I finally managed to collect all the electrical parts, and began building the assembly. Below is the layout. Since I had a good piece of heatsink, I decided to use it for the lay out as well.
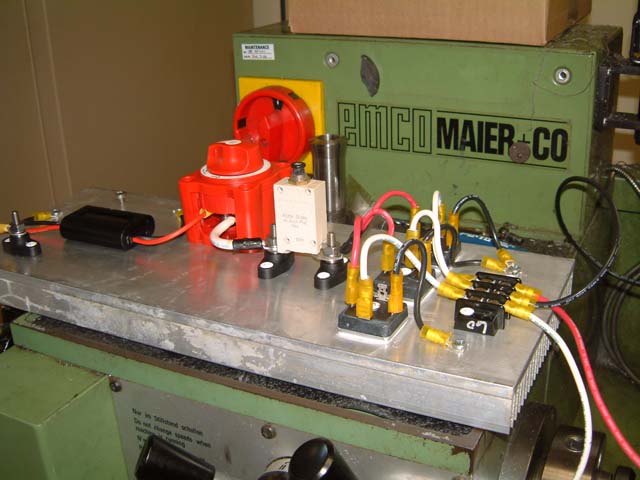
I decided to go with a 24 volt system based on the cut in rpm from the open voltage test I preformed earlier.
I connected two deep cycle batteries together to act as the load.
At 190 RPM's I didn't see any amps on the meter. On the DC side of the rectifier, it was about 23 volts.
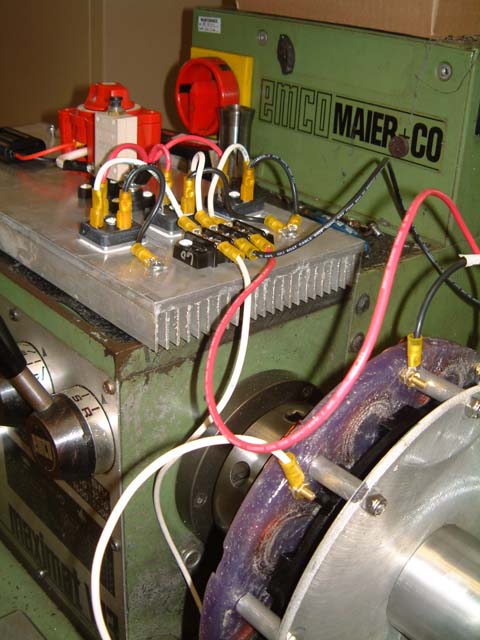
When I went up to 260 RPM's, things began to happen. The thing is, I had 21.1 volts on the AC side and 27.2 on the DC side? Of course on the AC side it was across two phases that I was doing the checking. I thought you would loose some voltage when you rectified AC to DC. I don't know if being in a star versus a delta has anything to do with it either. It is wired in star.
I also based the watts on the DC side. I had the amp meter on that side.
I also grabbed the mount to see how much force was against the stop. I had a difficult time at the low speed keeping it off the stop. Tremendous torque! at the higher rpm almost impossible to hold by hand!
Any way I also took thermal readings of the stator as well.
Started with lowest RPM and then progressed to higher until I got nervous and smelled fiberglass cooking.
Here are the test parameters. I ran each rpm for 5 minutes to stabilize the temp reading. I checked different places on the stator but decided to use one specific coil to take the temp reading.
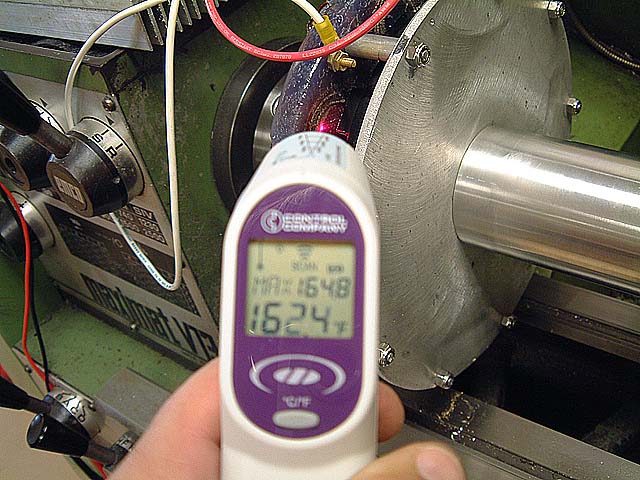
- RPM-no amps, no load
- RPM-(AC volts 21.1)( DC volts 27.2)( Amps 5)( Watts 136) Temp on stator 123.2 F.
- RPM-(AC volts 22.7)( DC volts 29.1)( Amps 9)( Watts 262) Temp on stator 134.6 F.
- RPM-(AC volts 25.4)( DC volts 32.0)( Amps 19)( Watts 609) Temp on stator 212.3 F.
- RPM-(AC volts 26.4)( DC volts 33.2)( Amps 25)( Watts 830) Temp on stator 235.0 F.
It looks like it is preforming pretty good. It looks like a rpm power range between 200-450 rpm. I guess when it is up, I can adjust the furl by the amp reading now that I know what is too hot ( about 20 amps at 24 volts.)
I also checked the temperature on the magnets. I'm not sure how much temp. they can take.
I got finished with the test and recorded a reading of 165 degrees F on the magnets.
I am also thinking about the size of the blades. I Should try to find a size that matches the genny.
Now that I have an idea how much power it will put out, I can move on to the mount and finish the rest of the project.
That's all for now.