Hi Scott,
Okay, I've been looking at the other part of the curve...
Here's an example of an inductor voltage(yellow) vs FET off time(purple) plot that my simple simulator shows:
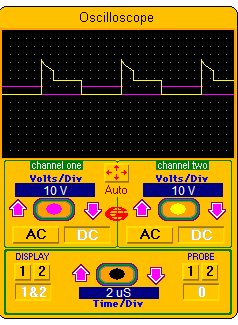
This is 17 volts in at 1 amp, 29 volts out, period = 20uS and duty cycle 50%
I think that the integration of the first part of the waveform is directly related to input power, if that can be done then no other sensors are needed for MPPT.
Also, no calculation would been needed for the off-time as the FET voltage drops to the input voltage as soon as it droops below the output voltage. (In this simulation, the FET is off for about three times longer than it should be.)
> The FET's voltage should be captured just BEFORE it turns OFF. When Inductors current will be at its peak.
Okay, I have to turn up the gain on my pretend o-scope to see the FET on-time...

... I think that you are saying that, with the proper sized cap, that I can use the current calculated from end of that curve times the voltage across the cap as the power calculation?
> If you can protect the ADC input and measure it at the right time then great! Do what ever works. Input voltage to ADC must NOT exceed its supply voltage.
Okay, what I was thinking of was putting a voltage divider in there to get the peak voltage below Vcc but then running it into the 20x gain stage. Not sure yet but am thinking that Vcc or less presented to gain stage might saturate the ADC at higher volts (but not blow anything) yet still amplify the lower voltages to get more accurate readings there.
I can schedule the sample and hold aperture on the ADC to the clock cycle and guess that with its 16pF capacitor that the value held will be the voltage very close to the end-time of the window. I haven't done the programing yet but think that by sliding the aperture across a few PWM cycles that I can super sample the discharge curve and get a fair digitization of it... just theory at this point.
> Was the 5 amps the peak inductor current? Or do you have 85w panel just waiting to be used?
I wish! In a nutshell, I hope to get a Harbor Freight panel set and test the three panels both in parallel and in series. I'm guessing that bucking will be better than boosting but would like both circuits to handle two or perhaps three sets of panels. I can't invest much in solar right now but think that 5 amps could conceivably be a lot of watts in the buck version ...
How does that sound?
- Ed.