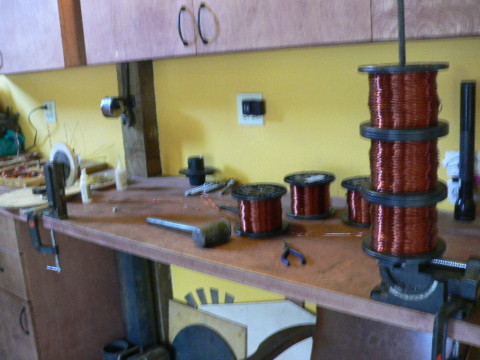
Last Thurs I made a posting about testing the a coil for this machine. The plan is a 20' dia wind turbine and I figured that I needed 45 windings, which I could barely fit with 3 strands of #15 gage wire. Pictured above are three spools of #15 gage wire and the coil winder in the back ground.
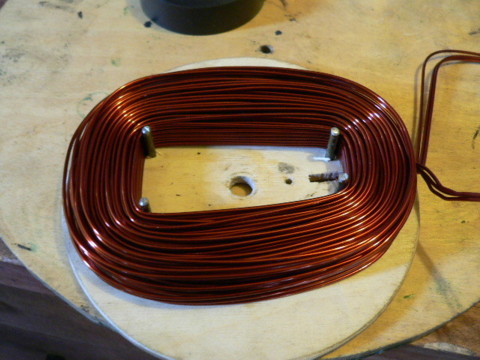
I used the same coil winder I made last year (actually late 2004) for my 17' machine, but I drilled out 4 holes and inserted pins to make the hole in the middle larger. Pictured above is one of the coils for the new machine on the coil winder. The pins on this insert through the front of the coil winder so the coil comes off with the front of the coil winder. Once I take that off I press the coil flat with a dowell and soak super glue into it. The I turn it upside down (the coil falls off) and I put more super glue into the back of it. Then we tape up the legs with some electrical tape.
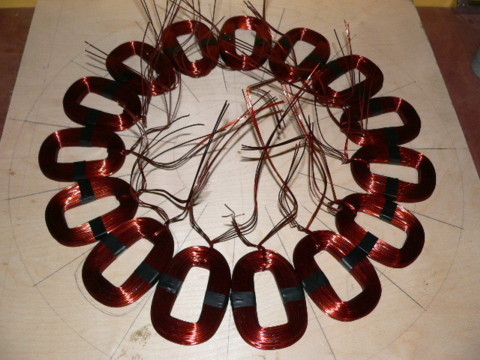
The mold is not finished yet, but the bottom is layed out and the positions in which the coils must lay is marked on what will be the bottom of the mold. These fit about perfectly I think. Again, we have 22" dia magnet rotors, with 20 1.5" x 3" x .75" thick magnets on each one. The overall diameter of the stator is 28" in diameter.
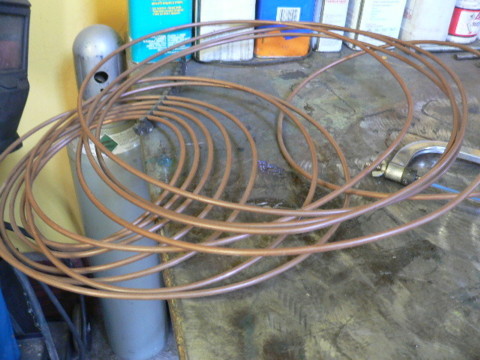
I used this old copper tubing (1/4" I think) that was previously used as the primary coil on an old tesla coil I made as connectors between the coils. It's handy to poke the wires in, crimp them - and solder them.
