"It would make me feel better if you used two hub plates, on the front and back." - Sparweb, you win the best comment from the audience award today...
So last weekend, I took the windmill out again and left it up over night to take advantage of some 18 mph winds that were building up towards lunch time the next day since my 18650 cells were almost dead. At 6:43 AM, I decided to look outside at the windmill in the back yard and was trying to make out if the blades were still there and if they were spinning. Well, about 10 seconds later, I got to witness the whole thing explode and throw the blades in all directions. The front leg on the ladder took quite a beating from the one blade and the other two blades shot off into the woods in either direction. When the blades flew their 100 feet in either direction, they struck the trees and sounded like wooden baseball bats being thrown into a pile.
Upon closer investigation, I've deduced that the blades did not hit the ladder first, but rather the hub had ripped in half along the grain by centrifugal force. I had confirmed this by comparing the dent in the blade to where it hit the fiberglass ladder.... seeing that the blade had to be about 6-8" lower than where it normally would be. Impressively, all 3 blades were in really good shape afterwards and they are definitely re-usable. The shaft on the motor appears to be straight still, but I'll have to use a dial indicator at a later point. The ladder on the other hand didn't fair so well and had lost all of its structural integrity... so that's going to cost me about $200 for a new one. The batteries flew out of their holder and about 4 of them were driven into the mud 1". I figure it was spinning at about 1,000 rpm when she let go.
In the span of less than 6 hours, the windmill generated about 4000-5000 mah. So I must of had the wiring correct, so that's now validated.
So the lesson here is that it is a really good idea to use two hubs to sandwich the blades together to both lower the bending stress in the hub and to distribute the load. It's also likely a good idea to add some additional fasteners. I figure there was a few thousand pounds of centrifugal force on each blade, especially since they were at least 3X heavier than my previous 5, 6 and 8' blade sets. Also it would be a good idea not to use poplar as a hub.
Here is a video of it going relatively slowly in probably 8 mph winds.
And the carnage video afterwards.
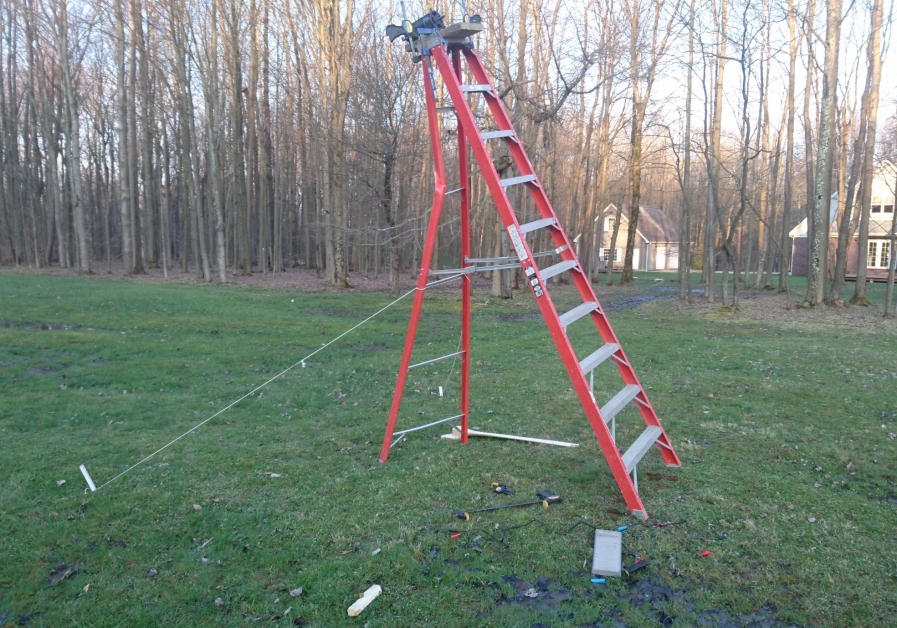
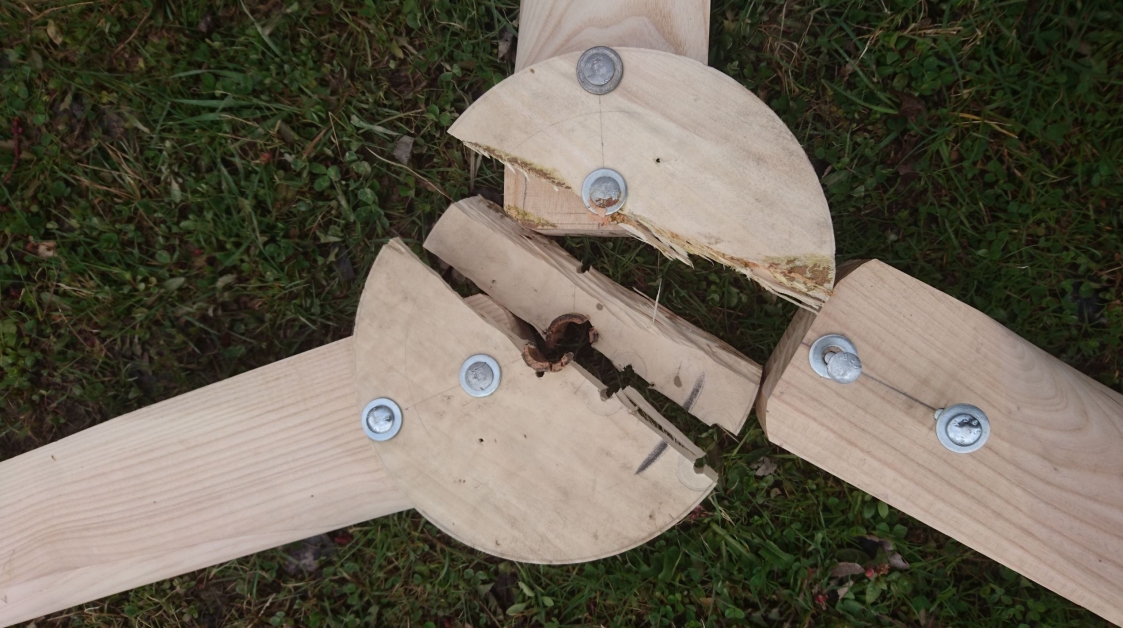
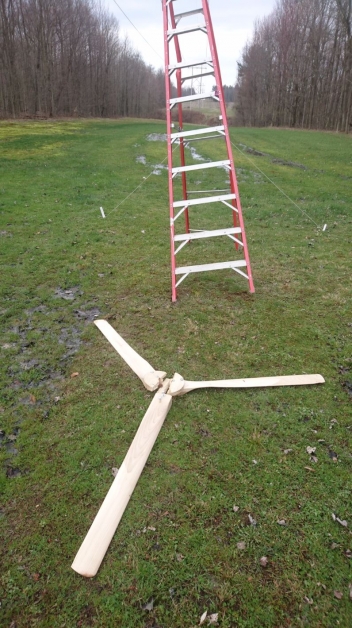
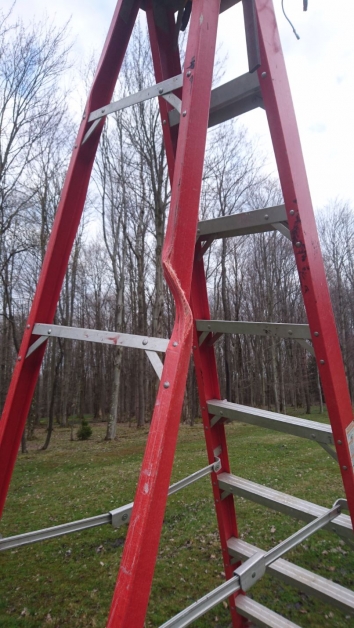