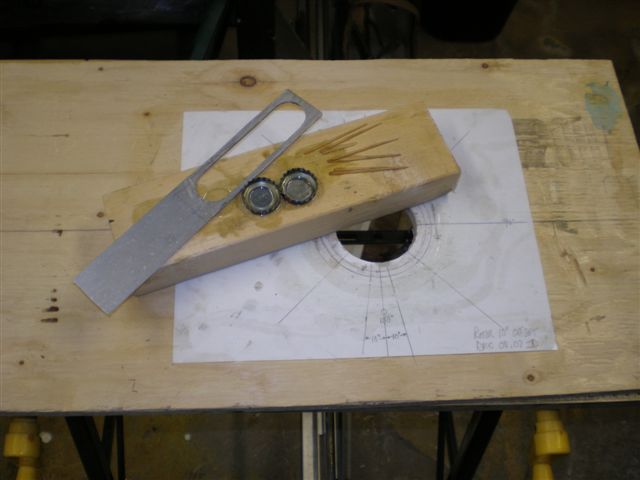
This is a little tool I made up to corral/control this movement. Also note these small mixing containers you might have lying around are great for small batches of glue.
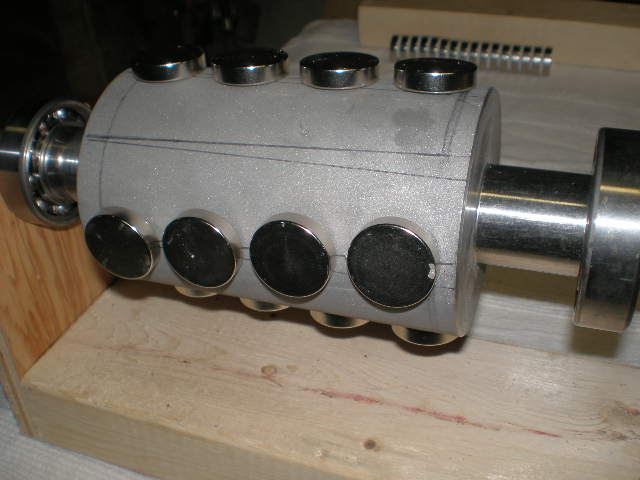
One row per night was all I could manage.
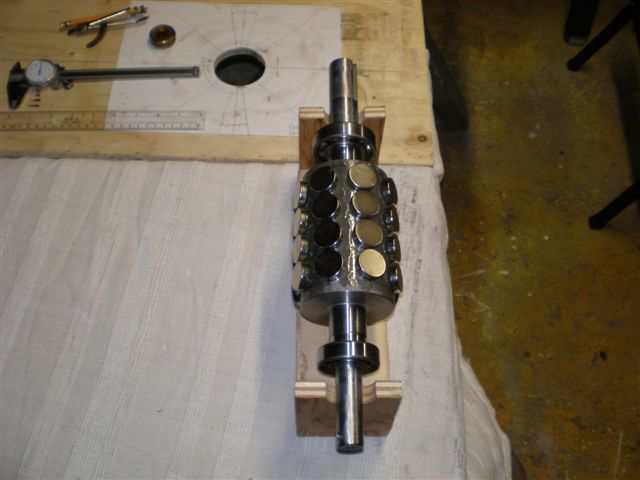
I thought the south rows would now be a nightmare but I guess flux from the Norths made it easy. Although the allignment tool was still required all four poles were completed in one night. I've refered to glue above, actually this was vinyl ester resin.
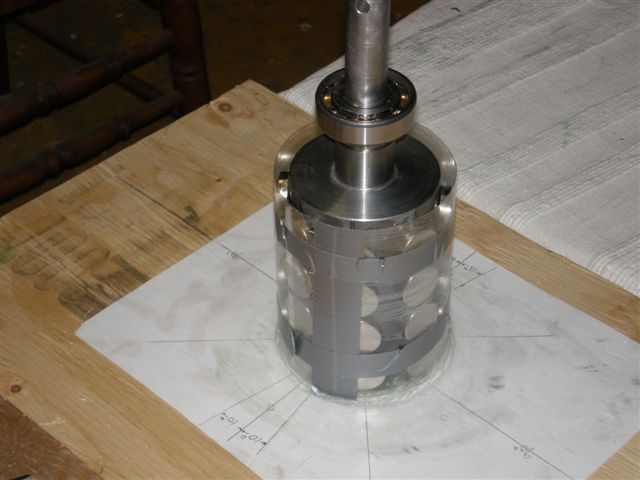
With a split soda bottle to control circumference, some duct tape, a little car wax and silicone, the form was ready.
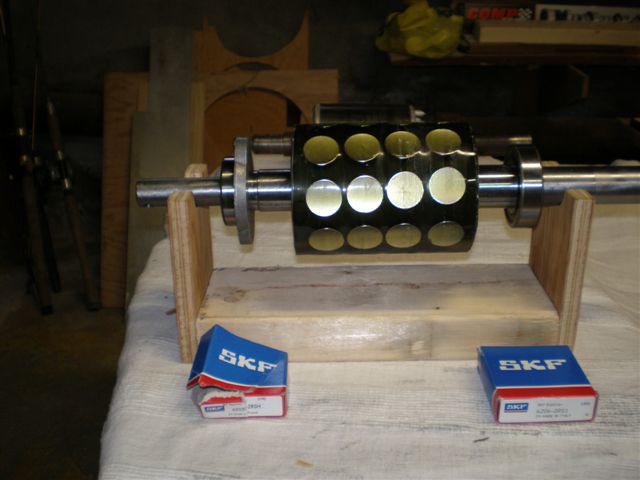
And there it is with new SKF's ready to roll.

