hello fellas,
fanman here,
im just trying to get this posting done and what a mess, all my pictures were taking in the wrong pixel size and i don't know how to make them smaller, so i went with some finished pictures instead i had to readjust my camera for these, anyway ive made a 120 volt axial flux machine the last couple of weeks its been an alful lot of fun for me.

i made the gen with 1/2" steel plates so there would be no flexing, i used24 magnets per plate. 18 coils of wire each with #14 wire one in hand 110 turns. as ive built this i tried to get all the information possible from the board and use it wisely, so my generater is kind of a mix of alot of things on this board
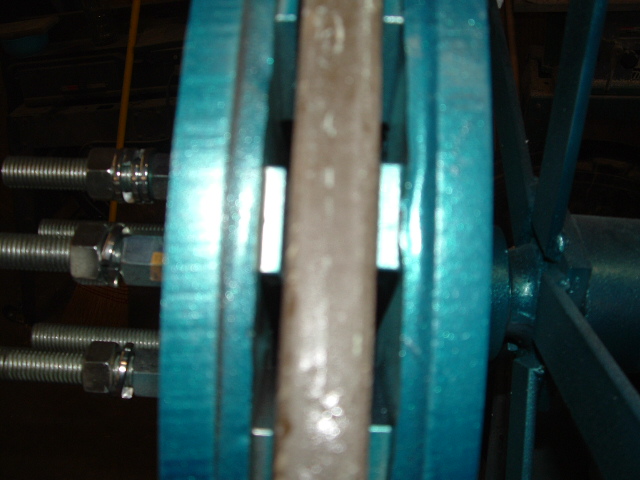
i didnt completly fill the magnet plates with resin because i thought that it would create a little bit of air flow around the coils, and my coil plate is a little thicker than most it is 5/8" thick, i made it that way for one to get the voltage i needed with the wire i had and for two,i will hopefully have a little better efficienties at higher wind speed, hopefully thet will eliminate some of the stall problems people seem to have
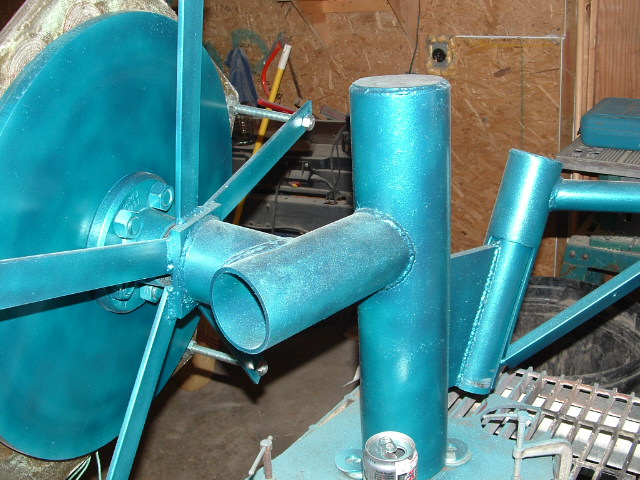
i made the fram from a 4" pipe mainframe and 3" offset fram it is guite tough and hardy, i guess i can say it is overbuilt a bit, but anybody in this type of hobby knows mother nature will always win. hopefully ive eliminated a week framwork, i also as you can see used 3/4" allthread in my hub, instead of 1/2" again for toughness,the hub itself is a 3500# rating so hopefully that is strong enuogh also,
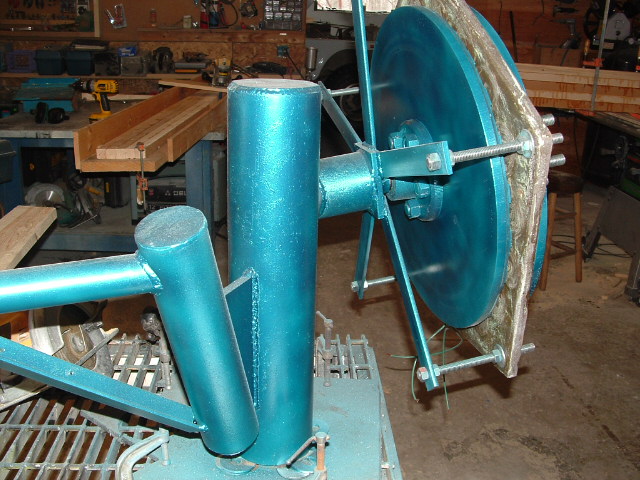
i used all the angle info from hugh manuel on the tail furling part of this machine, the tail is about 72" long, i havent got the tail blade on yet i am working on that.i sure wish i could of used all my other pictures on this gen owell.
