I am still machining parts. I finished up the shaft, housing and support plates. All the parts pretty much fell in line with the initial design that I showed on my last post. On the shaft I used a 7/8's dia. piece of 303 stainless steel. I attached an aluminum hub to drive the rotor plates. I included a picture below.
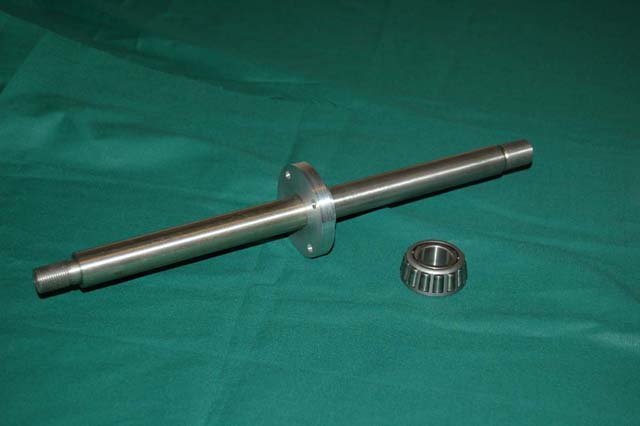
I decided to use tapered roller bearings so that the windmill could take a thrust load. I machined the housing and press fit the race for the bearings to ride on.
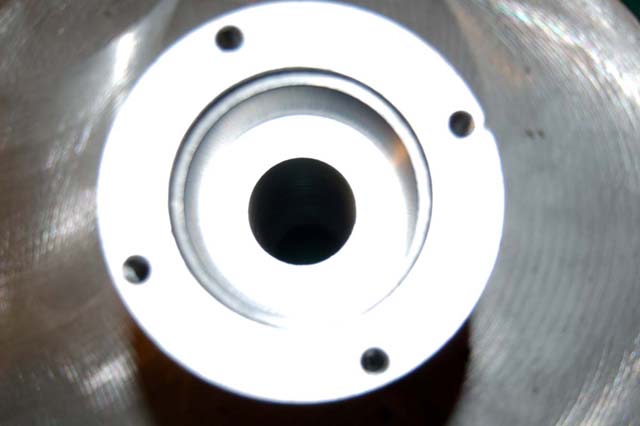
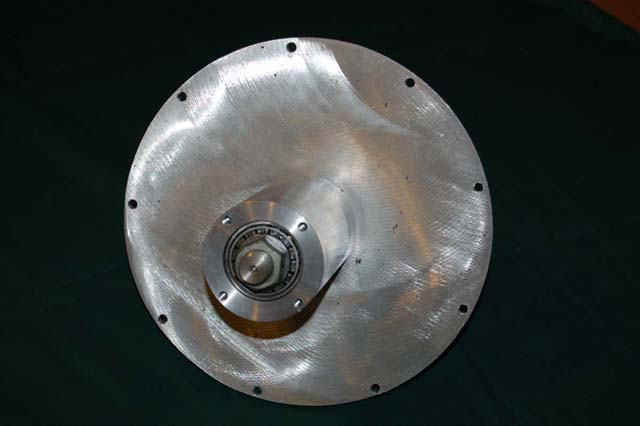
Since the tapered roller bearings are not sealed bearings, I designed a way for a seal to fit in the support plate and work with the hub to form a seal. The hub on the shaft fits into the seal on the support plate. This works quite well and has minimal impact on the torque of the shaft. I am working on an idea for the other end of the housing. I have a new thought on a furling system that I am currently designing.
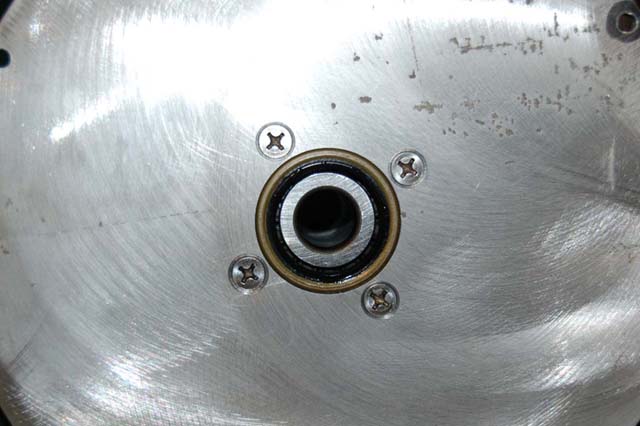
Below is a picture of the assembled unit. It looks very promising and I think it will hold up quite well in the long run. I chose aluminum and stainless steel due to their non corrosive properties and to keep the weight down.
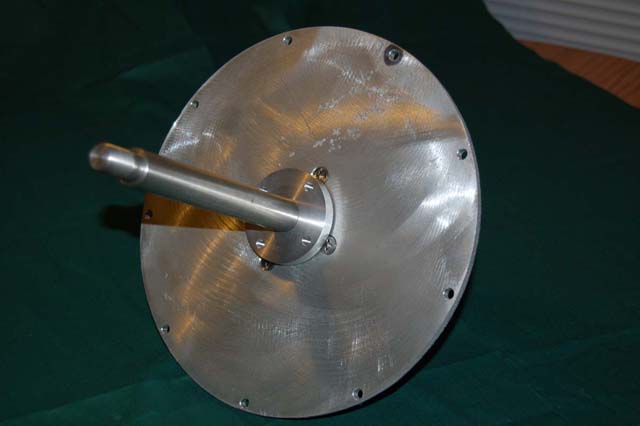
The next step is the rotor plates and mounting the magnets. I will have to also make a spacer and the threaded rods to assemble the plates.
Thats all for this week