At first I'll mention that me and my friend are trying to construct the device that costs around 100 k$ on the market. We'll spend around 1k.
The following is a serie of pics of our first attempt. Before any serious work we built small scaled laminator just for the purpose of learning, choosing the right materials and experimenting, without any expenses (just 30 $).
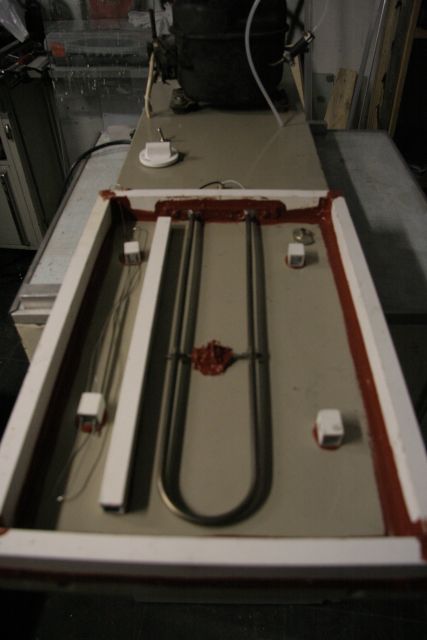
This is our construction yesterday, when we assembled it. We got to quit the work for one day because silicone needs some time to become harder.
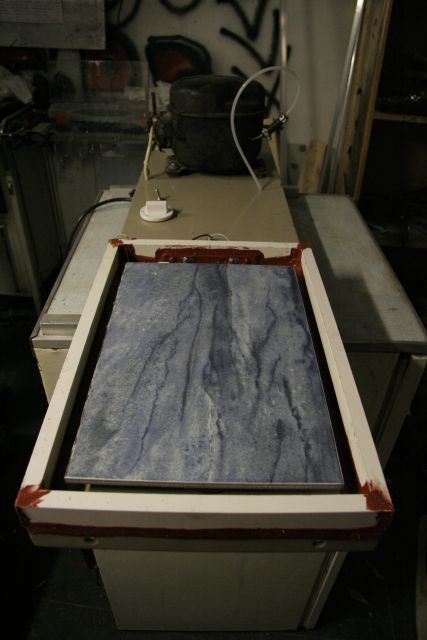
We are using ceramic tile in this model instead of copper plate. Hope it'll work.

First try of closing the lid. We put tempered glass instead of top chamber, just to see what's happening in there.
Before this I try to put EVA and TEDLAR sheets in my kitchen oven, to see what's happening. Lot of air was captured between the EVA layers, and that is going to be solved with vacuum pump. Hopefully.
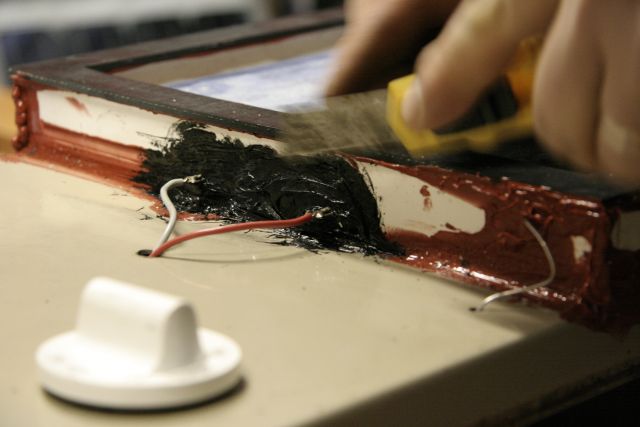
Yesterday, before we quit the job, something goes wrong. Holly smoke was released from the heater. I know it's hard work to put it back inside. I think that was because the silicone was wet, and make contact (shortcut) between heater contacts.