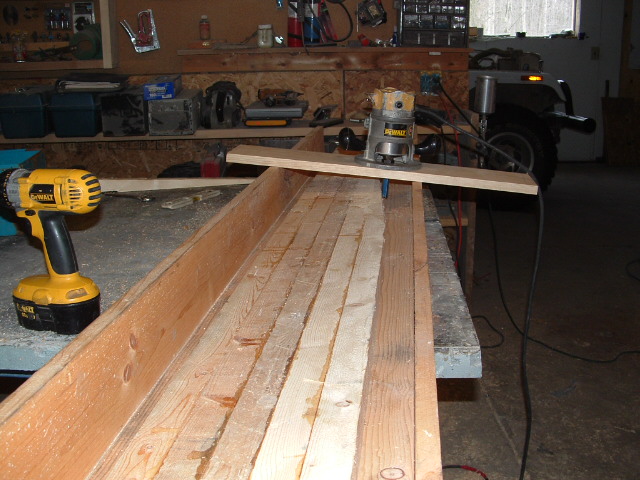
. i also am in the process of building blades for this machine. ive built a handy little jig that i can use to create the blade face, ive made several sets of blades with this jig and it works great, you just place the blank in it and make a plate for your router which rides along the top edges fo the box, if you notice the box has a straight edge on the back, which would be the leading edge of the blade, and the closer edge if you notice has the appropriat angles for the trailing edge of the blade
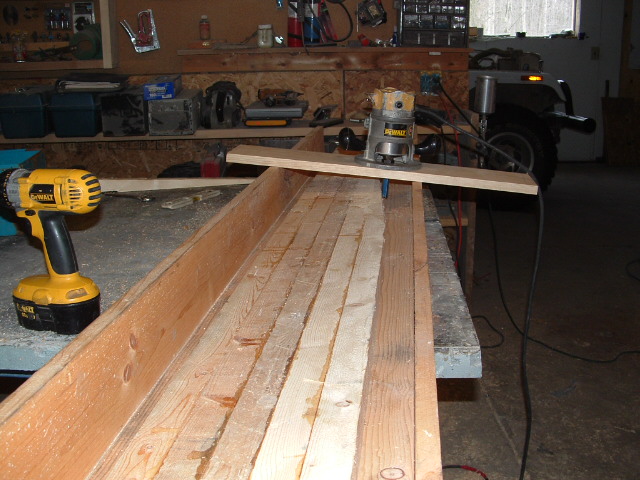
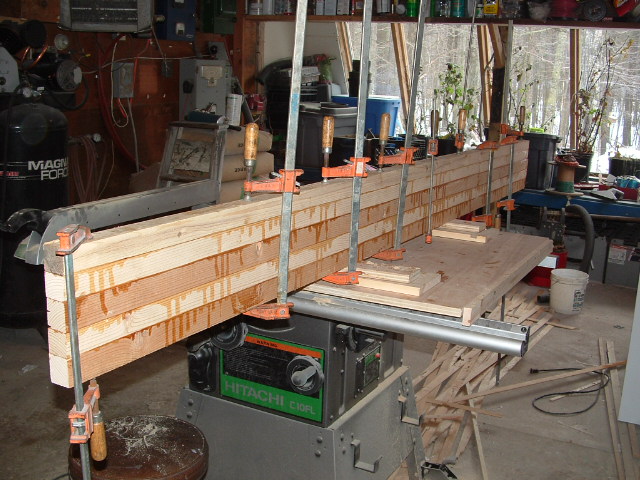
i just looked at the blade box picture and i guess you cant see the trailing edge sorry, anyway im making these blades out of 30 year old pine i got from a remodle job super dry and straight, i laminate it together with epoxy resin and that makes them super strong and water tight. well i hope to have this on a tower in a month or so and see what it will do. it will be a short test tower, i really need to fine tune this before it goes on my permanent tower, which is 158' tall and homemade,i really enjoy building my own things and creating my own power. i would really like to make a much larger machine like a 10kw, so anybody with some helpful ideas, lets talk. thanks all you guys for your input and for making this world a better place. if you notice in the last picture behind the tablesaw there is a whirlwind machine on the floor does anyone have anything good to say about that machine. the tag says its a 5500watt 120volt unit ive heard that there governing system sucked, but its never been put on a tower, i have the sitka blades and all that goes with it, i got it at a sale here in northern mich. what a find eh?