I finally got around to making some foam ribs on the cnc router. These are for a large blade, 2 meters long, with a TSR of 7. The ribs were cut from PVC foam supplied by a fellow windmill builder, Trev. Trev, the local fibreglass guru, will use these ribs to make a plug for a fibreglass mould.
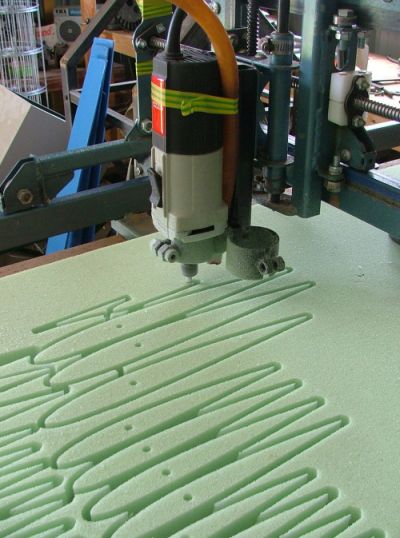
The full story is here
http://www.thebackshed.com/windmill/FORUM1/forum_posts.asp?TID=547&PN=1.
I used the Warlock calculator to work out the blades chords and angles, though I needed to doctor the figures slightly. The longest rib is 300mm long, though the calculator was asking for ribs 500mm long close to the hub, not really practical.
The ribs took about 2 hours to CAD up, and a further 1 hour to cut out. They all have a 6mm hole to slide over a length of 6mm rod, hopefully this will make assembly a lot easier. If this works I'll make a smalled set for a 1.2 meter long blade to suit the F&P motors.
Glenn