Last year (2004) I helped my friend Erkki Nousiainen to make a new wind rotor for his old wind machine.
The machine has got an induction generator with
a gearbox. The wind rotor diameter has been originally 10 m, it had two FRP blades. There has been a pitch control mechanism.
Last year (2004) we started to make a new wind rotor of wood for it, 10 m diameter.
'Eki' discharged the pitch control mechanism, which he said never worked really properly. I made for him a new design for the blades.
The design of the rotor blades was based on an idea of a wind machine builder called 'Reinikainen', who made some big wind machines in the nearby area earlier. The blades are made of wooden boards.
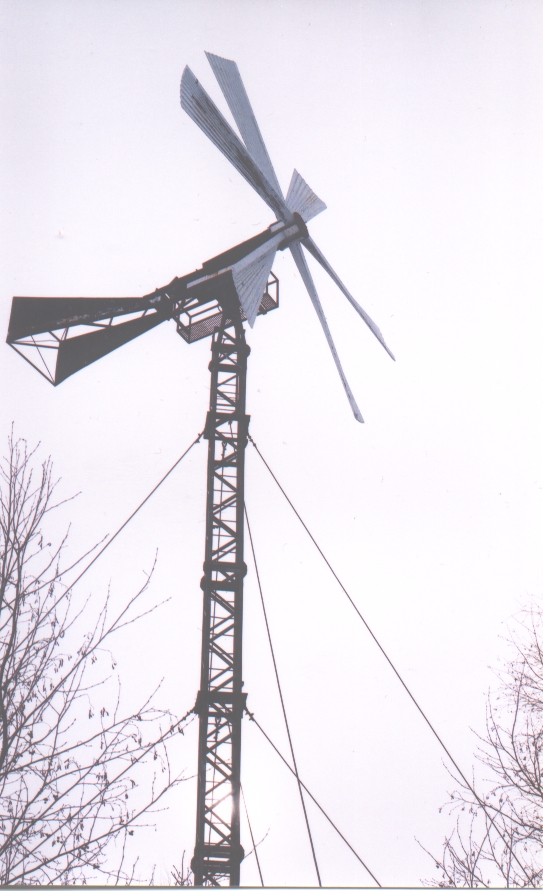
Here is a picture of an original 'Reinikainen machine', which is still working after about 15 years in use.
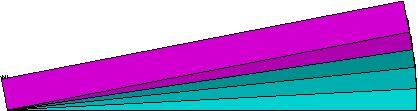
The blades are made by laying wooden boards on the top of each others like a fan and then using tools.
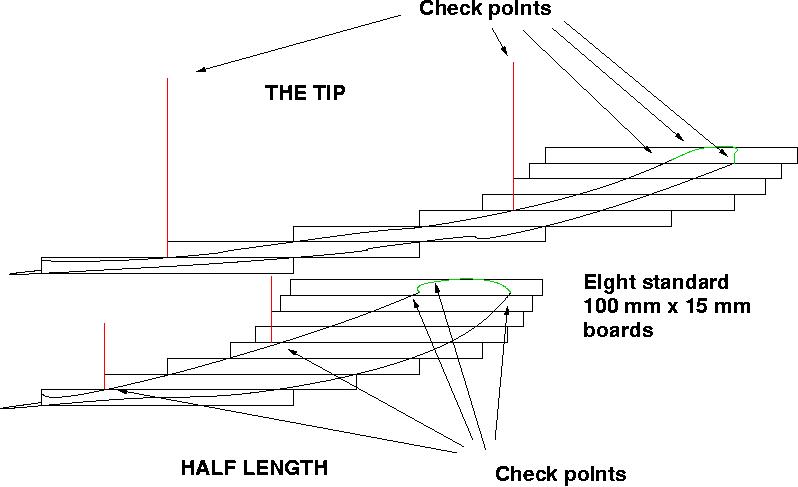
My plan was to use on the tips the K2 airfoil.
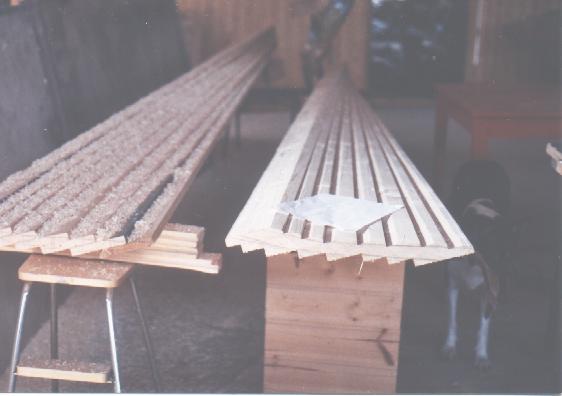
Here is a picture how the blades were made in 'Eki's workshop.
