Furling with a twist
Hi all and seasons greetings ... its been a while since I posted , just been to darn busy with to many projects all at various stages of incompleteness . The most complete is a 12 footer from Hughes latest plans but built with parts I had to hand.
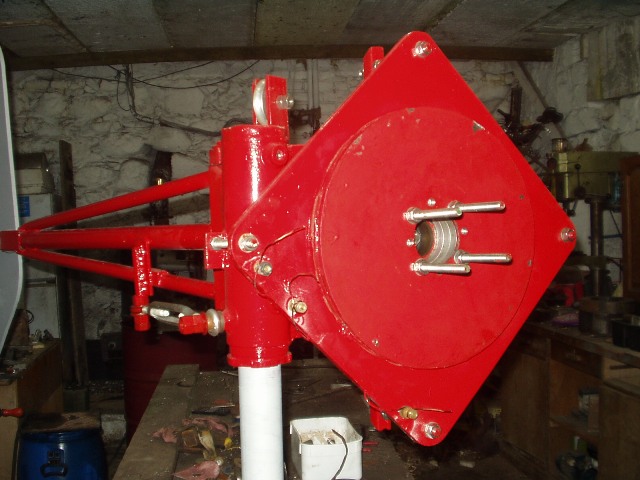
The main spec of this machine is the same as Hughes plans i.e. magnets, rotors and coil turns (48v)
However the chassis, yaw tube and tail are completely different. The yaw tube was originally a hydraulic tilt cylinder from a forklift with the ram removed and the gland nut machined to allow a 3 inch steel pipe to slip inside. The original piston was retained and acts as the bearing for the yaw. The mounting for the stub axle is a single ½ inch plate welded to the yaw tube at a 4 deg angle to give extra blade clearance and the offset for the stub axle (Renault) is 8 ½ inches. All pretty simple and not very deferent to the original plans.
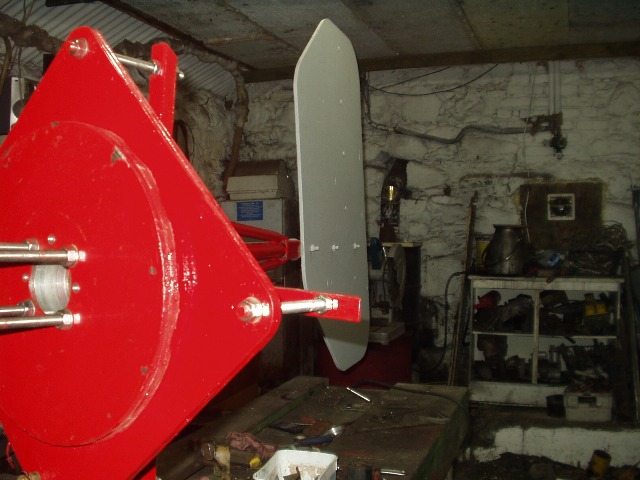
I started to make the tail, again as per the plans and I had cut the steel ready to weld when I saw a few stories about tail / blade strikes and burn outs so I got to thinking! wouldn't it be handy to be able to adjust the furl point from the ground and while the wind is blowing. Wouldn't it also be useful to be able to furl as an aid to shutting down or as a fail safe.
My first thoughts was to connect a cable to the end of the standard tail, bring it over a pulley and down the centre of the tower to a winch or weights. I should say at this point my towers are all lattice work so I have easy access to the centre area within the tower for cables etc. This method would mean the cable would have to carry the full weight of the tail as it would have to lift it up behind the blades.
I then got to thinking why lift the whole tail why not just twist the tail vane through 90 deg to horizontal thus allowing the alternator offset to turn the machine out of the wind, I could set it up so that weight was needed to hold the tail vane vertical and I could control the furl point by adding or subtracting weight from the cable on the ground and while the wind is blowing. So I made many drawings and eventually a small model to test the principle. I made the model from a few scraps of card board and a c.d. to represent the blades, the tail was made from a drinking straw with a card vane, the wind was simply the workshop airline. All very crude I know but it proved to be a useful test as proof of concept. I tried various tail configurations starting with the standard inclined hinge type, with the tail in its normal position the prop tracked the wind as normal and with it up behind the blades it furled out of the wind. So with the same model I twisted the tail vane through 90 deg and it furled as before, now I know this is not very scientific but I think it at least proved the concept.
