It has been a while since I checked in, though I still read the board every day.
Here are some pictures of what I got done this winter.
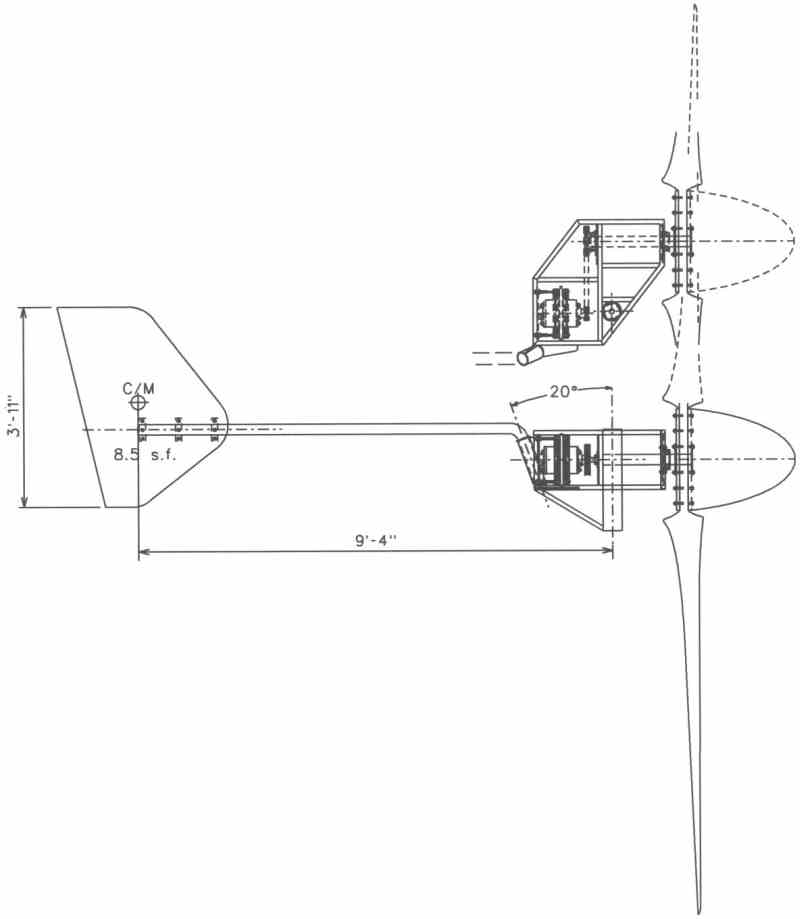
First, I nailed down the finished size of everything...
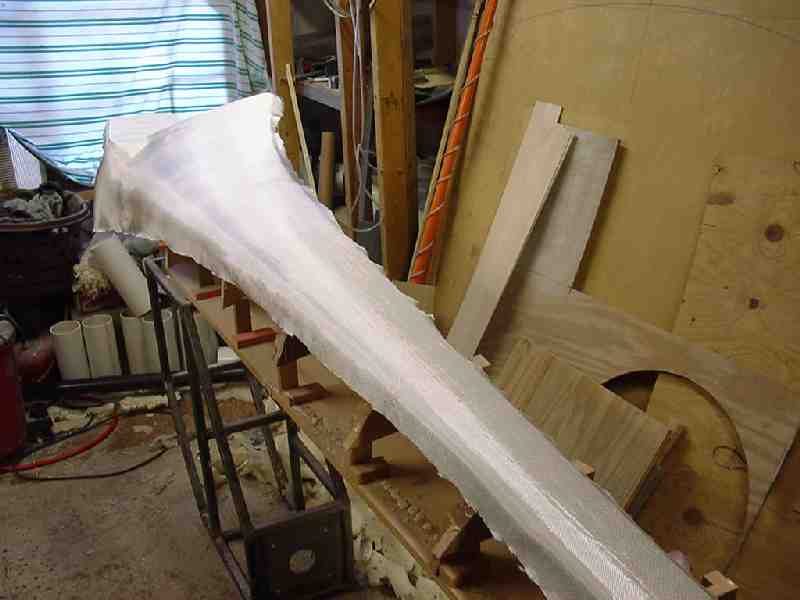
After sanding and filling, I got busy with the fiberglass and resin.
