Part2
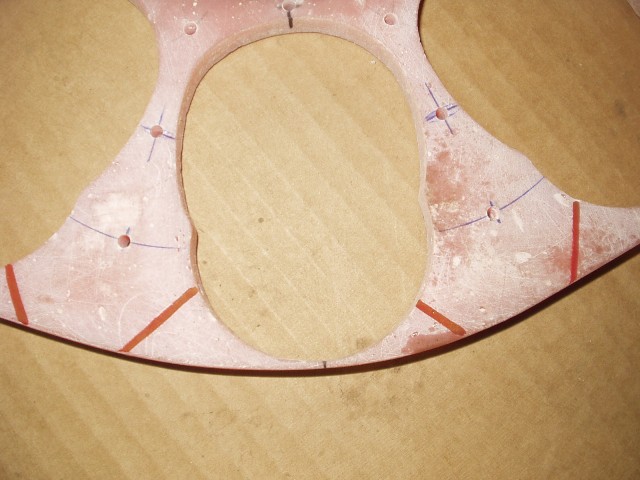
I drilled a series of holes for lacing the coils into the stator and also 2 holes at the end of each coil position to allow exits for the coil ends
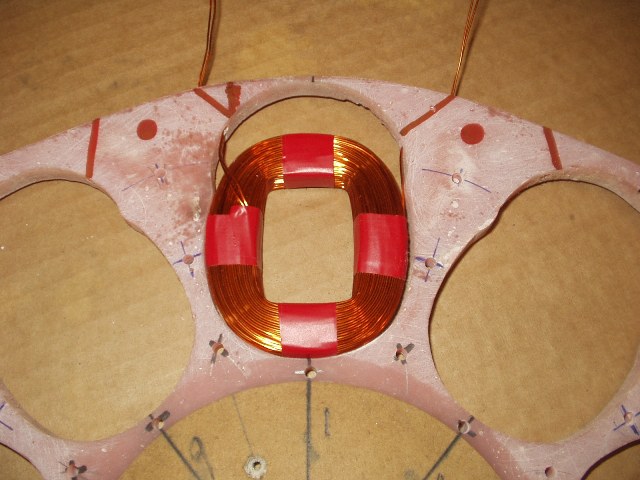
The coils fit nicely in the stator. At this point my intention is to tie/lace the coils in place and epoxy them on the sides and at the bottom but to leave the tops with the tails exposed to improve the cooling.
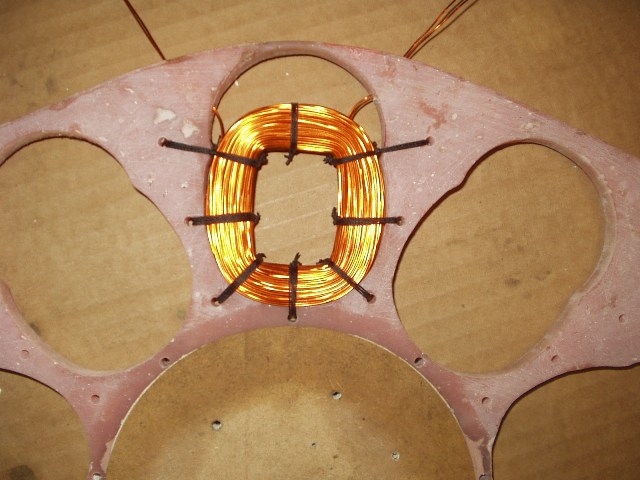
Fist coil fitted and laced in position, each lacing is done in a figure of eight fashion and is surprisingly strong and very secure. The lacing cord is a cotton polly-something! Mix it is very strong, a single strand is under 1mm dia and will easily support my weight of about 12 stone. I tried various types of cord as I was worried as to how they would react to heat. Cable ties would have been the quickest but on a hot wire test they failed miserably but this cord held up very well. So well in fact that I am going to omit the epoxy from the coils completely on this experimental stator. This could prove to be its downfall! Time will tell
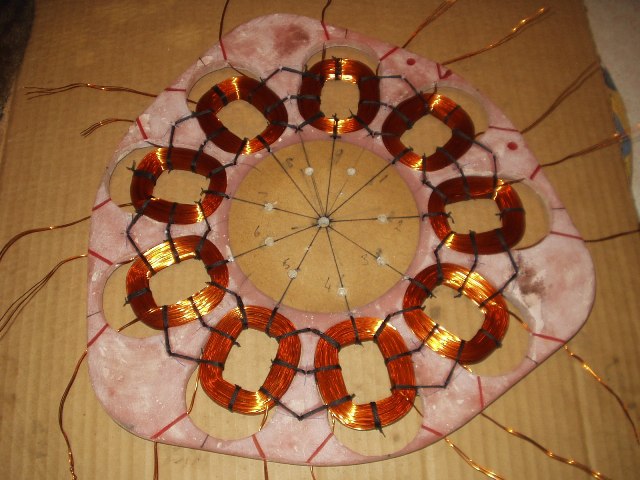
The lacing was the longest part of the job and proved to be very hard on the hands and eyes, but I persevered finally got them all done. The trick was to use a large sewing needle, and a plentiful supply of cold beer!
The whole stator is very stiff and strong, This might just work! I intend to give this a couple of heavy coats of paint to seal everything and glue the windings together.
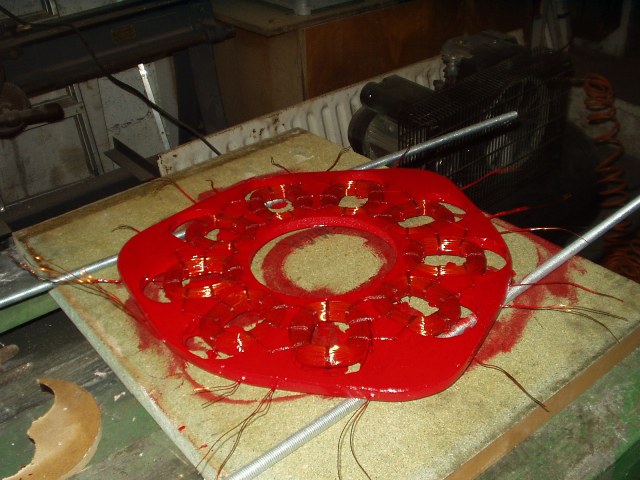
First coat of paint complete. The coil tails will be soldered and clipped to the outside of the stator and terminated in 8mm brass bolts as per normal.
So that's about it, just need a calm day to drop the tower and fit it.
Start to finish is two days with 90% of the work on day two lacing the coils I thought I was never going to get them done.
As always all comments are welcome. Im sure Im not the first to try this approach, there is certainly more work doing it this way and it is probably not worth the extra effort on this size of machine (10ft) but as I said earlier I intend to use this method on the next one but with Tufnol as the stator material.
I would be interested to hear opinions on Tufnol,, as far as I know the only snag is the cut/machined ends need to be sealed to weatherproof it and of coarse the price, it certainly isn't cheap.
I hope this is of some interest to you all!
Russell