Hi
The system is working well: today dumping lots of power overboard, as some successful changes are making the mill produce even more power than before. But first I'll give some context:
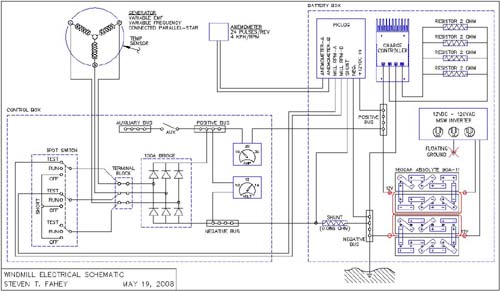
Here's the lay of the land, as of last week. This is about as good as it will get with the current 12V scheme. I'm getting greedy and I've also checked every possible angle - there's no reason not to convert the whole system to 24V, now. It's been obvious that with a motor conversion, high voltage should be the order of the day, but I've also been frugal and slow, to avoid buying into something that boxes me in later.
One necessary step, was to get playing in the "big leagues" with the rectifier block. A very kind soul let me have one rated at 100 Amps, including this fantastic heat sink:
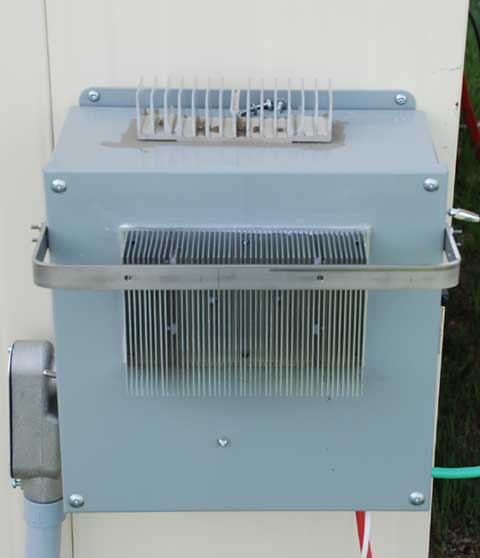
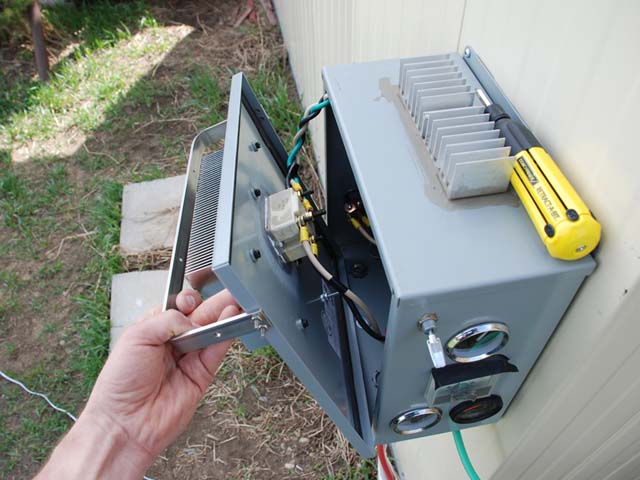
The small heat sink on top was used for the little 4-prong rectifiers. The new one on the front cover required some protection, so I put on this nice "handle".
I lowered the tower in May to make Parallel stator connections. It's now connected in Parallel Star and producing lots of power; here's my diagram of how the different connections work:
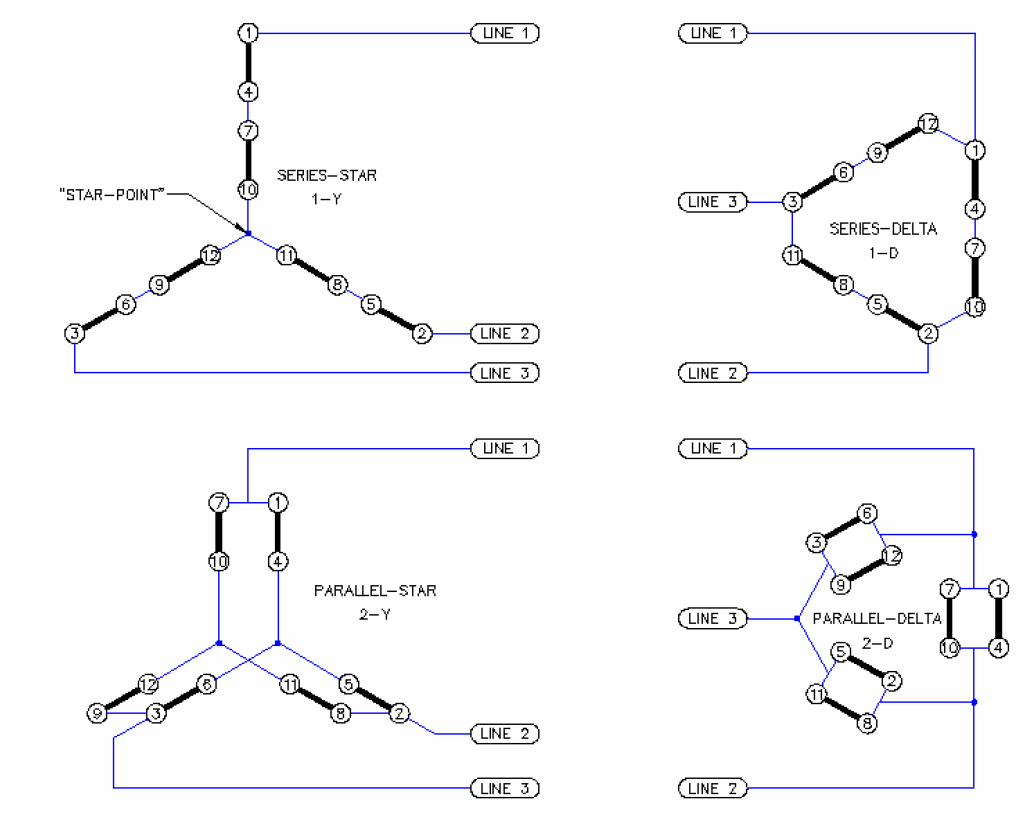
In fact I have had some 2 kWhr days recently, which is 1/5 of my typical 10 kWhr summer day consumption. The possibility of offsetting the house's demand is becoming more realistic!
The only bottleneck that remains is my stubborn use of 12V instead of 24V. Thanks to a fellow board member, I have the SW 4024 inverter ready to hook up and go. Going to 24V will require a re-connection of the generator to get the cut-in speed set properly, but the power curve will rise so much more steeply once this is all done.