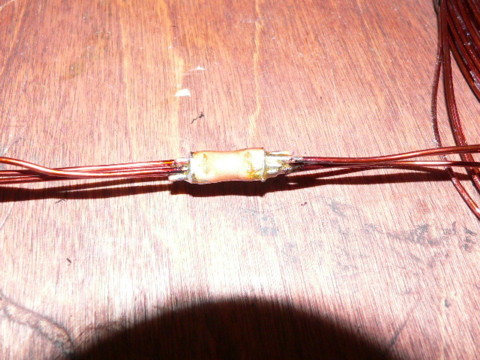
Theres an example. The tubing fits 6 strands (3 from each coil) very nicely and the connections came out very nice. We did something like this last week on Scotts wind turbine but with fewer strands and smaller tubing.
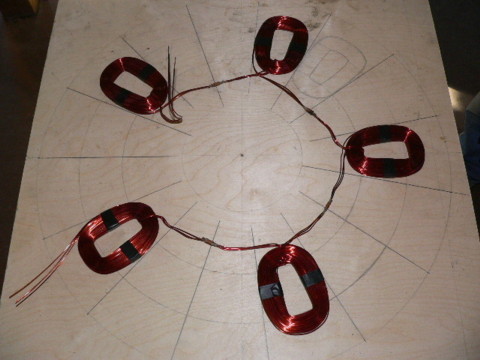
Theres one phase all wired up and sitting on what will be the bottom of the mold.
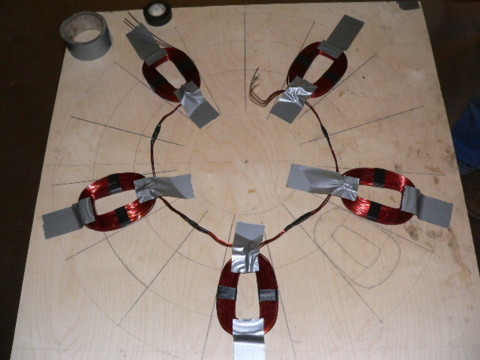
Then we get each coil postioned exactly where it should be, and taped down.. Pictured above is one phase in its postion.
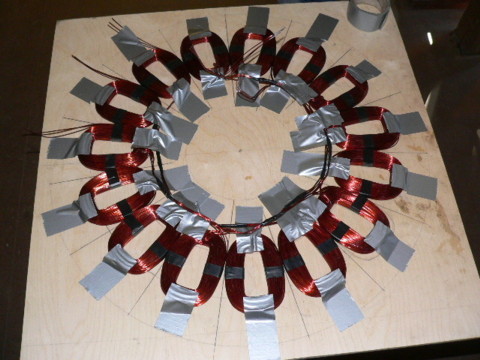
There we have all three phases taped down into postion.
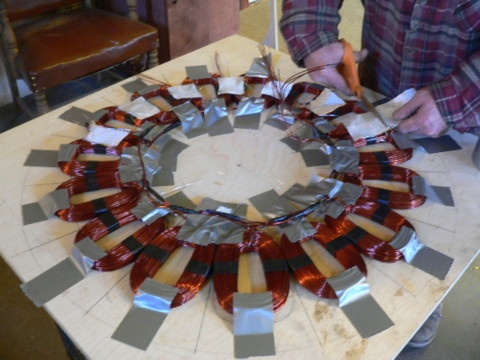
George is cutting out 2" x 2" squares of fiberglass cloth and placing them between the coils. We'll soon glue those there to hold the coils in place so the stay that way before we cast them. (we have to move them around inbetween now and then)
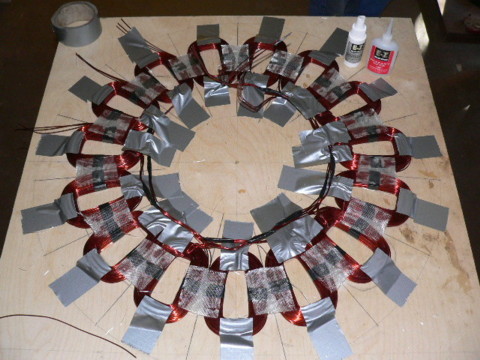
Then we use cyanocrylate glue (superglue) to stick the fiberglass cloth to the coils (we also run lots of it into the cloth inbetween the coils) to make it fairly rigid so we can move the stator around without changing the position of coils or anything.
