My Ahaa! Project, Auto Pitch VAWM
When I saw a picture of large size VAWT that setting public place like as the Park in some where, I wander why not those Wings have the movable Pitch to up wind, when thinking that, I got suddenly an idea came up my mind, that it!, might be possible pitch control simple devices applied like as "Swash Plate", it was trigger beginning my Ahaa! Project last December, remind that I saw the parts at Home Depot quit a long time before, it's a very large size of flat shape ball bearing made by tin plate, yes remember that time I had a curiosity about who use it? What purpose?
I have not surly plan and nor any reference information, but decided to start build a auto pitch control VAWM project with the condition of: (1).minimize expense as possible I can, (2).look around usable things & available resource. Realize moving object to proof a concept.
If the turbine shaft generates enough Torque, I d rather hooked up water pump but hold any expectation until I get good result on this prototype..
Frame must be rigid and robust for anti-vibration triangle pillar structure by 48mm & 25mm iron pipe.
Wing size: 250mm x 1200mm (Wight 980g) 5 wings supported by upper and lower hub ith spokes lower spoke supports each wing weights and 5 upper spoke have pitch hinge pivot.. avoidance any bent of pipe spoke which may trouble by the friction of inner push-pull rod. So it must be deadly straight without any vertical load. Otherwise change rod to wire.
Possibly "SWASH PLATE" is commercial name??, so I call those units here as "PITCH PLATE" Using two unit of Pitch plate, one is top for whether cook and second fix on gimbals under Frame head. top of free rotating bearing (Pitch plate) is to be fixed have a shallow angle to Rotating axis of weathercock, This plate angle makes displacement by wind direction Changes. From this slant bearing angle (not rotate) draw the information by two thrust rods each other 90 degrees placement. this pitch plate has two vertical rods an, one is connected to out side gimbals frame which set bottom of tower head and the second to inner Gimbals frame keep with 90 degrees position each other.
5 vertical pitch rods connected each bracket on free rotating plate on inner imbals, each rod connected Inner rod in spook through L clank on upper hub, rod end connected each wing hinge, so that wind direction Weathercock pitch plate angle and its element of inclination drive to relatively each wing's pitch angle.
Then when the wing passing rectangular wind direction (against), pitch angle increase To maximum, same time opposite position wing's pitch angle decease, other wing crossing neutral at both of upwind, downwind passing to neutral pitch angle from previous state. Wings angle is not center symmetrical since odd wings count.
About wings trying use the paper honeycomb, but changed taking styrene form core. I did not available to access any NACA Airfoil, so that making template easy way but it is beyond the aerodynamics.
Hand lay-up skin with bidirectional glass mat used with WEST SYSTEM, result of vacuum bagging with handmade perforated vinyl sheet, unfortunately finished many
small dimple both side of wing which caused not apply breather sheet on perforated one, actually I want make smooth wing surface like as Surfing board, however never increase Wight any more, compromised single layer by seems it enough stiffness.
Finally test result is acceptable, several troubles happened and fixed by miner Modification Look like All mechanism has functional as intended, however there seems to be a problem in Durability, tin made ball bearing might be work not so long life, unknown fatigue limit about all pitch control links used ball joint (using Radio Control model parts). Every parts has moving very busy. At now wind was small, scared the frame has happened resonance by vibration when attack the gust or strong wind, So Need more robustness and dynamic balance.
Wind flow was unstable since test place was close the building, I fond that when whether cook stopped some direction, then next wind coming from others, wing tend to rotate backward little bit, But whether cook get turn by threshold, wing turn back leading direction quickly that is almost looks like Jiving.
this time I have no room to use any stainless parts, because almost doable expense.
Unfortunately I have not available web to show other photo, if someone have an interest about all process of my trial and error, I can send those to provided FTP space for photo and video clip.
Now looking for some one have a large lath, I will hand made thrust ball bearing from way-out free Automotive parts. Hopefully next step I will replace 60percent large size (300mm x 1600mm) wing, within 1.5Kg. it is limit of maximum size at same frame, stay rotating Diameter should be 1500mm with some kind of strong spook replaced, now the most question is AIRFOIL, what type is suitable of NACA?
Hangar51.
Latitude: 43.33
Longitude: 144.26


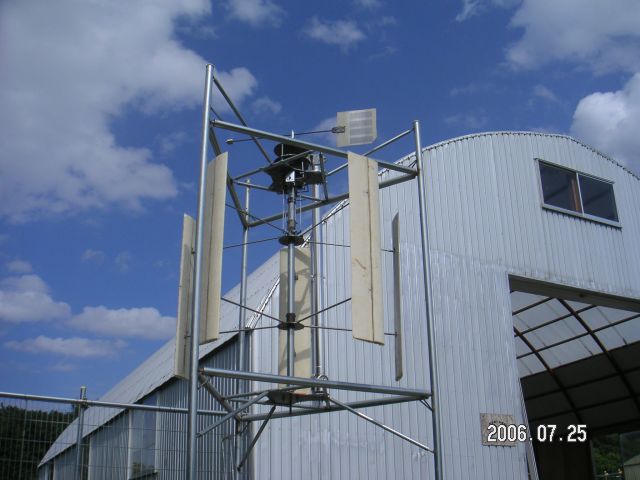