Hello, I posted a while ago (last week) trying to get some good ideas on how to realistically and efficiently produce a 5 KW alternator. Got some good feedback but I am at the point of wanting to actually start to make something. I have found a design which I believe will be the most efficient to produce (IMHO).
Some background. I have built a hugh piggot style alternator but Im not that impressed with its weight to power ratio. Seems that if a lightweight alternator is made available. That will help get wind power promoted as half the cost associated with a commercial turbine is the tower which needs to be waay oversized to support he 1000 Lb loads of say a bergy excel S (10kw)
Along coem the french with what I believe is a very simply designed and elegant alternator design. I'm sure some of you are familiar with the alxion alternators.
very light weight for the amount of power they can put out and dont seem to display allot of high rpm losses.
This is where I need someones help. I need some rudimentary shapes fabricated out of steel and aluminum, or aluminum alloy. Mostly trying to construct ring shapes for the housing of the stator and the frame for the rotor.
I'll post some pics of the internals of the alternator model Im after.
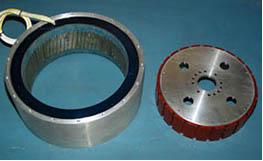
and
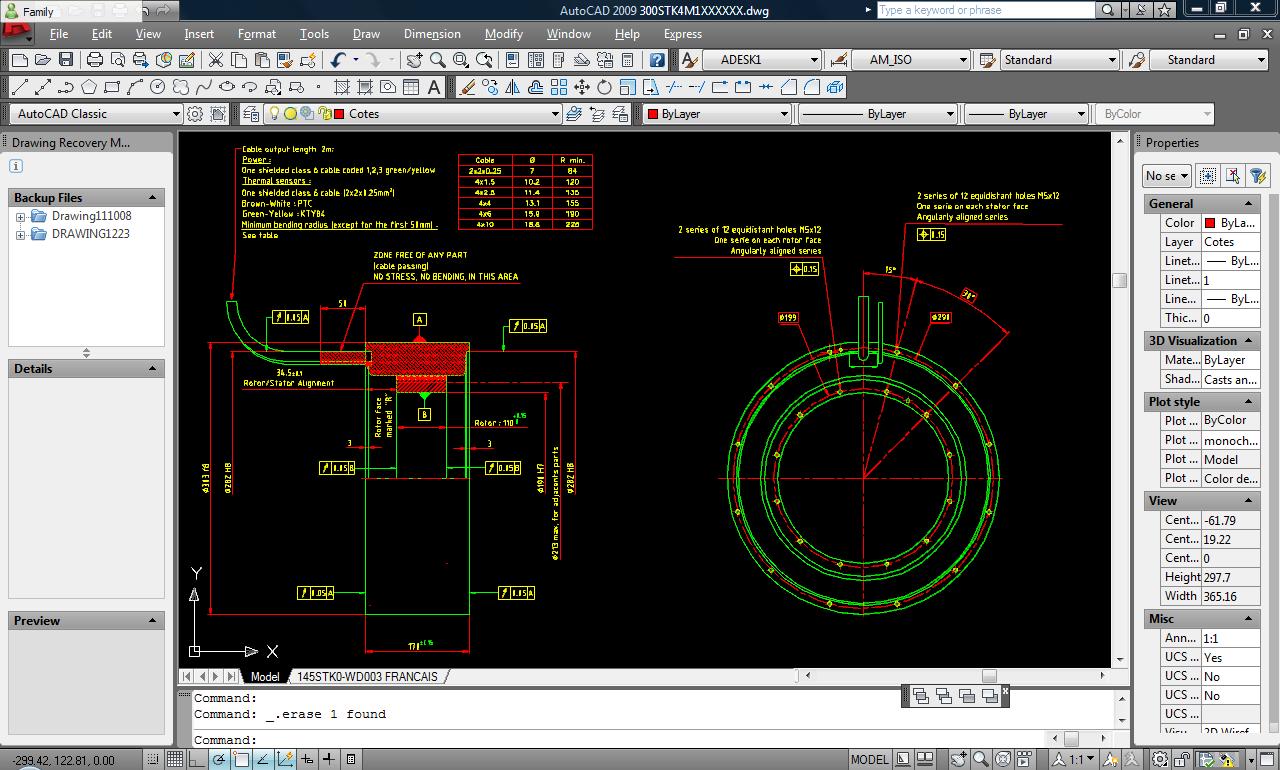
I like the idea of this design as it lends itself to extremely good power to weight ratio, which will help in the overall construction cost as a lighter tower will eventually be needed.
My Fabrication process would be like this.
- Cut Aluminum Housing out of some round AL stock.
- Cut Steel rotor out of some round steel pipe stock.
- Cut stator mount bracket and rotor mount bracket (disks) out of aluminum and machine for bearing shaft and mounting holes (see #9)
- Machine for mounting holes on both housint and rotor.
- Mount magnets to rotor cylinder
- Stator internals(Need help here) My idea is to use not a solid ring for the stator coil holder, but rather a series of steel rectangles that would be placed inside the stator and epoxied of fastened in the housing with enough space for the winding of the coils to the required voltage - way out of my league here so chip in with the obvious configuration.
- wind coils
- epoxy stator
- Buy a standard shaft I attached an image of what it needs to look like.
>

and attach to the rotor and stator housing.
I know some of you will say, who cares about weight, but in the long run a lighter weight alternator will mean more people use them due to the tower requirements alone. Also, They are easier to ship which also means less money.
I have already purchased 24 neomags (1x2x.5) for a 24 pole design, being that the rotor needs to be about 4 inches wide, this will serve for half of what I need, but testing with half should be good enough for now as the other 24 can be added later.
Thoughts? Offers? Suggestions?