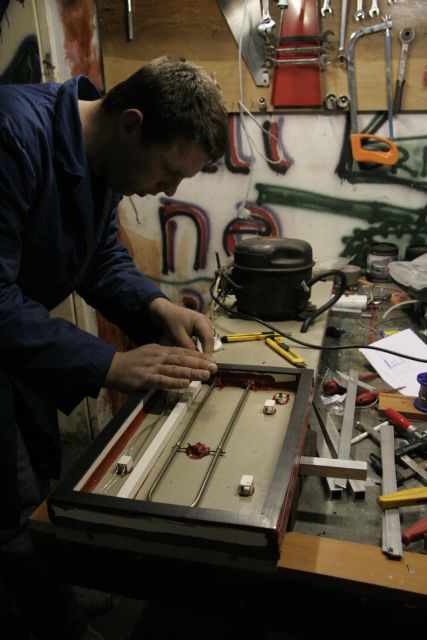
This is me putting some grease on the rubber sheet used for sealing the upper glass. The grease is some 30 years old military grease used for cannons. Still good, it seems.
When we tried to put the inside space under vacuum, we realize lot of leakage between the glass and the rubber seal. With grease that was solved.
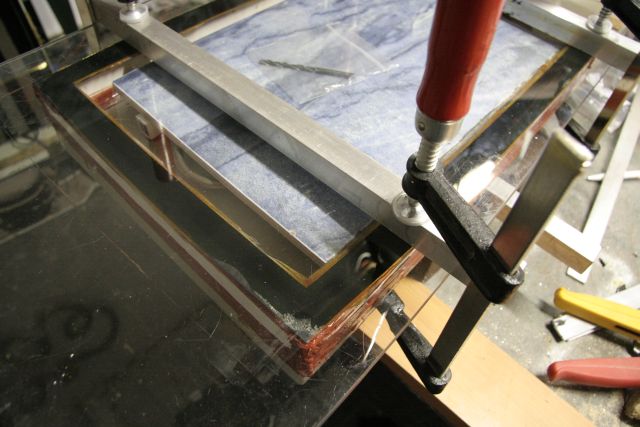
This is machine under work, with plastic bag inside. Inside the bag is a drill bit, to test vacuum it. We hope it will work.
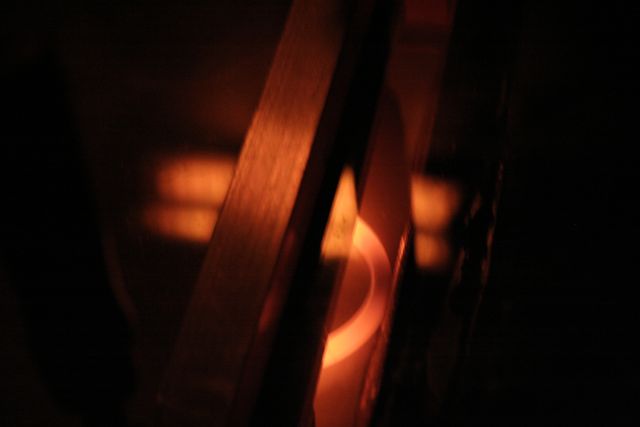
The heater on the run. We set the thermostat on 180 degrees, but it's ordinary household type. Not sure how accurate it is.
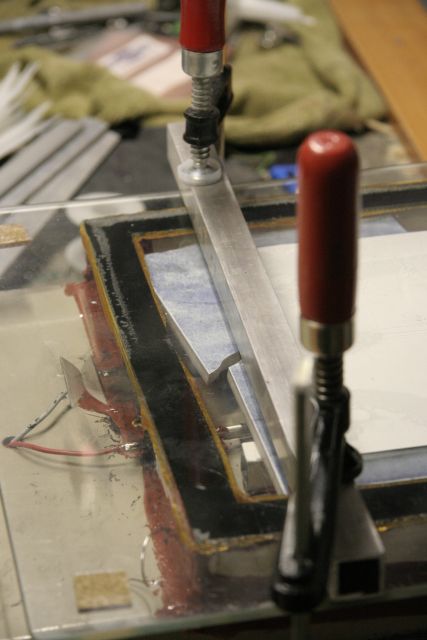
After about 5 minutes and 100 degrees achieved we heard the crack, and the tile was broken. As the inside test glass with sheets was totaly up with the upper glass, we let it all that way, hopint it would laminate.
