Thanks for the reply Ed,
(Admin - Sorry for the double reply, but I realised after I did the first one that it wasn't a reply to Ed's reply, but to the original poster. Assumed Ed would not be aware of my reply.)
Most of the information I have been able to find comes from http://www.ecoinn.co.nz They state in this file http://www.ecoinn.co.nz/pdf/smartdrive_wind_turbine.pdf that the Cogging force in grams measured at perimeter of rotor for an uncogged stator is 900-950. After the stator has been decogged, it is 450-500.
Based on what your reply was, I would need to build one a bit bigger if I want it to start in lighter breeze - any suggestions for a starting point?
I have rewired mine as an 80SP which is supposed to start generating usable watts a 250-300 RPM - well enough for me, I'm only looking to keep a single 120A wet cell deep cycle charged that has a constant 5.5-6A draw on it. (graphs at the bottom of this file http://www.ecoinn.co.nz/pdf/smartdrive_what_is_it.pdf).
Also, since I'm not really comprehending some of the settings you guys use mentioning, I was going to make my wing adjustable and measure any RPM differences.
I also thought of an idea, since kitno455 mentioned it here(if we could only get rid of the downwind blades - http://www.fieldlines.com/comments/2005/8/18/19637/0978/7#7 ). This modified diagram of yours will describe it better.
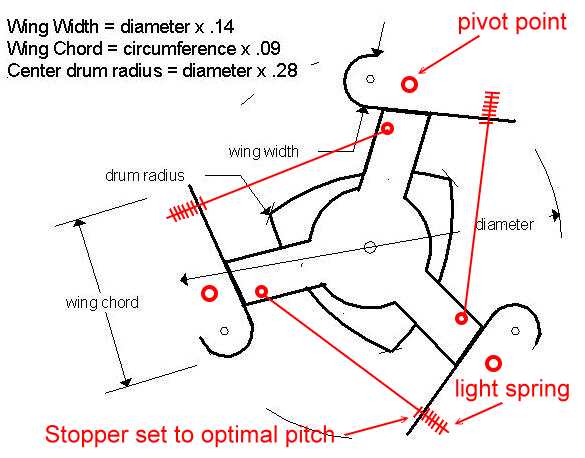
As a newbie, I'm probably treading on covered territory, but I'm going to try it. I'm thinking that as the wind hits the back of it, the blade will be forced to a more accute angle and actually acyt as wing and generate power rather than resistance. At worst it may spark some new line of thought. :-)
BTW, I am building to your current design. The above image was the easiest to find and use to describe my idea ;-)
Greg