Very interesting way to produce a ring without a massive quantity of steel.
About the end plates i considered that point, at this moment It's not my most important concern.
I dont know if i will use resistant UV canvas to save weight or the same material of the blades and to live with that extra weight.
About the two blades or three, I can understand that when studies have been done the best results were obtained with 2 blades. But what those studies did not take into account is the extremely slow rotation speed of a savonius at this enormous size.
It is the same thing that happens with horizontal turbines, if more blades are used they work with lower speed winds but with higher speed winds the turbulence between them makes them lose efficiency compared to models with only 3 blades.
then all the lifting effect that could be given in a much smaller savonius turning at many more rpm will not exist here. On the other hand, the problem of the moment of negative torque when one of the two blades is in its worst position, can affect the smoothness of the turn.
If you look at the turbine from the front (at least what I can see with the naked eye with my 2 meter model) there is almost no point where the blades can have significant negative torque.
And since the rpm is going to be very very low, I depend purely and exclusively on the drag effect. And the day the turbine suffers very severe winds, probably the turbulence generated by having 3 blades will help it not even reach its maximum tsr for that rare wind speed.
When I started the prototype to see the feasibility of the project, my goal was that for that size of turbine it could reach 50 watts at a 20k/h wind.
I only did 3 tests on the coast with it (where it had a relatively stable average wind of 20 k/h. In the first one it barely reached 55 watts because the maximum wind peak was 20 k/h (that were sustained for a couple of of seconds maximum) and the average was 14-15. The second time I went there was a little more speed an average of 16-17 and peaks of 21-22k/h and reached 80-85 watts. The third time the average was 18-20 and there were gusts of 25k/h and I think I read a reading of 130 watts before I burned out all 7x 12v bulbs that I had added as a load. Honestly, I'm not very sure if it reached 130 watts or not, it was all very fast and when I ran out of charge the turbine began to speed up a lot.
But the point is that I long passed my watts target so that scaling the turbine to larger sizes would be interesting for me.
If anyone has been able to see videos of large commercial savonius (2.30 meters maximum height) such as the luvside, they may have noticed how SLOW they rotate even in the promotional video.
Well, my turbine probably turns the same or slower than that, and 3 blades will give me more positive torque moments than just 2.
I consider that due to my design commitment, I may lose some efficiency on one hand, but gain it on the other. The luvside for example, at first glance they seem quite heavy and the wind has to charge a very heavy rotor with energy before reaching a generation speed. That limits it to moderate to strong winds, and in low winds with some gusts of more speed, that extra momentary energy will not be used.
So try for a moment to imagine a turbine turning at probably 30-40 rpms and you will understand as I do that the same fluid dynamics that apply to small scale prototypes that turn at 200 or 300 rpms do not apply in other very different rpm regimes. (in fact my first prototype on a very small scale, just 4 cm high and 20 cm wide, it reached 900 rpm without load at 22k/h.
In fact, have you been able to see savonius, whether commercial or homemade, that generate some useful current in light winds? I couldn't find them on the web. And I think the problem is that when they decide to scale a small prototype (beyond a cost issue) to something bigger, the materials they used for the prototype are not suitable when scaling up. And when they are forced to use steel to reinforce the entire heavy structure they end up with a very heavy rotor in order to draw current from a light wind.
I try not to repeat those mistakes with a design that improves the compromise between the resistance of the rotor and the total weight of the moving parts.
And taking into account that the turning speeds are going to be very slow 80% of the time.
Regarding the measurements of his PMG, I imagined they weren't going to be very small, there are no shortcuts to anywhere worthwhile. But I'm still interested in seeing your setup.
The commercial models that cost about 8-12 thousand dollars that really are for very low rpm ( i not consider 300 or 200 rpm so low rpms...) are also usually very large and heavy, 75-80 kilos at least, and this taking into account that they optimize the design quite a bit with the type of magnets and aluminum housings that they use.
