Hi Henry.
I posted a story some time back on this subject. I use tredmill motors as a drive motor for motor conversion tests. I had looked at the Harbor Freight router speed control ($10 to #15?). I took the HF apart and part for part it was identical to my lite dimmer.
Next I took an old car amplifier heatsink and mounted the dimmer to it with some heatsink compound. I added an AC receptical at the end of the heatsink.
The output is fed to a fullwave bridge rectifier then the DC is off to the tredmill motor. Since the RPM on the tredmill motor is 6,000 tops, I used a small belt pully on it and a large belt pully on the motor conversion.
I also used my Lazer Tack to take rpm readings, Fluke true rms for voltage reading and an amp meter.
I tried the big caps but that didn't work well. Go without the big cap.
If you would like to use my complete setup just e-mail me or call or come buy the store. The hole things been setting on a shelf for a year now.
Heres a few pictures. I hope they're not to big? Please forgive if they are?
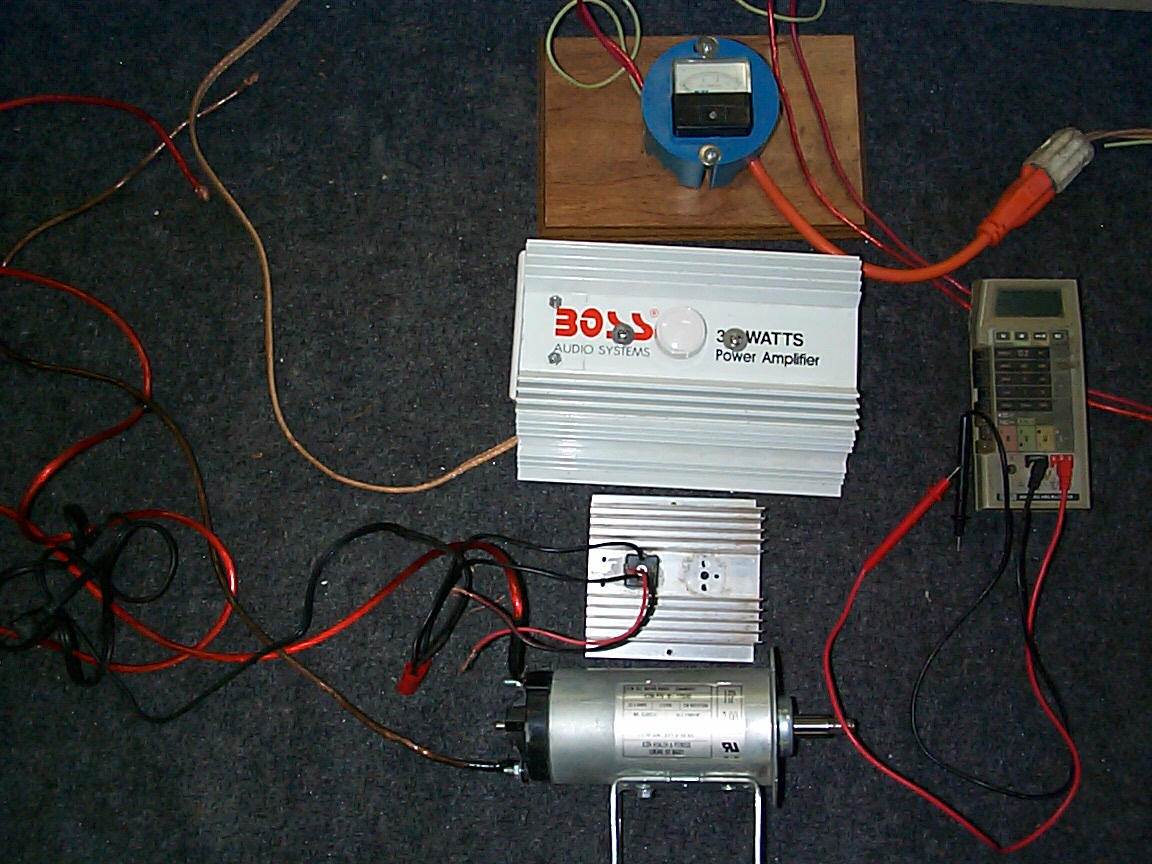
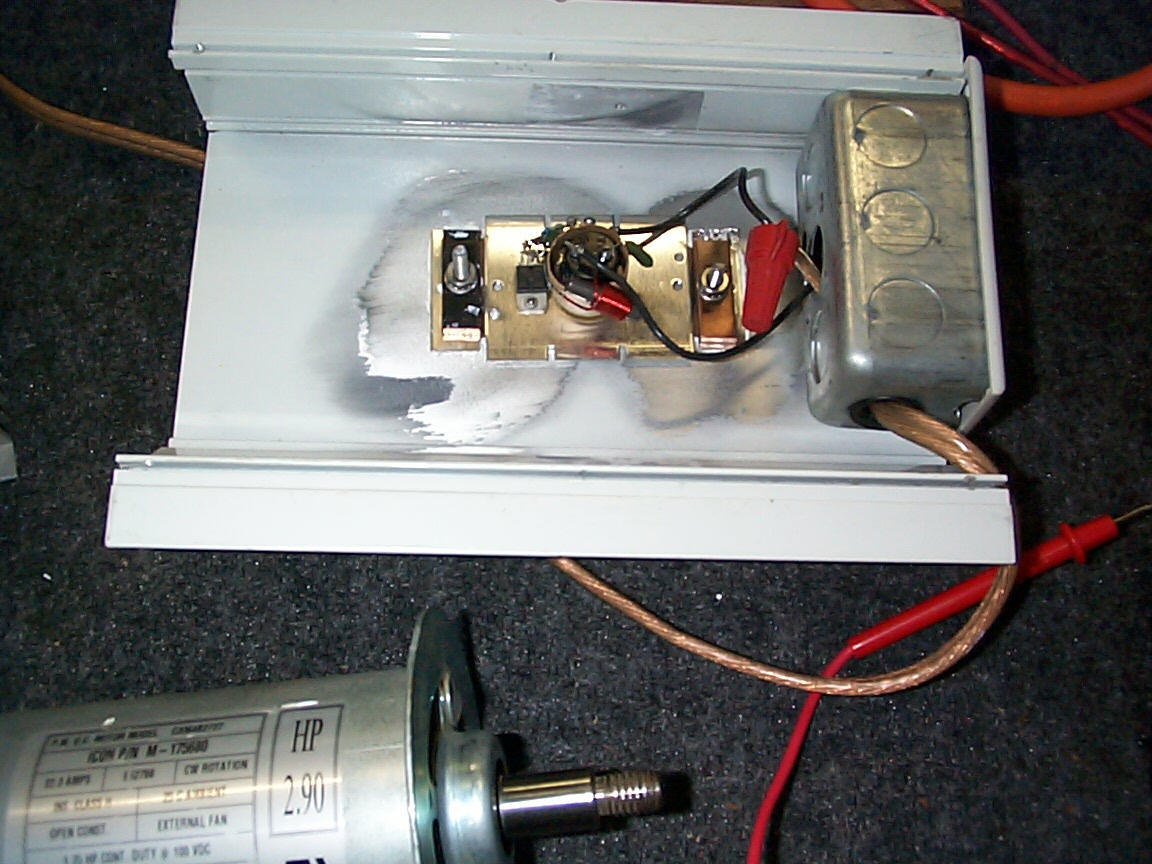
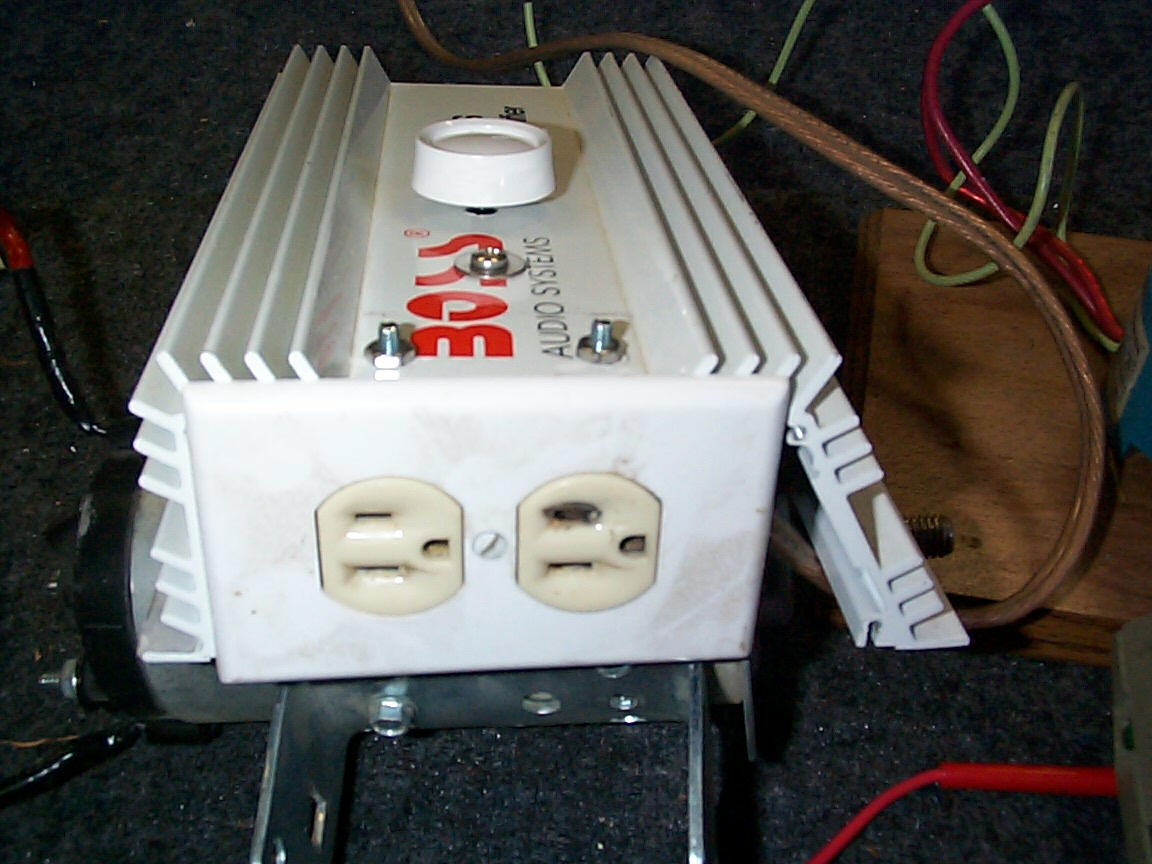
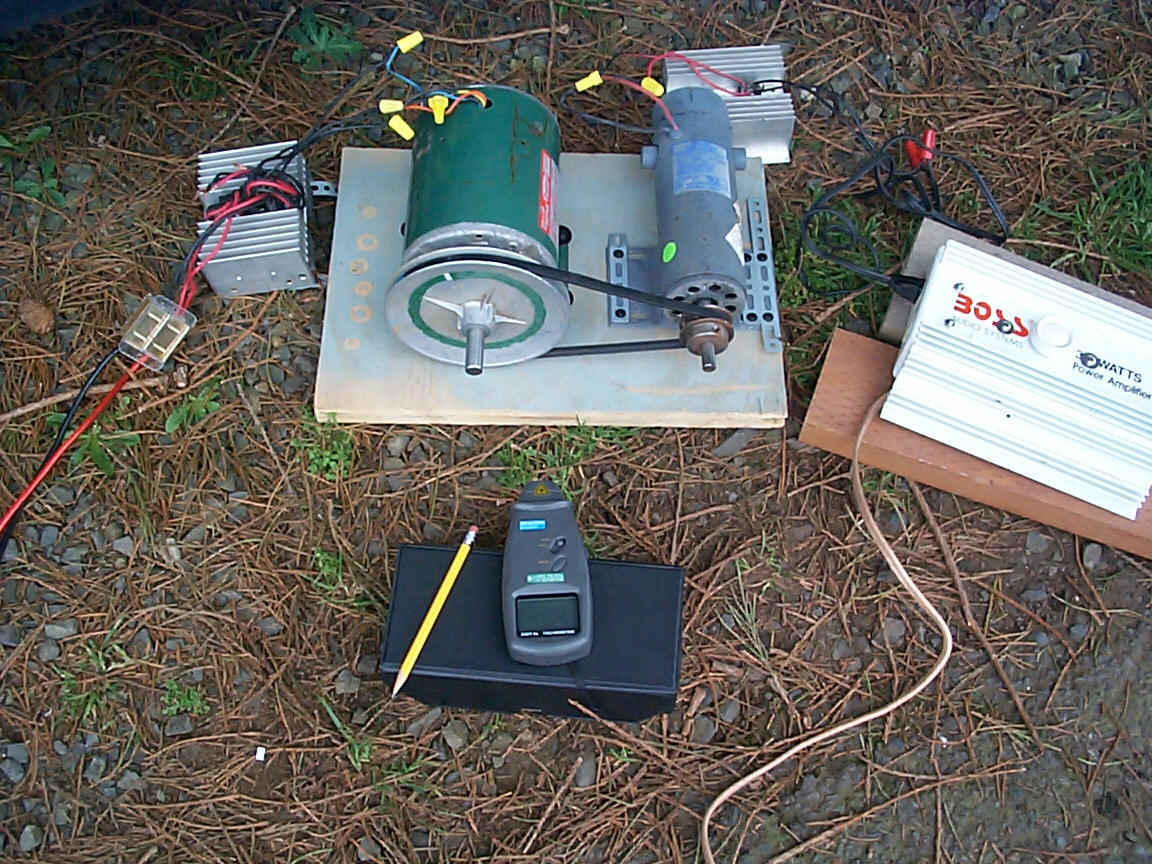
With the added heat sink this controller works very well. I had no heat problrems at all.
JK TAS Jerry