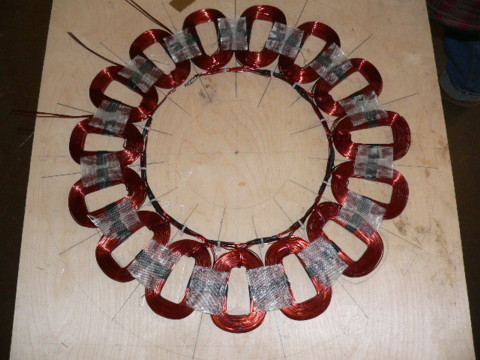
We've removed the duct tape - all the fiberglass is glued down. We've also used 'zip ties' to hold all the wiring together on the inner diameter. At about 11:00 you can see where we made the star connection between the three phases.
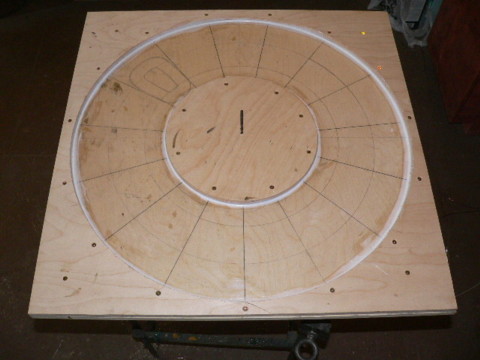
Pictured above the mold is finished. The OD is 28", the island in the middle is 12.5" in diameter. We used caulk around all the edges to smooth things out and make sure no resin can run under the wood. The mold is screwed together with wood screws - we countersunk them all so everything is nice and flush.
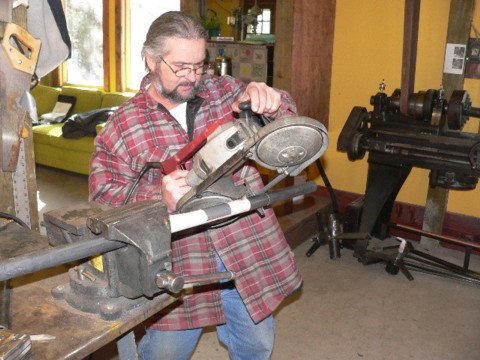
In the mean time - George cut out tail pivots, tail bearings, and yaw bearings for 5 more small (10' diameter) machines.
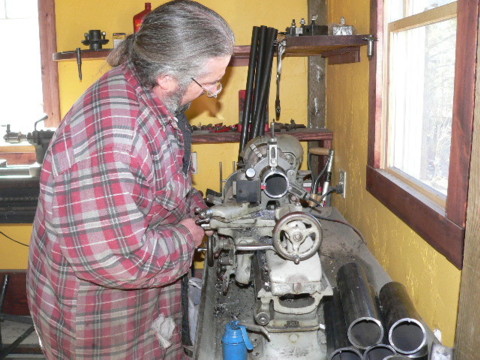
After we cut bits of pipe for windmills we usually face them off in the lathe to the right length, and get make sure things are nice and square.
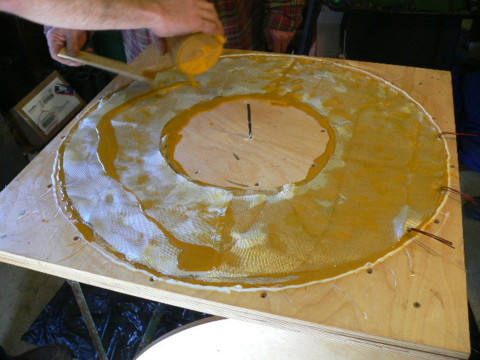
Its always tense for me (stressful)casting stators, especially one this big so lots of pictures did not get taken. Here were at the end of it all just getting ready to put the lid on. This took almost a gallon and a half of polyester resin. We have a thick layer of fiberglass matt on one side, two layers of fiberglass cloth on the other, and lots of fiberglass strips around the outside of it (inside) to give it extra strength hopefully. Everything Ive casted thats 'big' in the past has cracked some - I wanted to give this all the strength I could. We also mixed about half the hardener we normally do because of the volume here.
