Well it has taken a while but finally we lowered the duel rotor for a long over due check up, a few flaws were exposed.
The blades are carved from Oak with helicopter tape on the outer 300mm, not enough as it appears.
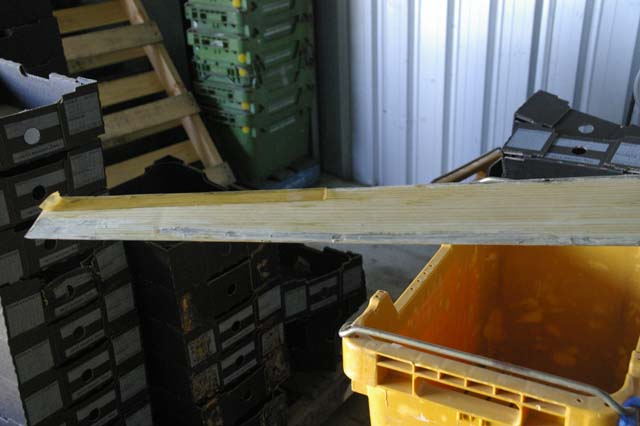
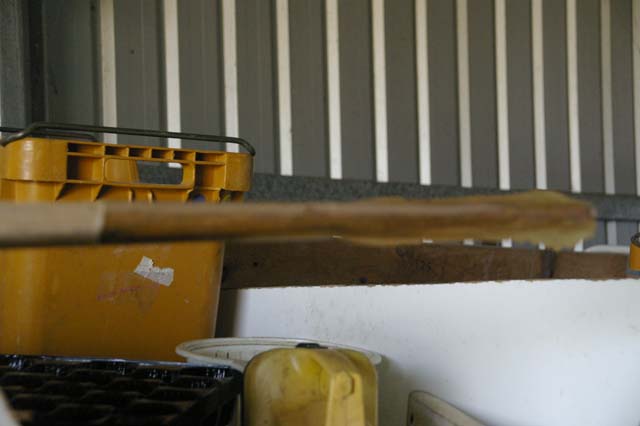
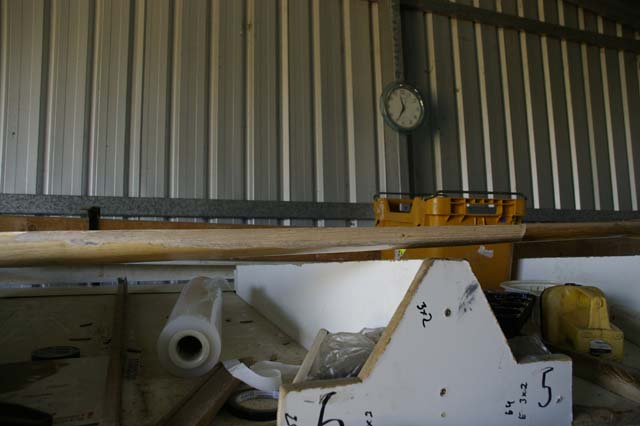
Digging deeper reveals the stator has rubbed, the magnets are separating from the resin, also the magnets have lost some strength, possibly attributed to it's previous rub session.
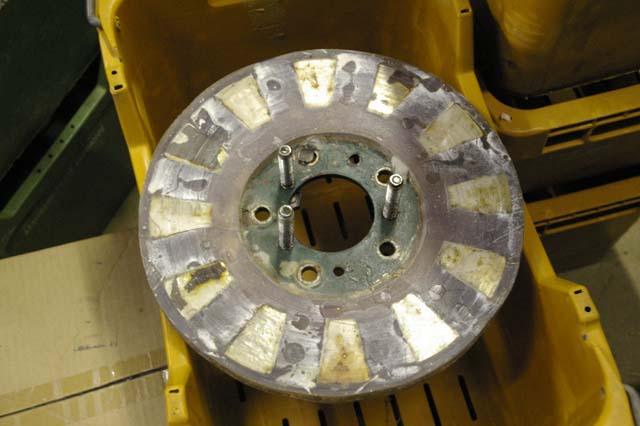
The rear rotor is in better repair,
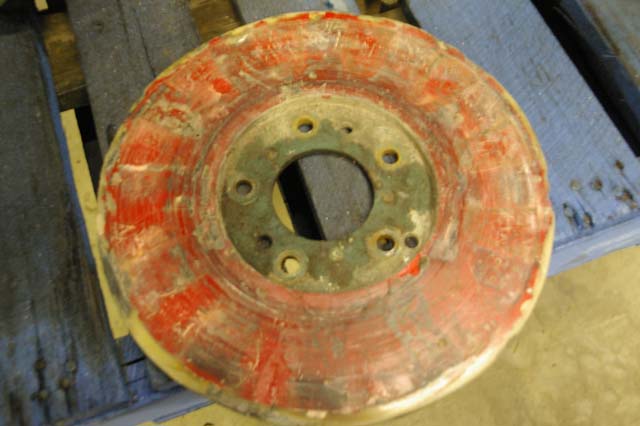
The stator has been rubbed baring some wire, resistance measurements of each coil show most at 1.3 ohm but one at 4.6 ohm, further investigation needed there.
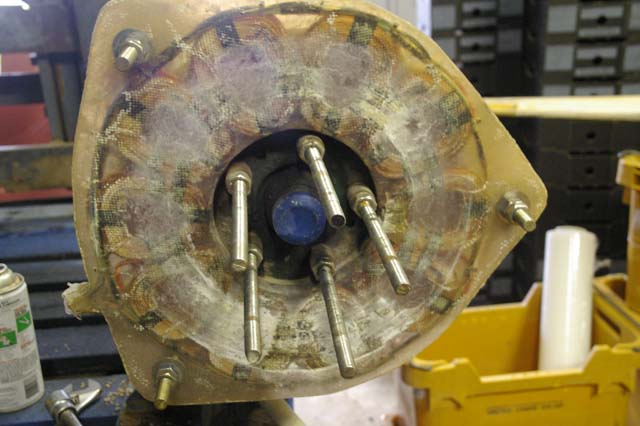
The bearings came up well with no sign of water ingress despite fitting without the seal.
So a rub down, new longer tape and re coat for the blades should fix them, the magnet rotors will not be so easy. In reality it needs a complete new unit but for now I may add a third magnet to the existing stack of two on the front rotor. Seal everything and raise it, with a view to making new rotors with new magnets and a new stator.
The original ripple rotor had two 12v stators, when we converted it to a duel rotor we made a new 24v stator, I'm tempted to fit one of the 12v stators and give it a whirl.
Winter has finally arrived to my part of Australia so very little sun and only two turbines flying, thankfully we have had several days of gale force wind, to keep the batteries charged.
I suspect the rubbing is in part at least caused by flexing of the plate the stub axle is mounted
on allowing the rotors to move independently from the stator, so some reinforcing needed there.
With a new 4 Kw of solar going in soon at our new house site with a tie back down to the packing shed (aproximatly 600m) will take some of the pressure off and allow me to take a few liberties with this one.
allan down under