Now it was time to go full size. I started by making a hinge system that would carry the weight of the tail and vane but I wanted to be able to adjust the angle of the tail to the wind so as to be able to correct the tracking of the wind direction without having to change the vane size. I used a ½ inch turnbuckle I had laying about. The tail itself is a steel pipe within a box section setup that allows the tail to twist via a lever at the yaw end, I also added two end stops one for vertical and the other for horizontal. The tail vane is ½ inch ply with less area than the standard plans require as the angle is adjustable I think the reduced size will be fine although time will tell
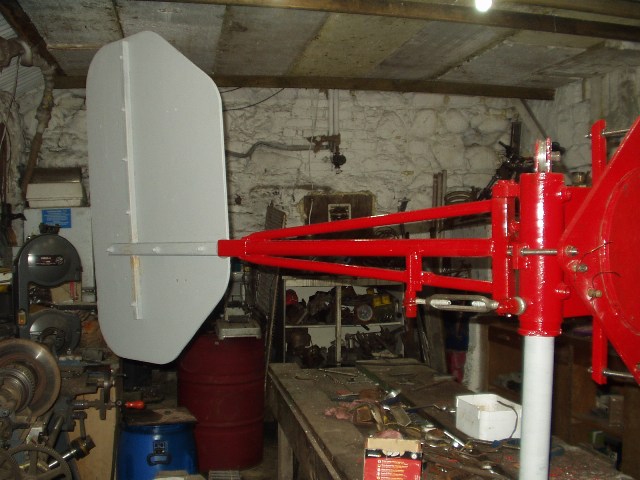
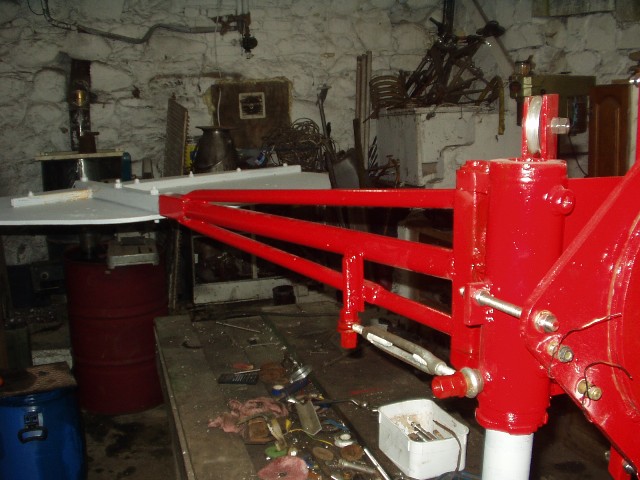
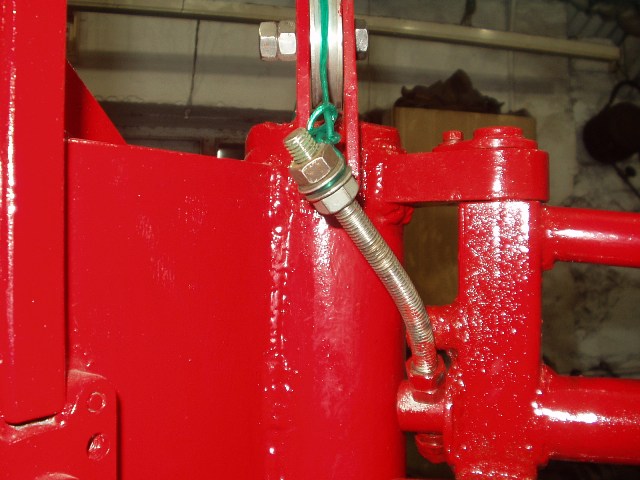
Just need to carve the blades and get it up in the air. The cable for the furling weights is on order it is 4mm 316 stainless rigging wire rope with a breaking strain of 1.75 tonnes. The cable will go over the pulley and down through the yaw bearing in a copper sleeve about 10 ft long with the power cables, I use welding cable for the first 15 ft down the tower where they then move to the outside of the tower to allow the furl cable a clear drop to ground level. The weights I intend to use are cast iron sash window weights, I have various sizes and weights to chose from. The tail vane is mounted below centre to make it top heavy so if the cable breaks or if you remove the weight the vane will fall horizontal and the machine will furl or at least that's the plan!