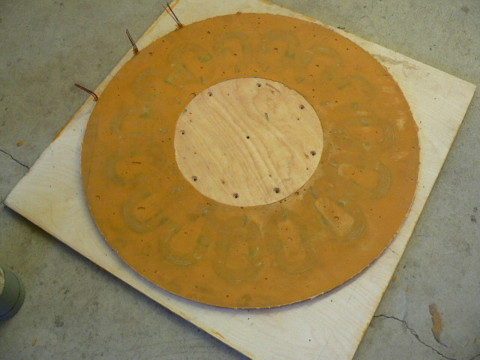
After two hours it had set up mostly and we pulled the lid off the mold. It looked nice, a couple of very small (barely noticable) cracks, but nothing like on other large castings we've done. Once the lid was pulled I let it cool and then tried to remove it from the mold. It did not come easily - I actually had to take all the screws out of the mold and pry things apart to remove the stator. I've never had so much trouble. Maybe just due to the surface area - hard to say. We used 'Crisco' for mold release this time (its worked well in the past) - maybe I should look into something else. The stator wound up cracking (some bits stuck to the mold and broke out of hte stator) - but not too bad, better than Id hoped for.
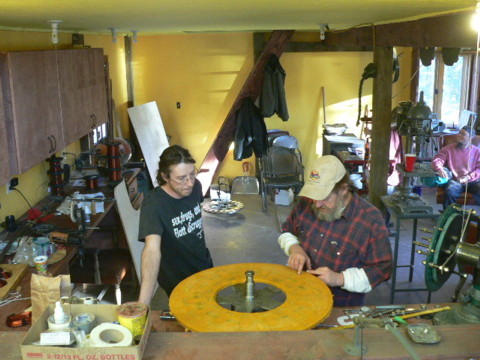
Tom and I discuss the cracks in the stator...
we decide it's no big deal, we'll drill it out, assemble it, and epoxy up the cracks later.
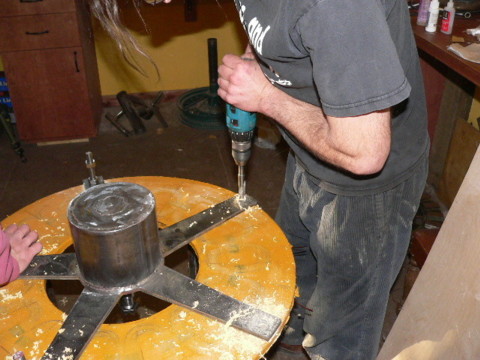
I put the stator down on a stand and put the frame of the alternator over it (spindle poking down through the stator) and drill through the stator with a 5/8" bit for the studs that will mount it to the alternator.
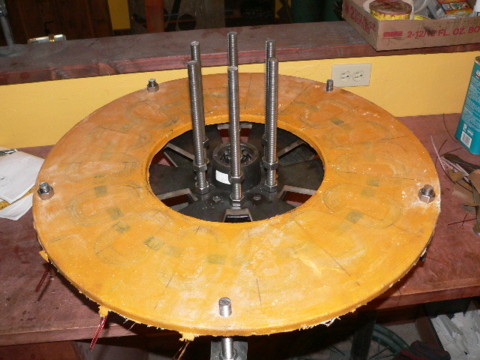
Then we mounted the bottom magnet rotor to the alternator frame, and mount the stator over it.
