On the way to building my second windmill I ran into builders block. I realized my current setup with small sealed ball bearings wasn't enough. I did not want to go the trailer hub route either but I did want to use the same bearings as in the 4" trailer hub. I have spent quite a bit of time over the last year staring at different bits and pieces, trying to put them together into some sort of workable unit.
So, my goal; a setup that requires no plasma cutter, no welder, no lathe and really just needs a few hand tools to build the main assembly, less the alternator. A 6 foot and under mill that either uses stall limiting or no furling. A setup that anyone in the US could copy with a shopping list and few visits to the Ace hardware and building supply stores. Oh, and it also uses the same tapered roller bearings as the 4" trailer hub. I believe the original idea came from something in Ghurd's files so credit where it's due.
Here's the bits.
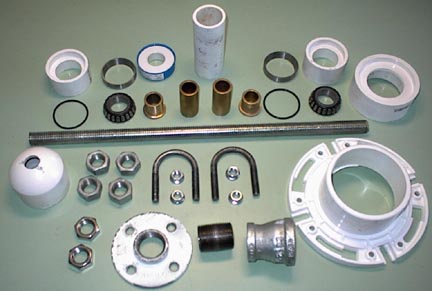
Next,
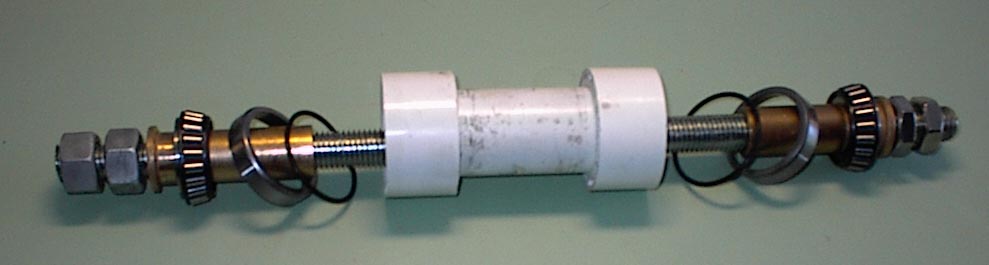
Partially assembled,
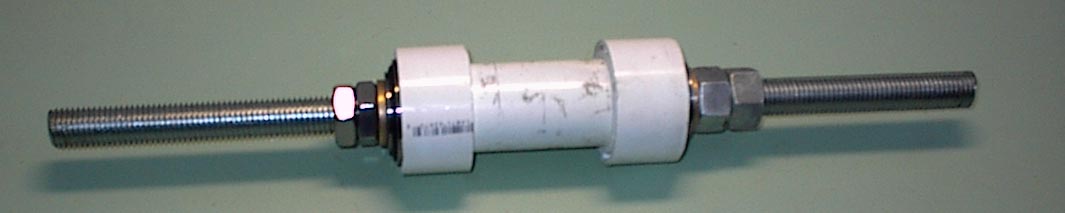
adding the down pipe,
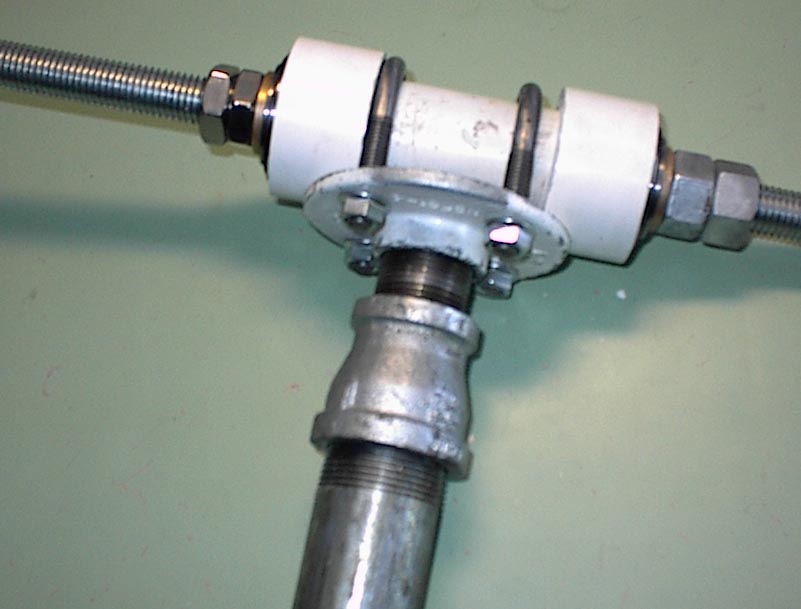
Stator support and front bearing cover,
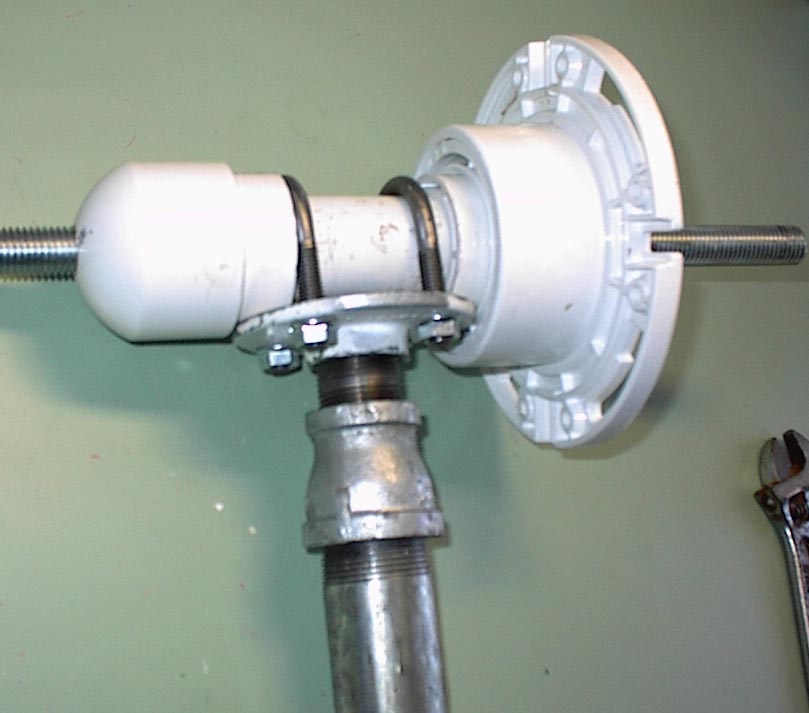
The blade set will go on one end and the alt on the other. Everything is mounted on a 3/4 rod of all thread. The threads are set so that when the prop is turning the shaft the threads will push water out in a corkscrew fashion to protect the front bearing. Also the front bearing cap will have a weep hole at the bottom to drain any water that makes it's way in. The rear bearing will be protected by the stator support (not in the picture. Everything will get a few coats of Rustoleum to protect from rust and the PVC from UV.
Why did I do it all this way? I wanted very much to build a small mill but knew I never would if I needed welder, lathe and the like. Also, I think there are many others that get discouraged from building a small mill and either quit or go the route of looking for treadmill motors and the like because it's easier, even if the results are disappointing.
So there it is. Assembly time from the first picture to the last is about 10 minutes. Shopping time for the bits, a little longer. My six foot wood carved blades are already made and ready to be mounted and the alternator is on my bench just waiting for the stator to be poured before the final assembly. I really hope this is useful to folks with limited tools and I have no doubt it can be improved upon.
Oh and thanks, I couldn't have done it without YOUR help.
(please let my pictures be the size that right clicking says they are)