You guys scared me so badly I wouldn't try this insertion without my chainfall and some sandbags below. Thanks, it went smoothly despite great attractions.
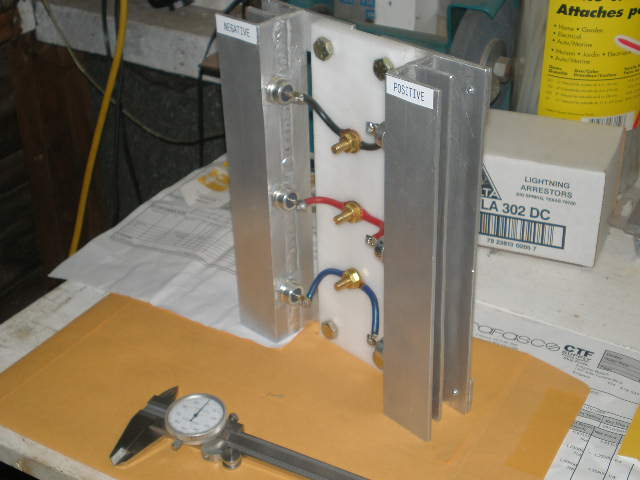
Thanks to this site and especially to Harry & Nando(where are you guys?) I put together this rectifier. Studs are 90 amp each, from India.
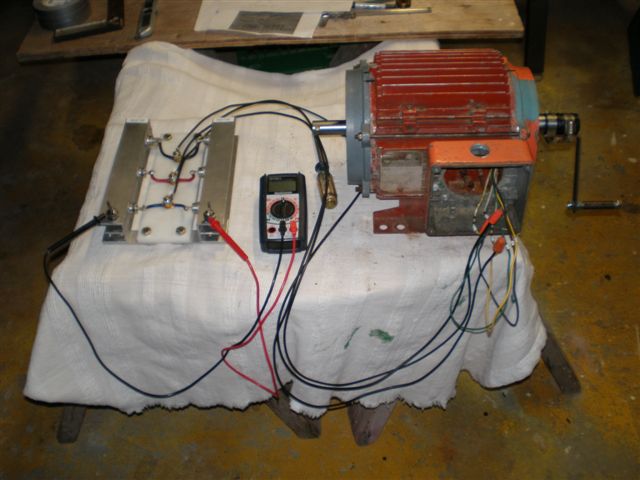
Now I get into some troubles, the mechanical I can work out however I have very little testing knowledge. Hand cranking in delta at 150 rpm open I see 70vdc. When hooked to a baby 48v bank I see 60vdc (4 sla's at rest 50vdc). The first revs are cog free but when I hit 50vdc I feel a smooth increase in cranking resistance. Even I can figure this is cut in! At this point these batteries are really being charged and I'm showing approx. 0.8amps on the multimeter. Is this possible? Please any comments are appreciated here.
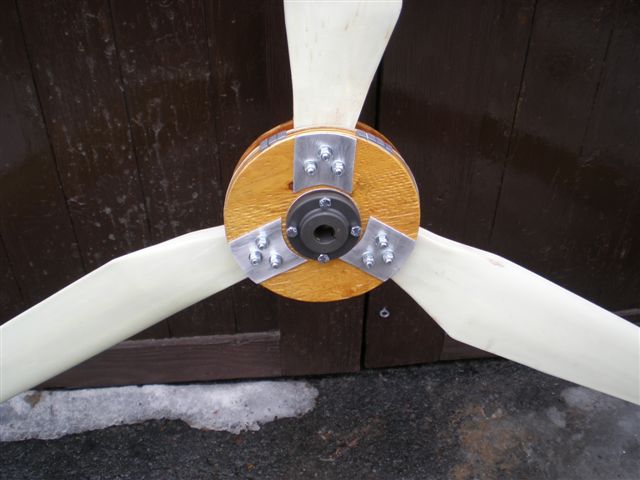
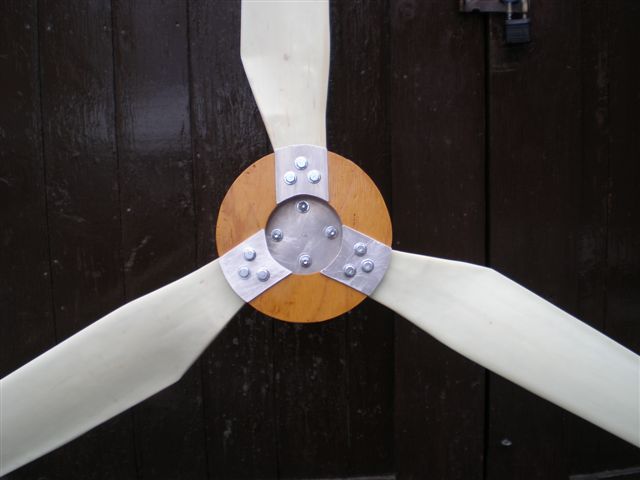
I carved blades for my Hugh 8 foot wich wor great although only a 6 week run before winter storms. Just for laughs I thought I'd try these chinese fiberglass blades we've all seen on e-bay for this job. This is how I secured them. At 8'8" diameter I'm pretty shure they'll get stalled, but we'll see.
I'm running a 12v system now but I guess I'll be changing to 48v. Shouldn't be too bad I just need to change my inverter and pour a new 48v stater for the Hugh, please comment.
What.......Me worry???
Regards, Jim
i fixed that one photo that did not display properly next time name your photos so they have no spaces in the file names before uploading them.
Kurt