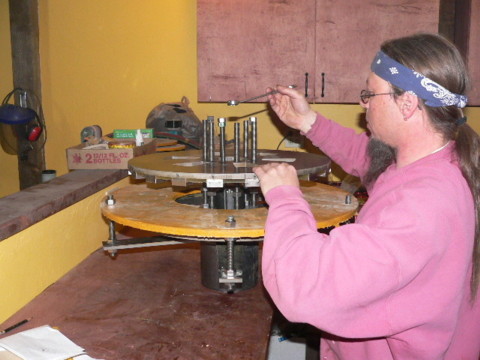
Adam helps to patienly lower the top rotor down with 3 jacking screws. This process takes about an hour. If it gets crooked, it either binds up, or tips over... trick is, 1/2 turn per screw, one screw at a time... lots of patience.
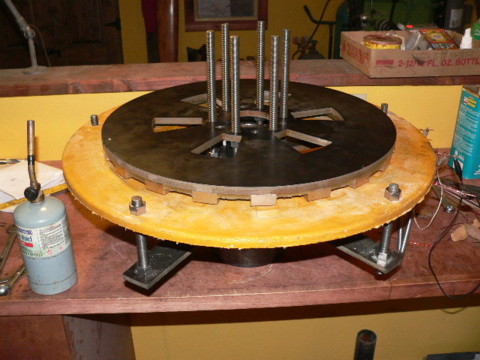
There it is finished (mostly) - we just need to test it (volts/rpm). Then well take it all apart again,finish the metal work, paint it etc..
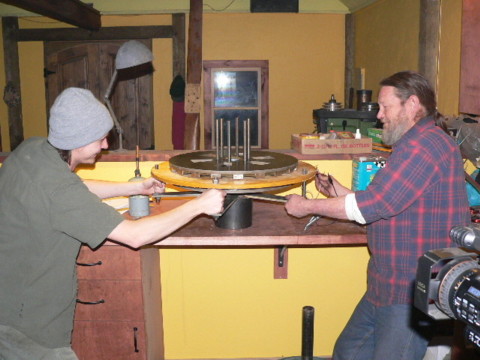
Adam and Tom are amused with it. It is quite amazing how rapidly this stops (its downright violent) if you spin it up and short it out. It's incredibly stiff to turn when shorted out. Past that... we've not tested it tonight but it seems quite impressive.
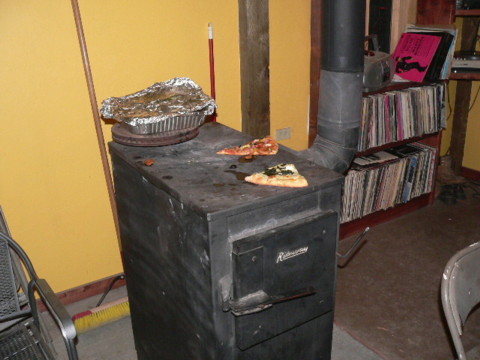
Matt and Daphne brought up pizza as usual. If its not hot enough when it gets here... you can always put it on the riteway for a bit and it's better than new!
Also notice the aluminum container which contains 'buffalo ribs' that George brough up (luch!).
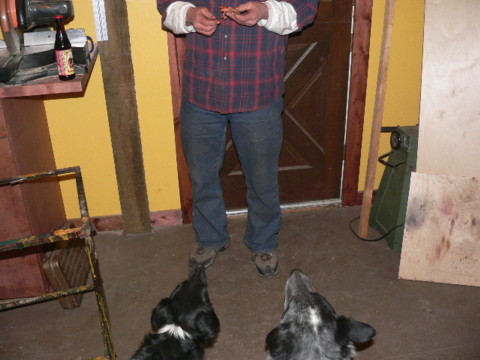
and of course dawgs begged...
One other note about my 17' machine since we fixed it last week (we opened the airgap a bit). Yesterday is was very windy and I saw a 'record' 96 amps from it (I only watched for 10 min so it probably did more) and it was pushing my fairly low batteries up to 64 Volts (not good) because the heaters could not dump enough power. I shut it down... but it is interesting how much better it works in high winds now (too well - probably in stator melting zone if Im not careful) that Ive opened the airgap up and extra .1". Its still fine in low winds, but much too powerful in high winds, it needs to be closed up and the blades really need to stall a bit more in high winds I think.