This is pretty plain ,I wanted to make a small genny about 50 to 70 watts for my brothers camper. not sure if this will do the trick but here's what I have so far.
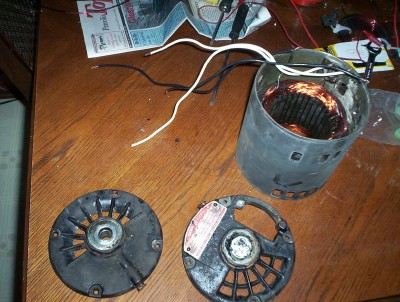
Then I pushed the shaft out of the centre & a 1" square pipe fit over it perfectly.
I then put 2 1X2X1/2" neos on top of each other on all 4 sides this just barely fit
in the centre , I wish I had left it like this or bought 1/2" thick steel flat stock
ubnder the mags but instead I had 4 ceramic mags around so I put them under the neo's in the end but they were thinner so there is a good 1/8" plus clearance now.
This is the shaft with mags installed
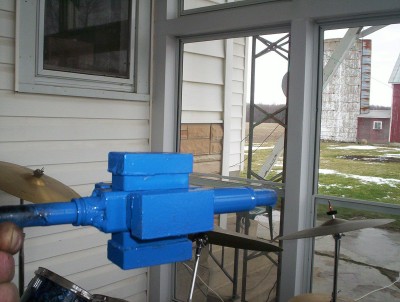
I used the "stock coils" & rectified each with a bridge rectifier then put the 2 rectifiers in paralell. here are the stock windings
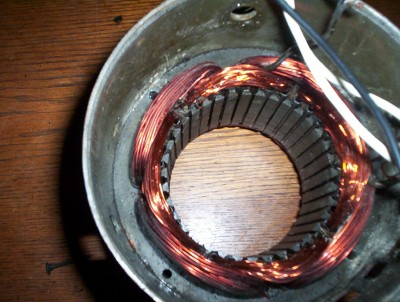
Then I tested it on my drill press
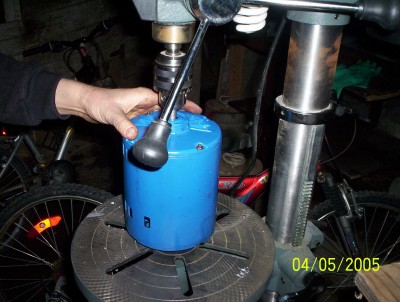
I got 16 volts (open)at 210 rpm
this gave me 7.6 watts or .64 amps into my battery at 12 volts
at 280 I got 22 volts (open)
which gave me 26 watts or 2.2 amps into my bank at 12 volts
the numbers seem to drop after that on my drill press when I go higher, I am guessing the higher gear ratio kills it.
I did try it at 800 rpm open & got 48 volts I think as it shook the wires out of the
volt meter (motor was off centre in the chuck-at 800 rpm it really shakes!)
I also have 8 180 volt 1/2 hp dc pmg motors the figures on it are as follows
- rpm , 41 watts into the battery bank
- rpm , 66.7 watts into the bank
again when I move the belts to a higher ratio the output drops (need to get my lathe home.....)
Devo