So I already accepted the idea that if I want something that works at very low rpms its weight and size is going to be big.
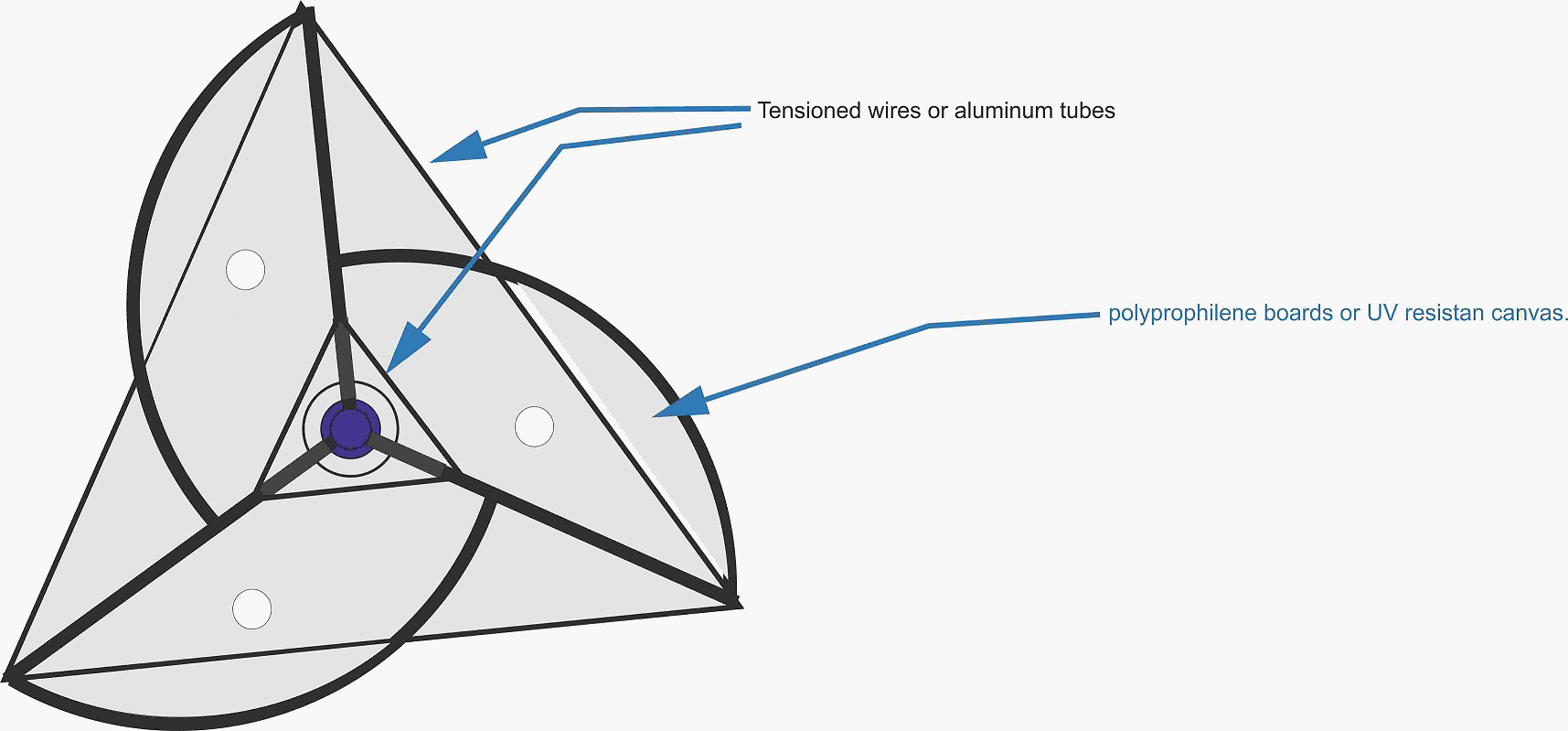