Hello RE group,
This is the progress so far on my Low wind genny using a Leeson DC motor I recently bought. It is rated 180vdc / 1800rpm / 4.5 amp (weighs 40lbs). The 12 volt cut-in is about 135rpm. There was some discussion about here:
http://www.fieldlines.com/story/2007/12/19/35449/016
Of course we all know that homebrew brushless alternators are much better for many reasons, but this low rpm motor might be a good alternative to a high rpm small 4 foot diameter PM motor windmill. Of course I love ALL windmills they are ALL good!
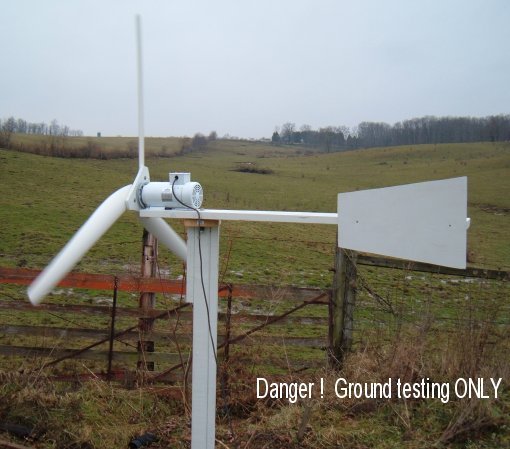
These are the first PVC blades I have ever made. I made them like Ben's at Gotwind.org. They are alittle different since the leading edge is actually the curved side of the blade instead of the straight side. So these blades turn Counter clockwise-- which is the correct direction for this particular DC brush motor.
Jigsaw goes thru it like hot butter. Very Quick and easy especially after you make the cardboard template. These blades are made from the 6" pvc pipe. I actually have enough from one 10 foot long pipe to make SIX SETS of pvc blades! So thats plenty extra for experimenting with different shapes. They are quick and easy and look very good, but I am suspecting they have more drag (slower) than a good set of wood blades.
The over-all diameter of the rotor blades is alittle less than 7 feet. It is 6 feet and 9 inches.
I had thought that 7' was probably too much , but now after seeing that each blade is only 1.5 lb and the weight of the entire blade rotor (including 3/4" treated plywood hub) is less than 6 lb, I thought it would be safe to go alittle bigger rotor, and then cut it down if I decided to later. I think it is fine for now as is.
Plus, I intend to probably furl early to limit the AMP output for this motor to less than 8 amps or so. But as of yet, I havent seen it go this high yet. There has been no real big winds yet hit it.
I made it in only about 6 working hours, plus a couple more hours today since I trimmed about 3/4" of the top widest part of the blades to get alittle less drag and some more speed. It did helped. All the photos are before I made this change. The blades now look alittle thinner than in the photo below near the widest part of the blade.
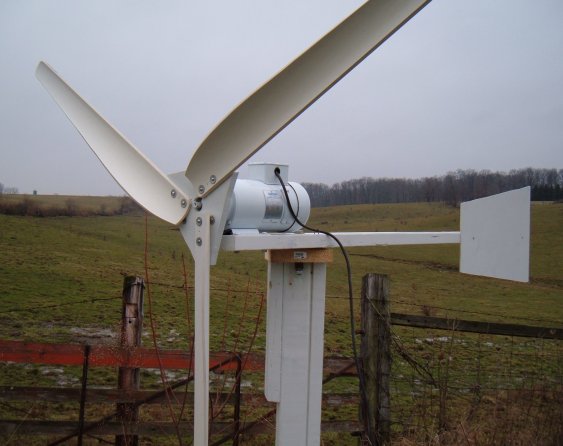
It is at ground level ONLY for testing. As soon as I get things adaquate, I will put it up on a higher pole, hopefully with alittle less turbulance.
I do not have the furling system on it yet, but it absolutely will have FURLING soon. It is a MUST to have a good furling system with the extreme wind gusts now.
I may make a set of faster blades for this mill and furl very EARLY to keep it under control.
I certainly have ALOT to learn about everything. Please keep that in mind-- I am not that experienced yet. But I like experimenting and trying New and different things even though they may not work out so well sometimes.
I put silicon caulk on the back side to keep water out of the back bearing. And put some grease in the front 'soft' seal and the back.
Then I spray painted the motor white.
