Kevin L wrote:
You should try super glue, I hear it works well in these applications as well.
Well, I tried it and want to warn any readers of this thread to not follow Kevin's advice. I superglued three pieces together, supported it on each end and went to stand on the beam. It broke apart and I fell on my! But the braised beam was not only strong enough to stand on, I also jumped up and down on it with my considerable overweightage and it held together just fine.
Still, braising was pretty slow so I got set up my flux welder for MIG and got a bottle of argon and went at it... Now this is just my second welding project; the first was the tail for wind mill. It took a lot of fiddling to get all the settings right but I think the welding is going pretty good now. Here's a pic -
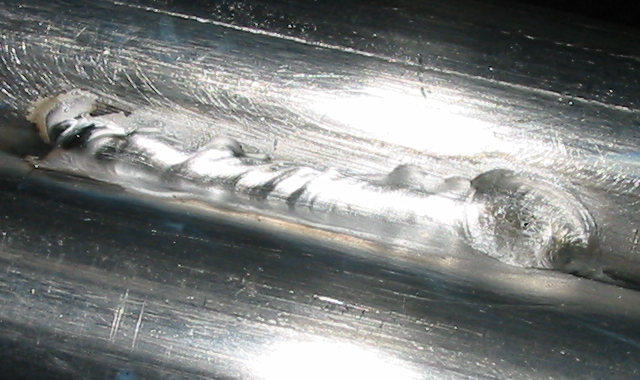
There are three roughly two inch long welds on each of the three sides for a total of nine welds per leg section.
I changed the the overlap pattern slightly that I'll be using to join the sections. Previously, I only had one tube staggered, now they all are. The notion is that I'll insert a short piece of (steel) tubing into each end to enable bolting the legs sections together without any bolts interfering with other bolts. Here's a picture of the end of a leg section -
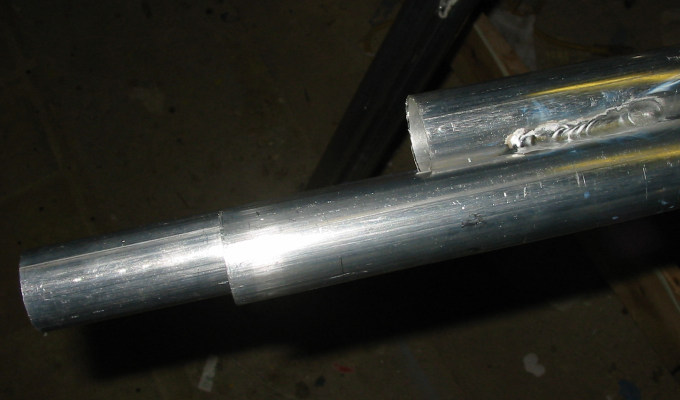
As far as designing a windmill tower, I've googled and studied lots of pictures of windmill towers. I've gotten a notion of generic proportions and bracing from them. One question the pictures left me with, though, was whether to make a three or four sided tower. And what's the difference anyway? Well, I think I found the answer!
This page: SIZING CONCRETE PIERS FOR TOWER LEGS is a real goldmine. (Basically, you'd need twice the shear strength in the legs and twice the diameter in the footings for a three sided tower that you would need in a four sided tower. Even so, I'm leaning towards a three sided tower. I don't pretend to follow the "soil science" but I can do the math and it tells me that I can do the footings for a three sided tower (and have a nice safety factor) with a the 12" auger that I can rent from the hardware store down the street.
- Ed.