i found this dc current regulator i was wondering if it would work well for a windmill application
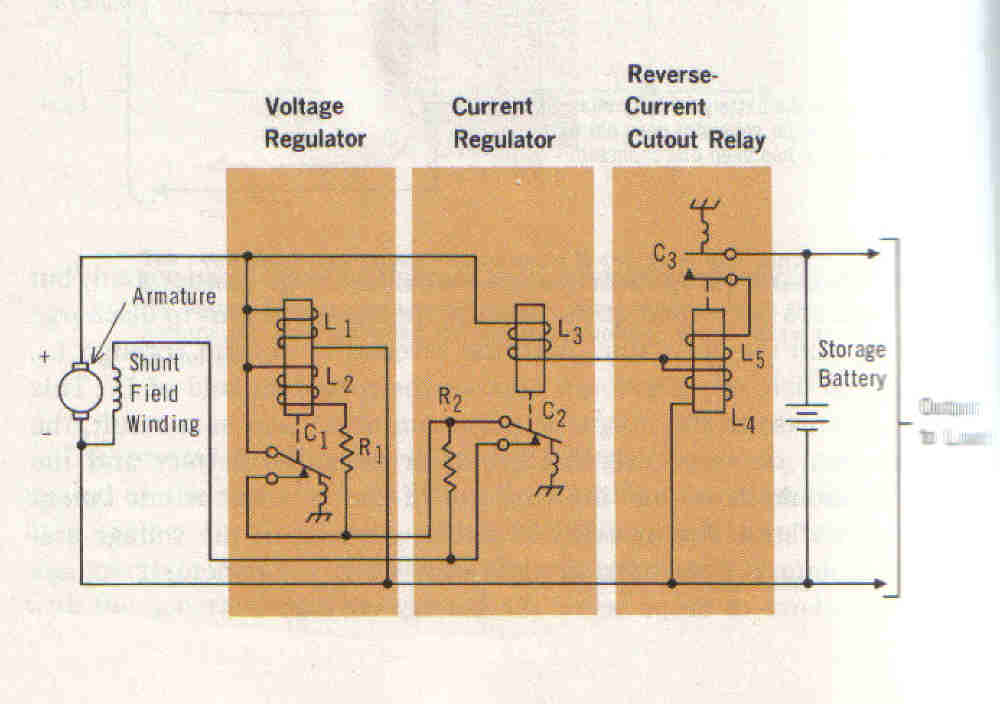
Electricity 1-7 by Harry Mileaf
I built my machine according to hugh's plans but here is the break down
the coils have 300 turns of #20 wire 9 coils
when the generator is spun at 60rpm one coil is about 5.2 acv
it only has one rotor with magnets on it but there is another steel disc on the othere side of the stator i used the 1.5x2x.5 inch neo's
there are five brige rectifiers that are 35 amp 600 volts
the rectifiers are connected in parralel
it is a two blade machine
the blades are 8 foot dia carved to hughs plans
the wire coming down the pole is #12
i have a 60 amp ammeter
What i want to know is what size type of components will i need to get so everything works out. my windmill is a 48v machine but i want it to charge at 12 volts will that schematic do this
i found another schematic by michael hackleman for a windgenerator controll box man that guy is a genius
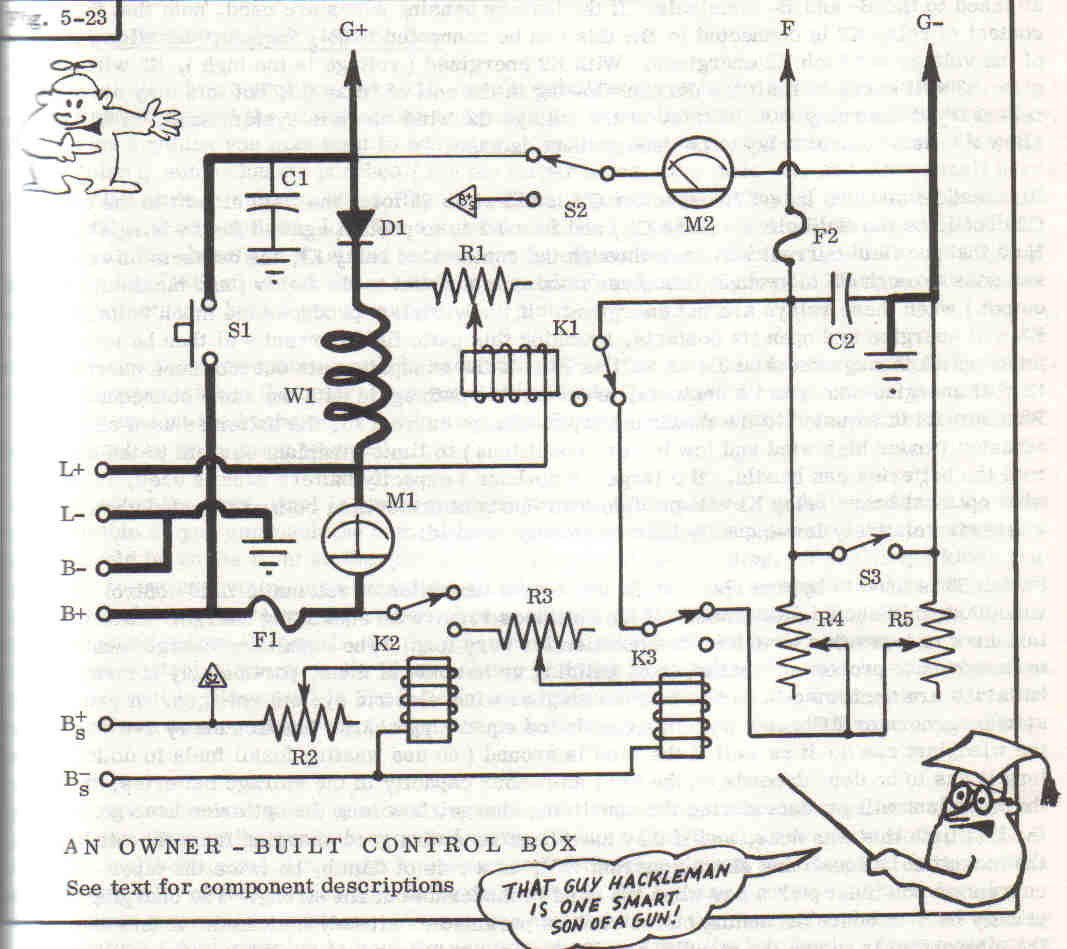
any coments will be helpfull
also thanks to admin for the FAQ which i just viewed it is very helpfull