After not seeing much improvement with the 12 pole vs 6 pole swap, I decided it's finally time to add a second axial flux alternator to the shaft.
Specs on the old is are 9 coils, 12 poles, 212 turns, 22 gauge, 5/8" thick coils and 3 phase. The new one is going to be 12 coils, 6 poles 200 turn, 24 gauge, 3/8" thick coils, and dual single phase.
The goal is to wire the two 6 coil single phase alternators in parallel after the bridge rectifiers to be able to match up with the 22 gauge of the first alternator. Then put both alternators in series. I'm hoping to drop the cut in RPM from 90-100 RPM down to ~40-60 RPM and also increase the peak current to 8-10 amps.
I have 3 coils wound on the CNC machine already.
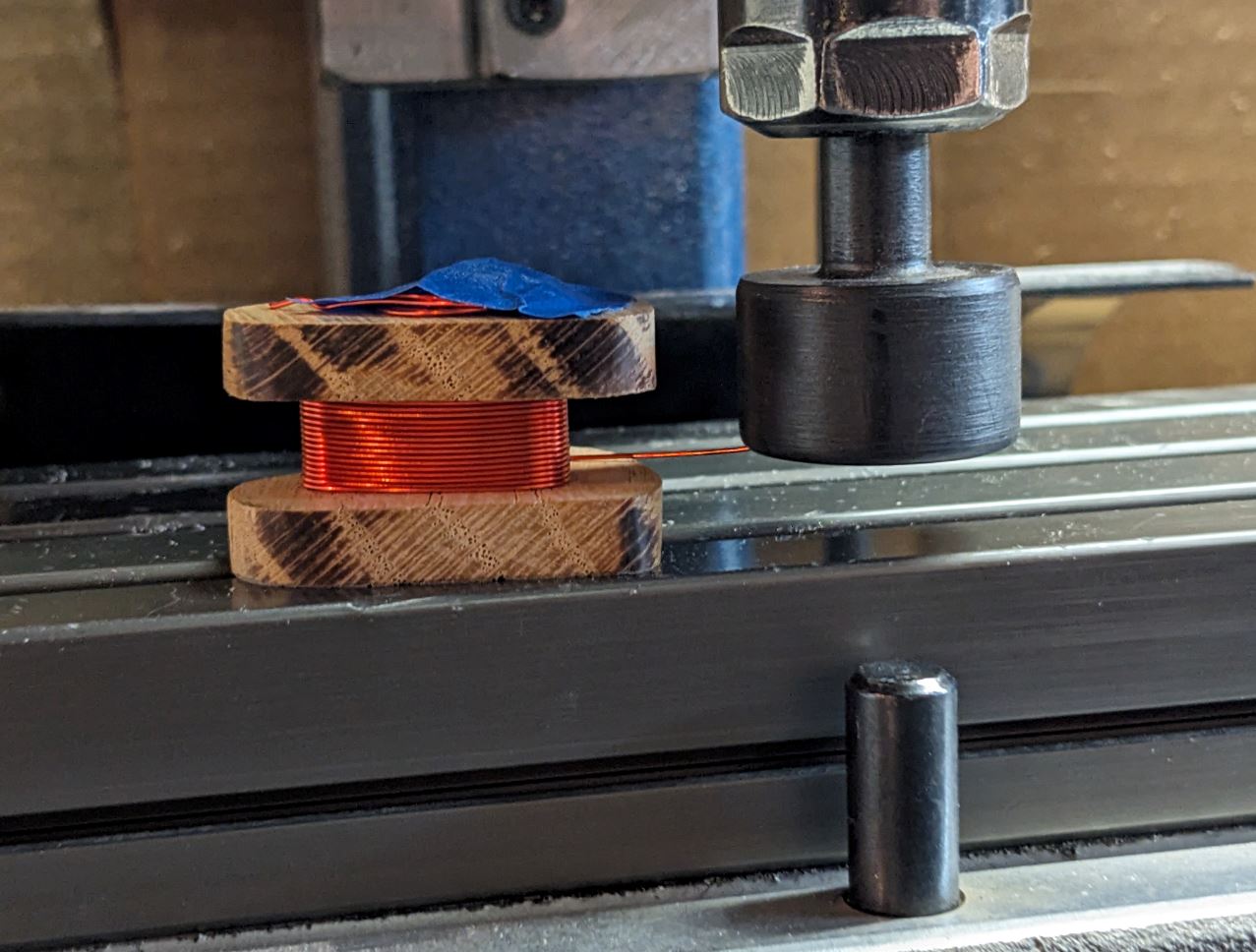
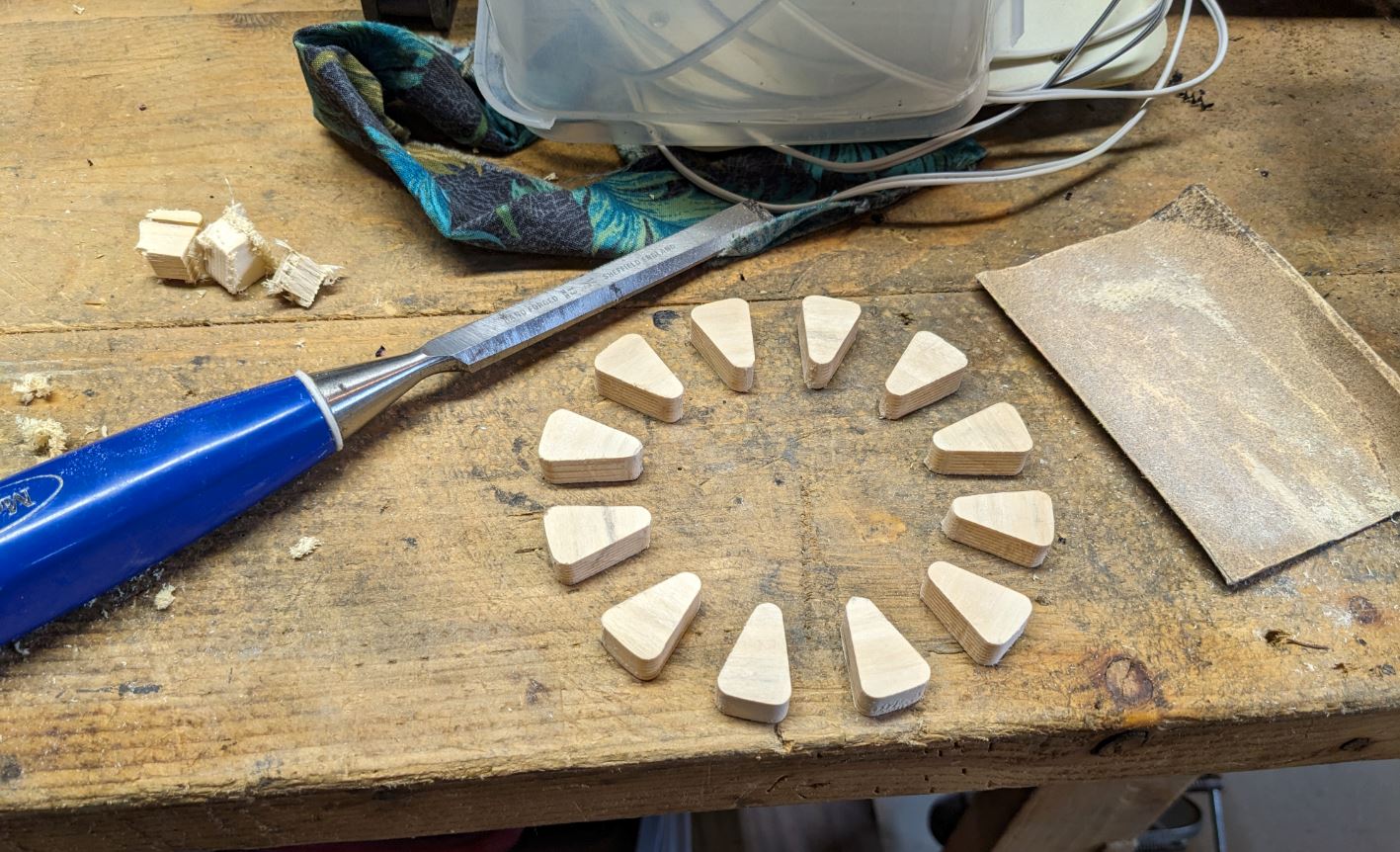