The batteries, by the way, are doing well. Earlier in the year I posted with concerns about weak cells, and I devised a plan to "cycle" them deeply a couple of times. This is now done, and after solid wind for several days they're about as "floated out" as AGM batteries can be (fyi AGM batteries shouldn't be equalized).
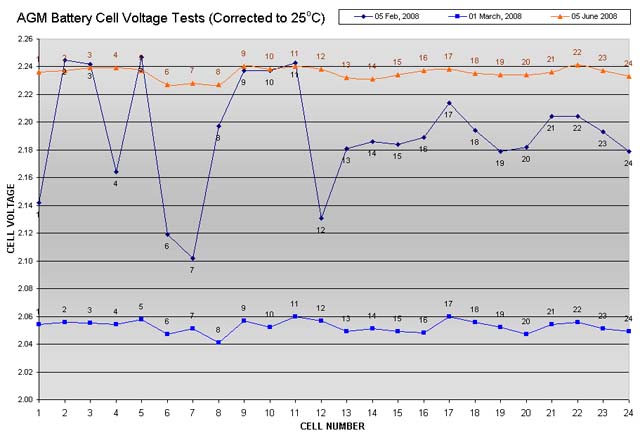
The curve from February was taken at (what I thought was) float voltage, but it turned out the individual cell voltages were all over the place. By draining the batteries (to 10.5V) and bringing them back up again twice, I now have a very consistent set of cell voltages; all within 0.02 v of each other. This particular set of AGM batteries is tolerant of deep discharges, as claimed by the manufacturer. I wouldn't be as eager to do this kind of "reverse equalization" to batteries where numerous deep discharges are not recommended. Also in February I noticed white corrosion starting to accumulate on the lead connector bars. Ever since I cycled the batteries and charged a more balanced set, I've seen no further corrosion. It's like some of the cells were out-gassing while their neighbours still weren't fully charged! Seeing the corrosion stop is a big relief, because I have the charge controller and a few other things mounted in the same box as the batteries. I know, I know, it's not right, but the cable lengths are shorter because of it.
In other news, my Piclog is still giving me funny data. I've rigged up a second (incomplete) motor conversion on my drill press to see if I can reproduce the spotty data. Tweaking the Piclog and immediately running bench tests will speed up the process of gaining trustworthy data. As a side benefit, I may gain data from lots of test runs, and little changes to the motor conversion, too. This will give me a more quantitative understanding of what changes do what to motor conversions, and what to expect when I'm done this one. With all the rewiring stuff going on outside, I don't know how long it will take to accomplish this.

Busy, busy!