my next step will be to apply
the tubing to the out side
edge as you have depicted.
what are your thoughts
on solidity as a percentage?
---
I think that you could start with
a similar solidity as used with
Darrieus machines. There is available
one really good web page:
http://windturbine-analysis.com/index.htm
In his prototype the guy is using a rather
high solidity Nc/D = 0,42
---
the airfoil profiles you
have drawn look "right".
This is where the real science
is required, to produce
the optimum ratio between
vain thickness and vain width.
You are considering using cloth
as a surface, to allow
the airfoil to form itself?
---
Yes, if you'll use a tube on
the leading edge, I think
that cloth could be a good choice.
I think that the airfoil
would form itself quite well.
One of my friends In Finland
has made HAWT rotor blades
using a tube in the thickest
part of the airfoil, polyurethane
on the leading edge, a steel wire
on the trailing edge and covered the
blades with cloth. They are working
really well.
---
consider this, if the sections
of the surface removed to
form the rotors (waste)were
reapplyed along with the tubing
over the remaining sections
it would create a profile
similar to that which
you have drawn.
---
I think that would
be a good idea.
Do you think to use a tube
on the leading edge?
One more drawing with also some
new suggestions. You might try
using polyurethane on the leading
edge and cloth to cover the vanes?
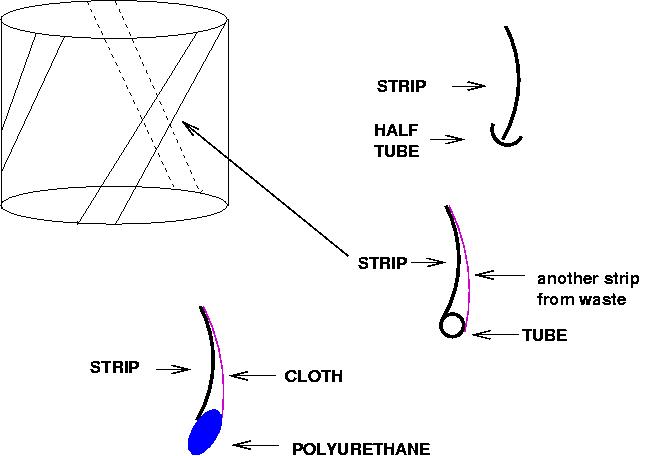
Which kind of tube have you tried to use?
Metal or plastic?
How thick are the walls of your bucket?
Is the bucket made of metal?
Have you got any pictures of your
prototype?
- Hannu