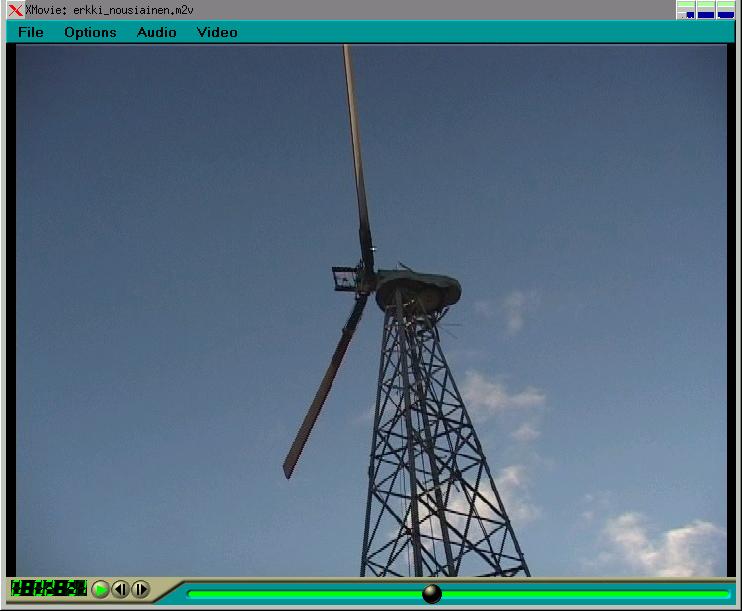
Here the blades are installed on the wind machine, of 'Eki'.
There is no pitch control mechanism used, but some working parts like the counterweights were left there...
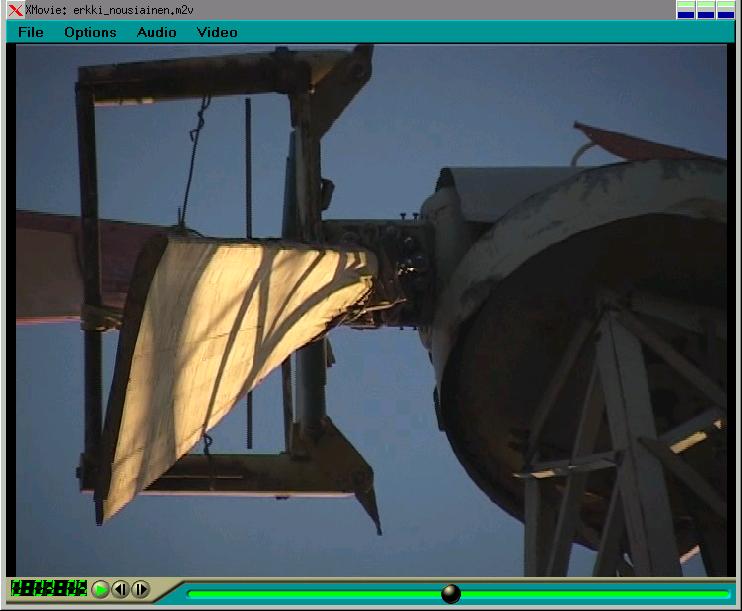
Here is a shot of the blade tip.
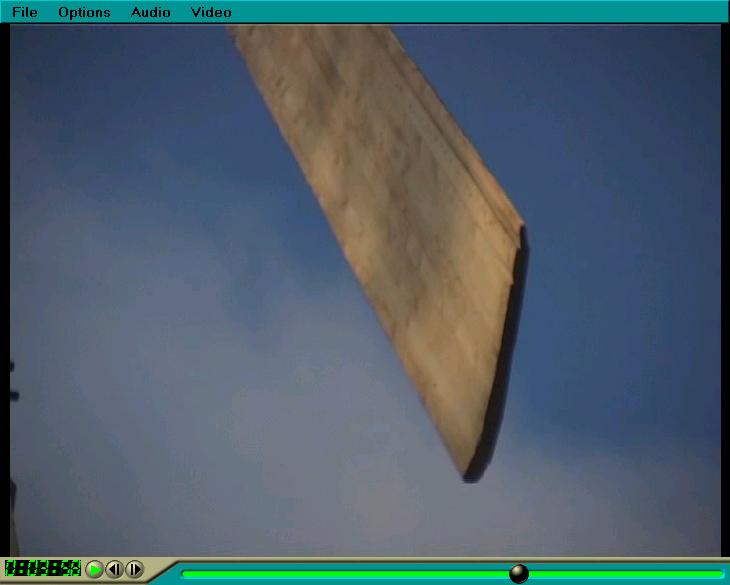
Another shot of the tip of a blade showing clearly the K2 airfoil.
The last three pictures are taken from a video tape as made by 'Ossi'. We are working with the video, there is lots of other information about 'Eki's other machinery there.
---
Unfortunately 'Eki' didn't manage to get the induction generator working. He left the machine turning free during a stormy night in the winter 2004. At that time I was in India. I heard next day by email that the wind rotor was broken.
In my opinion the wind rotor was really successful. It was going quite fast, at least when going 'free'. 60 RPM was quite easy to achieve.
It was broken because of the too fast speed and mainly because the old weights of the discharged pitch control mechanism went loose and started banging 'out and in'.
---
Now a new wind rotor consisting of eight blades is almost ready and 'Eki' has tested the generator so that it will work at this time. During the next week we are planning to lift the machine again up...
- Hannu