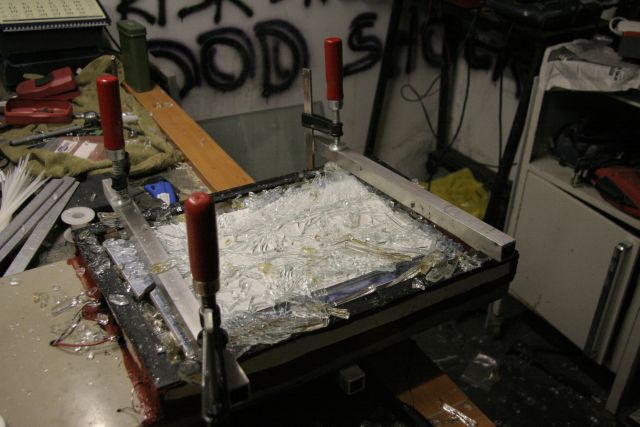
Another 5 minutes , and just after I said we should terminate the process, we heard large BANG! The glass goes apart. We're lucky it's vacuum inside, so it really implodes, not explodes. Now to se what we have in there.
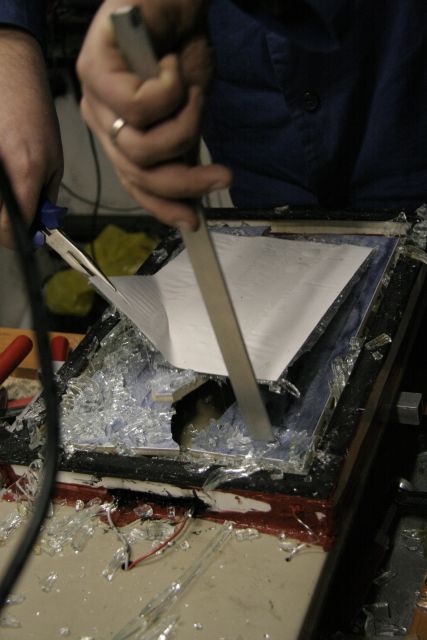
Taking the laminate out. Before this we had to remove all glass parts. maybe it was better idea to set the laminate layers opposite direction, so we could see the entire process thru the glass. TEDLAR (upper sheet) is non clear.
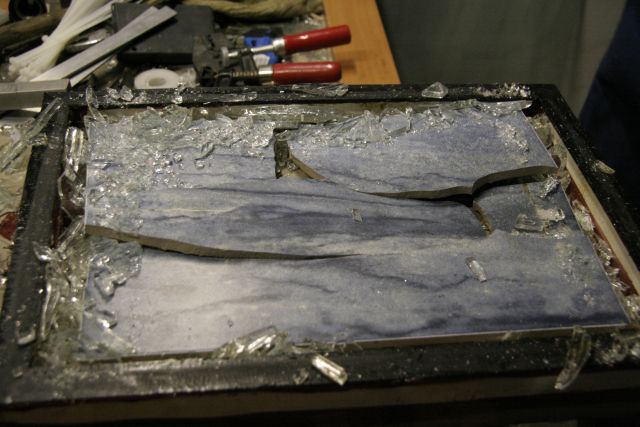
This is the ceramic tile. We thought only one crack was happen. It seems more was on the scene.