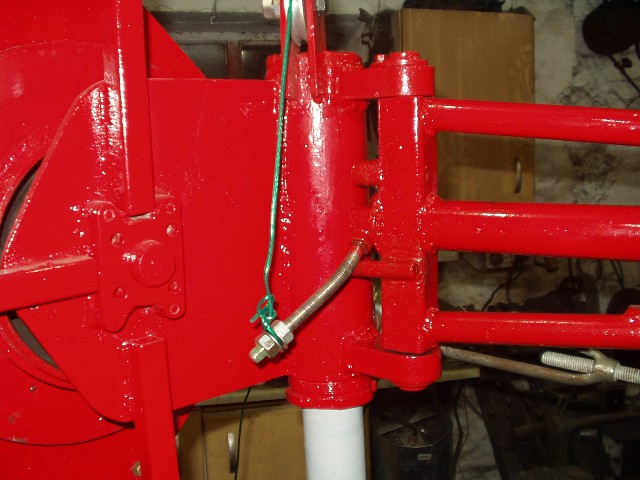
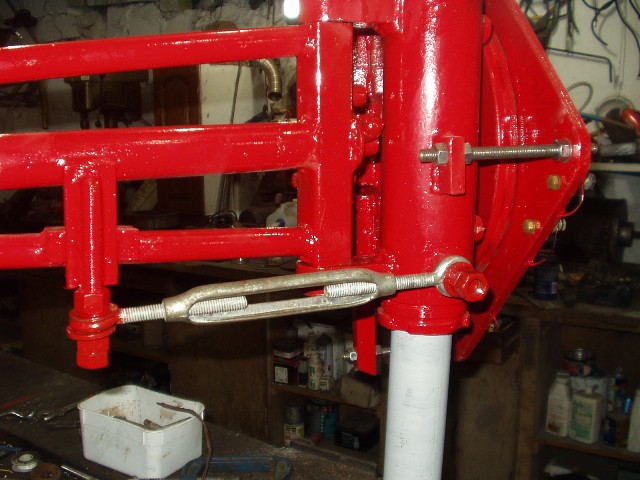
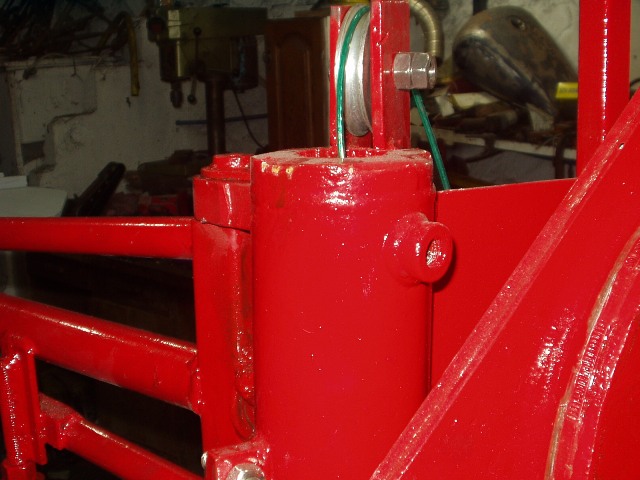
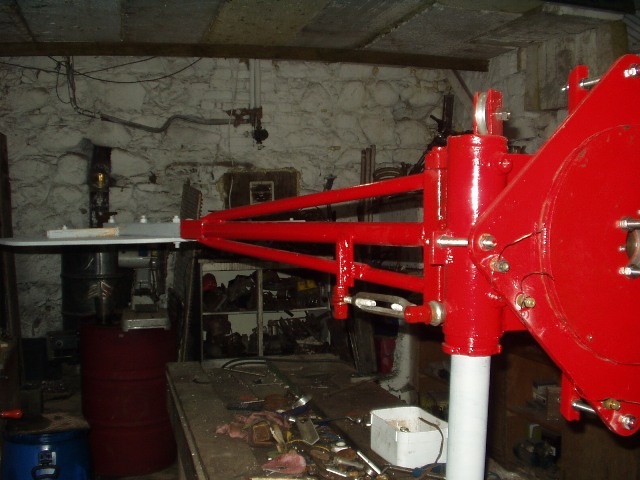
Im sure someone has tried this approach before but I have been unable to find it in past postings.
So there you go further updates will follow when I get it up in the air
As always all comments / ideas welcome
Seasons greetings from Ballyroney Northern Ireland
If you fancy a laugh have a look at the safety awards from our local radio station
http://downtown.bauerweb.co.uk/programmes/downtown/johnnyhero/wacky/safetyatwork.pdf