Seems a common problem for people is how to mount blades to a motor conversion shaft.
Well, here goes my sales down the tubes on these hub adapters

This is how I am making some to sell for my Blade hubs I'm selling on E-bay.
You can do the same, cheaper yourself and these are mighty strong heavy steel!
My other diary, NTL designed Blade hubs here.
http://www.fieldlines.com/story/2007/4/14/03728/3458
This is a NTLsuper6 daisy hub. Notice the 3 small 1/4" bolt holes near center hole for mounting it. The holes fall centered on a 1.5" circle. The center hole is 0.7"
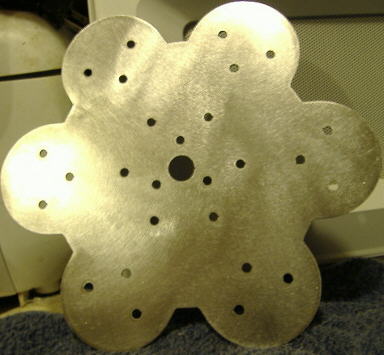
Here is an X series weld on hub, sold in farm stores and such. G&G is one brand, Weasler or Weaser is another. They come in various sizes for the center bore, this one is a 5/8" with keyway and 2 allen set screws 90degrees apart.
An X series like this G&G is 2.25"OD on the large end. Plenty of room to drill and tap for the 3 holes 1/4" I want for my hubs. You can also get smaller hubs like this as W and V series, all are made in various center bores for shafts. A W series is 1.81"OD and V series I think smaller yet. I have 2 odd ones that were 2.5"od with 1/2" center bore, not sure what those would be, but they do exist also.
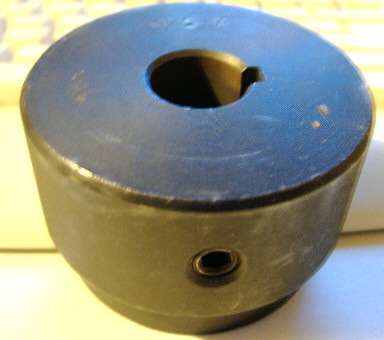
It is very important of course that you get your hubs centered on each other, if not they will wobble or run oval/egg shape in use. Here is a simple tool you can make from a broom stick or dowel rod of correct size. Since I will be doing many of these parts I made something a bit better for myself. I'll clean these up and knurl the centers and possibly chrome plate them also to prevent rusting. Each end has a size to fit a center bore for a hub. Maybe 1/2" one end, 5/8" other end, both ends have a step up then that fits the center of my hubs. These fit tight so no wobbling off center when puching marks. Make yours for the sizes you need, I need all the main size bores myself.
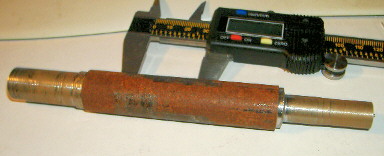
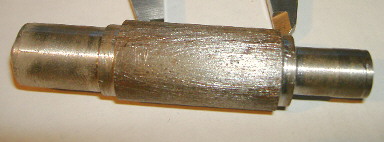
I turned mine on my lathe from steel, if your making yours from wood you can rig up something with a powerdrill, couple boards and some screws for a simple wood lathe, take it easy and be carefull and you should be able to turn alignment pins like these from a broom stick and a cordless drill that will work well.
So once you have the pins made you simply slide the pin into the hub center then into the center bore of the shaft adapter. Make sure they sit tight and flat together, then use a self centering punch in the 1/4" holes to mark your drill spots. Make sure you drill straight down into the weld on hub, use a drill press if you can. And also make sure that your holes are not going into a keyway slot or setscrew!!
Perfectly centered blade hub, shaft hub under it, ready to center punch.
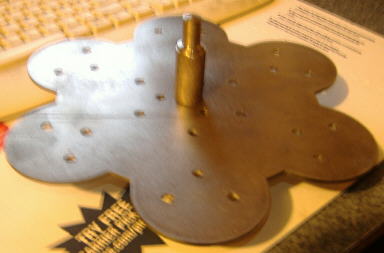
With an X or W series hub I have here the front to rear size is 1.5" deep. Drill and tap as far as you feel you need too! Or drill all the way through and put a nut on rear, or feed bolt from rear before mounting and put nut on front. I will be drilling and tapping mine as planed for now, but I am cutting the hubs down on the lathe making something else out of them.
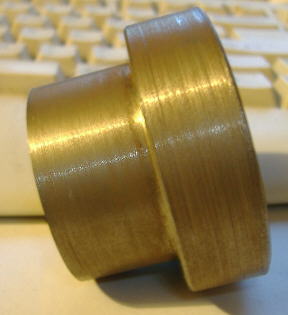
Adjust any sizes, number of holes, etc.. to the blade hubs and shaft sizes you need, if you can find the X, W, V weld on hubs series in the size you need this is a good way to make a shaft adapter. Cost of parts will vary, maybe $7 and up for these weld on hubs. Mine will be allot more, but lots of work at time going into them!!