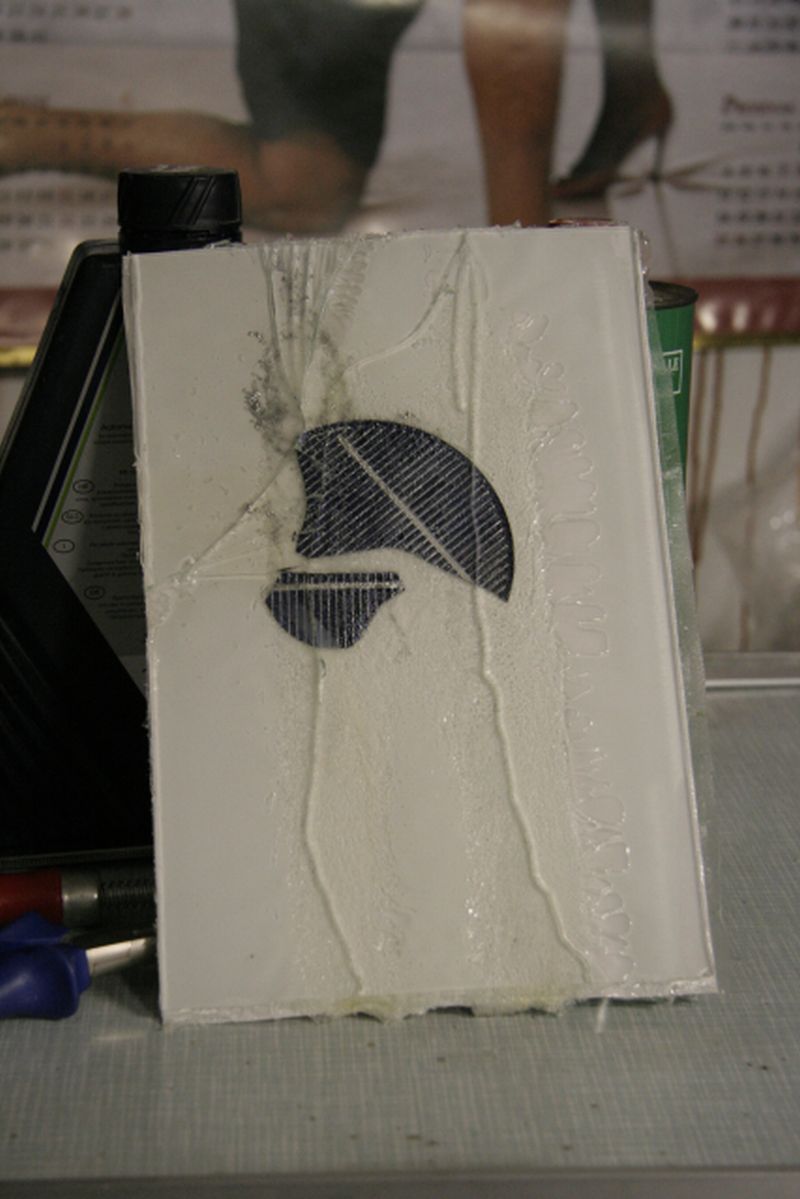
This is other (true) side of the laminate. It can be seen that wacuum even pulled the tin from the cell (two pieces of broken cell). It seems that temperature was too high. Also, we can see too much cured EVA film above the heater. They just were too close.
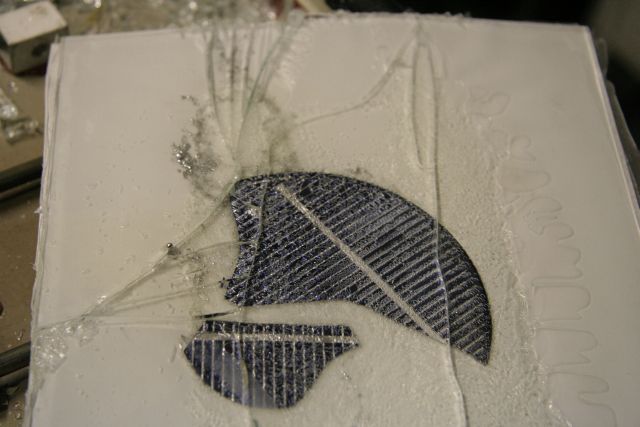
On the right, near the edges is visible how good it was laminated. Unfortunately, as the glass breaks, air comes between the laminates and spoiled the thing.
But we stated it was sucess. We're alive, and it seems things are working this way.
Tomorrow we'll try one more laminating process, with opposite layers.
Hard work to achieve industrial-type solar panels. But worthy. No condensation issues, no back-sheet troubles....
I'll continue as fast as we get other results.