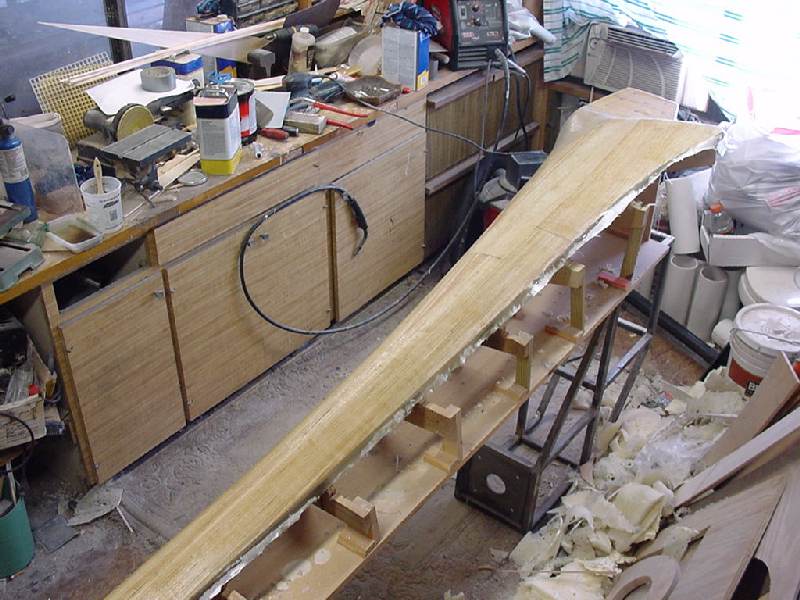
Starting to look like something now.
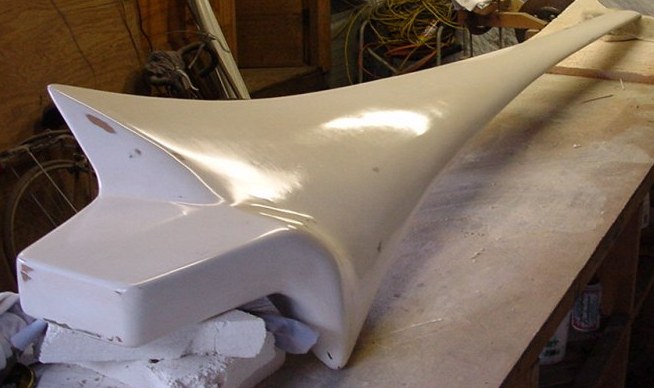
Lets skip ahead, past all the itchy fiberglass sanding, messy gelcoat applications
and dusty gelcoat sanding and go right to the waxing. Ooooohhh!
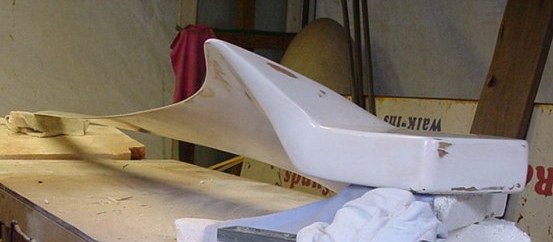
Twist & taper...
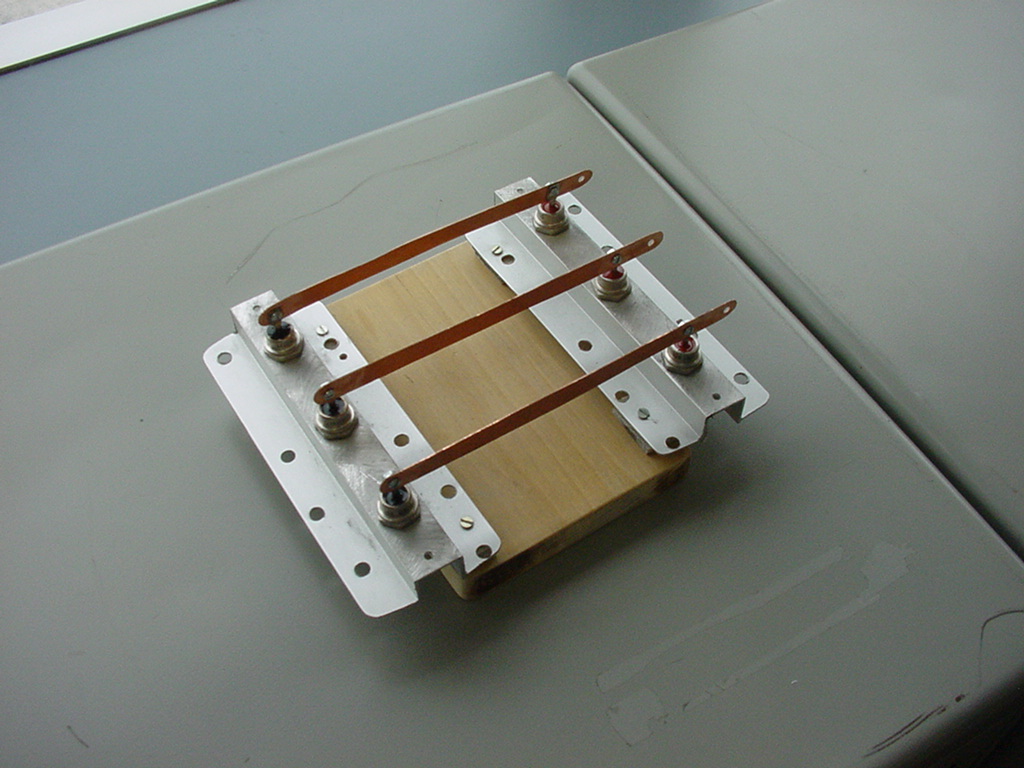
Homade 3-phase bridge rectifier from 6 50A/600V stud diodes and some shop scraps
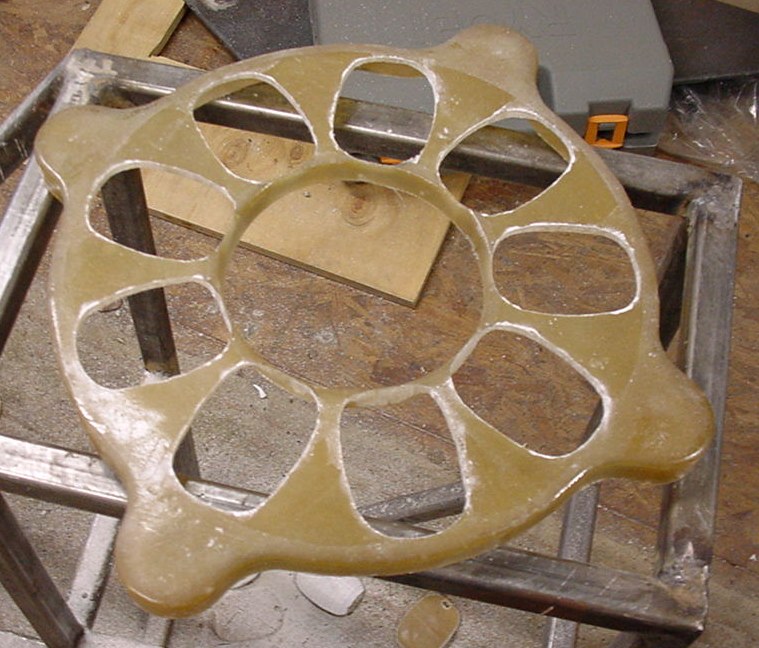
Coil cutouts in the stator plate
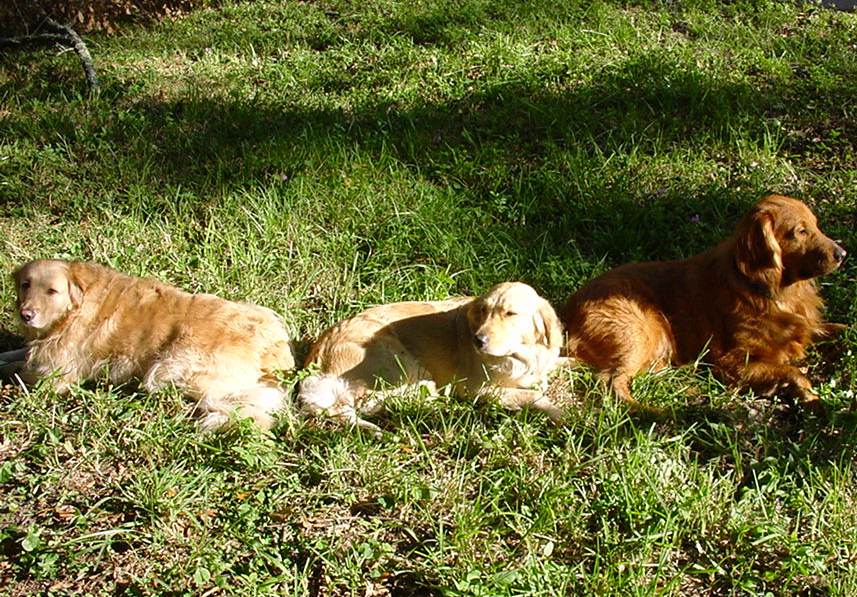
...and as always, the team of project supervisors
The plug is finished and waxed. I am now making the flange or "shadowbox" that goes around the entire periphery. When the gelcoat for the mold proper is sprayed, it and the fiberglass to follow will overlap onto the flange area and be trimmed along the outer edge of the flange. Doing this automatically provides a flange surface for the opposite half of the mold when it is layed up.
The batteries are coming along slowly, testing and charging and cherry picking the best cells to make up new batteries with. Finally found out what "battery oil" was after a good deal of time on the internet- just pure mineral oil from the drug store. Not cheap at $8.00 a quart, which is enough to do 9 cells at the recomended level.
Be safe, be happy & I'll report in again when I get some more done