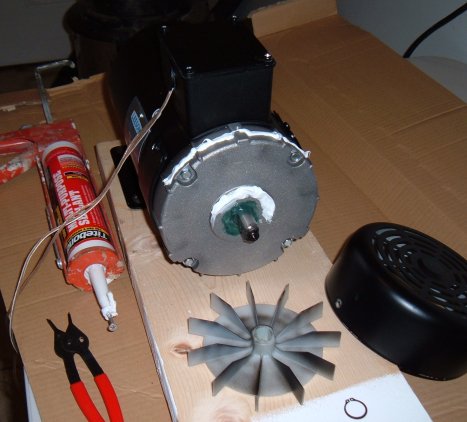
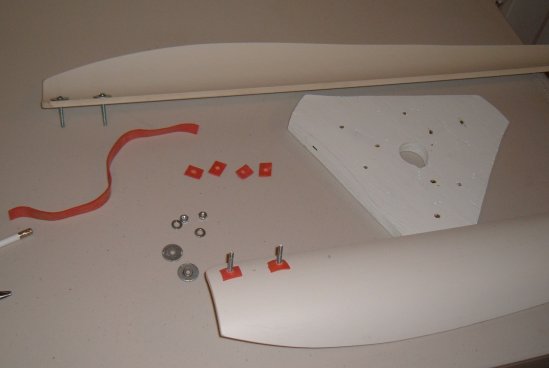
Heres an interesting experiment: I put some rubber band pieces behind the blade mounting bolts to see it the blades might all twist back alittle to a better angle for more speed once it gets going. You can twist the blade back fairly easy with your hand. I don't know if it helps any yet, but it isn't vibrating or anything, so who knows.
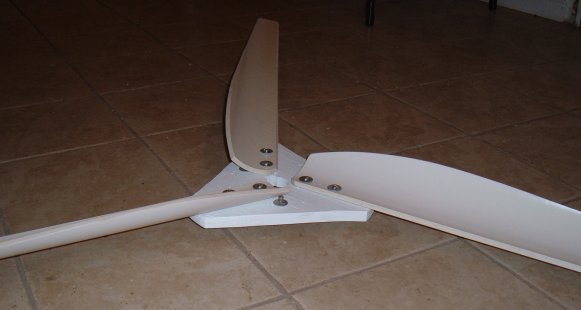
Heres a pretty good shot of the blade angles. When I first started, the angle at the tips was about 10 degrees and the max angle near the thickest part of the blade was probably about 25 degrees! (That is, from the upper part of the arc to the lower part of the arc)
In the photo though, the tips are about 8 degrees and with the newly trimmed blades the maximum thickness of the blade is probably about 20 degrees. Is that bad??
Yes, in the photo you can see why I had to trim some off the thicker part. I didn't need it to be such a steep angle. Even the thinner blades (not shown) still EASILY get over the cogging of the motor in a tiny 5mph breeze. It is almost always turning at least 60rpm.
The swept area of the blades is THREE TIMES that of a 4 foot mill. Of course it is more noticable since it is bigger and the motor is heavier, but all in all I am VERY pleased with the initial performance. It is MUCH better in lower winds than my 4' treadmill windmill at 23 ft up. The small mill is not even turning at all when this bigger pvc hawt at ground level IS consistently charging my battery. (even a small amount adds up for my small 12v system)
I am using only 18ga wire for the testing though. Still need to get much bigger wire.
It usually is doing just 1-2 amps in fairly low winds. I have seen 4 and 5 amps in a better bigger wind a few times, but this is at GROUND level a few feet from the corner of my house. It is very turbulant location as I'm now learning. I've only begun testing the thinner blades a few hours ago. I will know better when I put it alittle higher in the air.
From my ground testing so far, it seems to be at least TWICE as good as my 4' small mill in Watthours into my batterys. Truthfully, I had hoped it was going to be even better than that. I will know even better over a week of testing. Anyway , I am very happy with it so far. It is much more CONSISTENT in lower winds. I live in a horribly LOW wind are (8mph average) AND I have a very small battery bank. So I need to try my best to re-charge what little I use each and EVERY DAY. (unlike folks with a serious batt bank)
I do have one basic question for the group about blade angles:
The tips of the blades are at 7 or 8 degree angle and so are obviously going to have some lift--- but does the middle part of the blades ever get any LIFT since thay are obviously at much steeper angles like 12, 15, and even 20 degree angles???
If its TOO complex a matter to explain then don't bother-- I will understand it one fine day like everyone else.
Any comments, knowledge, questions, pvc suggestions, or concerns, greatly appreciated friends!!
We all learn.